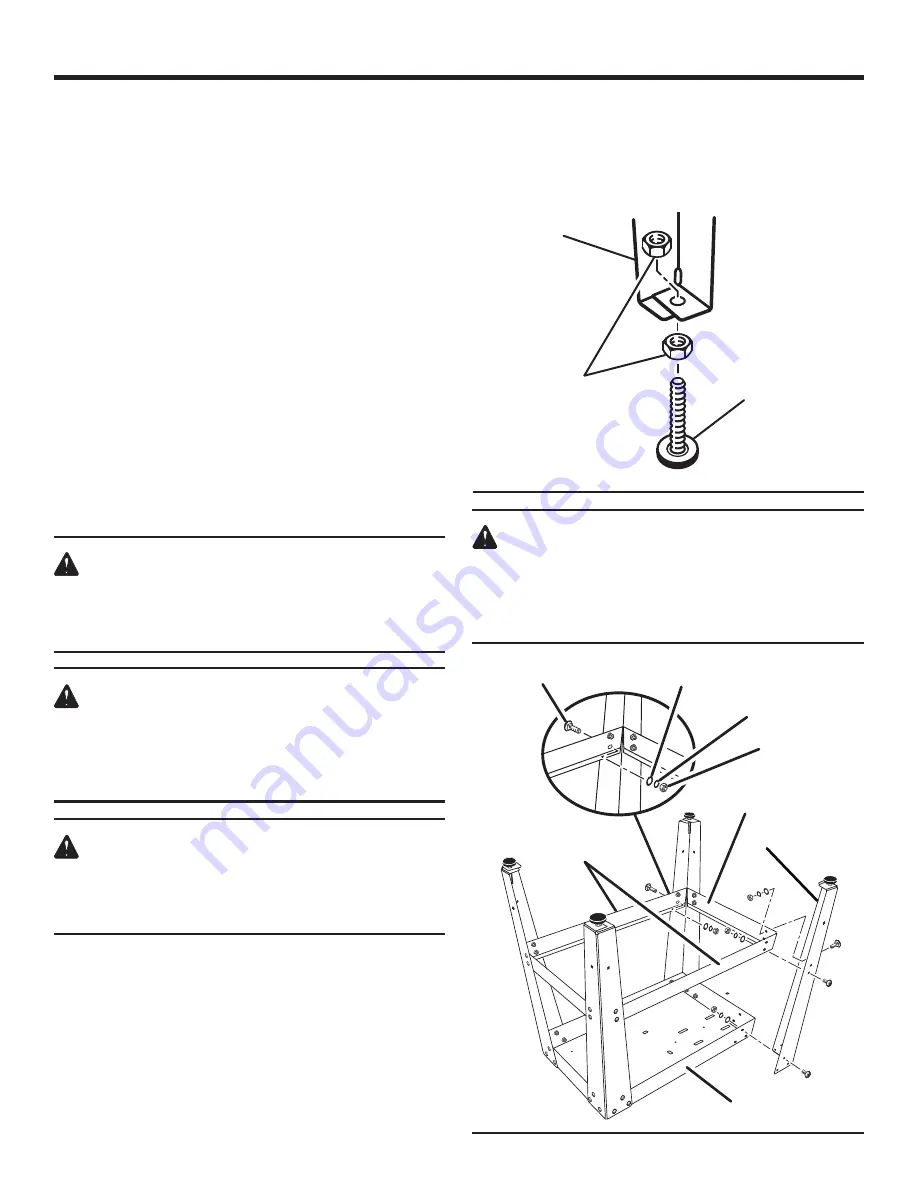
15
ASSEMBLY
UNPACKING
This product requires assembly.
n
Carefully remove the tool and any accessories from the
box. Place it on a level work surface.
NOTE:
This tool is heavy. To avoid back injury, lift with
your legs, not your back, and get help when needed.
n
Inspect the tool carefully to make sure no breakage or
damage occurred during shipping.
n
Do not discard the packing material until you have
carefully inspected the tool, identified all loose parts,
and satisfactorily operated the tool.
n
Remove the protective oil that is applied to all unpainted
metal surfaces. Use any ordinary household type grease
and spot remover.
n
Apply coat of paste wax to the saw table.
n
The saw is factory set for accurate cutting. After assem-
bling it, check for accuracy. If shipping has influenced
the settings, refer to specific procedures explained in the
operation and maintenance sections of this manual.
n
If any parts are damaged or missing, please call
1-866-539-1710 for assistance.
WARNING:
If any parts are missing, do not operate this tool
until the missing parts are replaced. Failure to
do so could result in possible serious personal
injury.
WARNING:
Do not attempt to modify this tool or create
accessories not recommended for use with this
tool. Any such alteration or modification is misuse
and could result in a hazardous condition leading
to possible serious personal injury.
WARNING:
Do not connect to power supply until assembly is
complete. Failure to comply could result in
accidental starting and possible serious personal
injury.
ATTACHING LEVELING FEET
See Figure 10.
n
Locate the following items:
4 leveling feet
8 hex nuts, (3/8-16)
n
From the loose parts find the following items:
4 legs
n
Thread a hex nut on each of the leveling feet and screw
it down towards the rubber foot.
n
Put the leveling feet through the holes in the bottom of
each leg.
n
Thread another hex nut on each of the leveling feet and
hand tighten until they are next to the bottom support
of the leg.
Fig. 10
LEG
HEX NUTS
LEVELING FOOT
WARNING:
To reduce the risk of injury from unexpected saw
or work movement, leveling feet must be adjusted
so that saw does not rock. After the band saw
has been attached to the leg stand, it will be
necessary to adjust the leveling feet.
Fig. 11
LEG
LEG BRACE
(LONG)
LEG BRACE
(SHORT)
BASE
HEX NUTS
LOCK WASHERS
WASHERS
CARRIAGE
BOLT
Summary of Contents for BS14002
Page 34: ...34 NOTES...