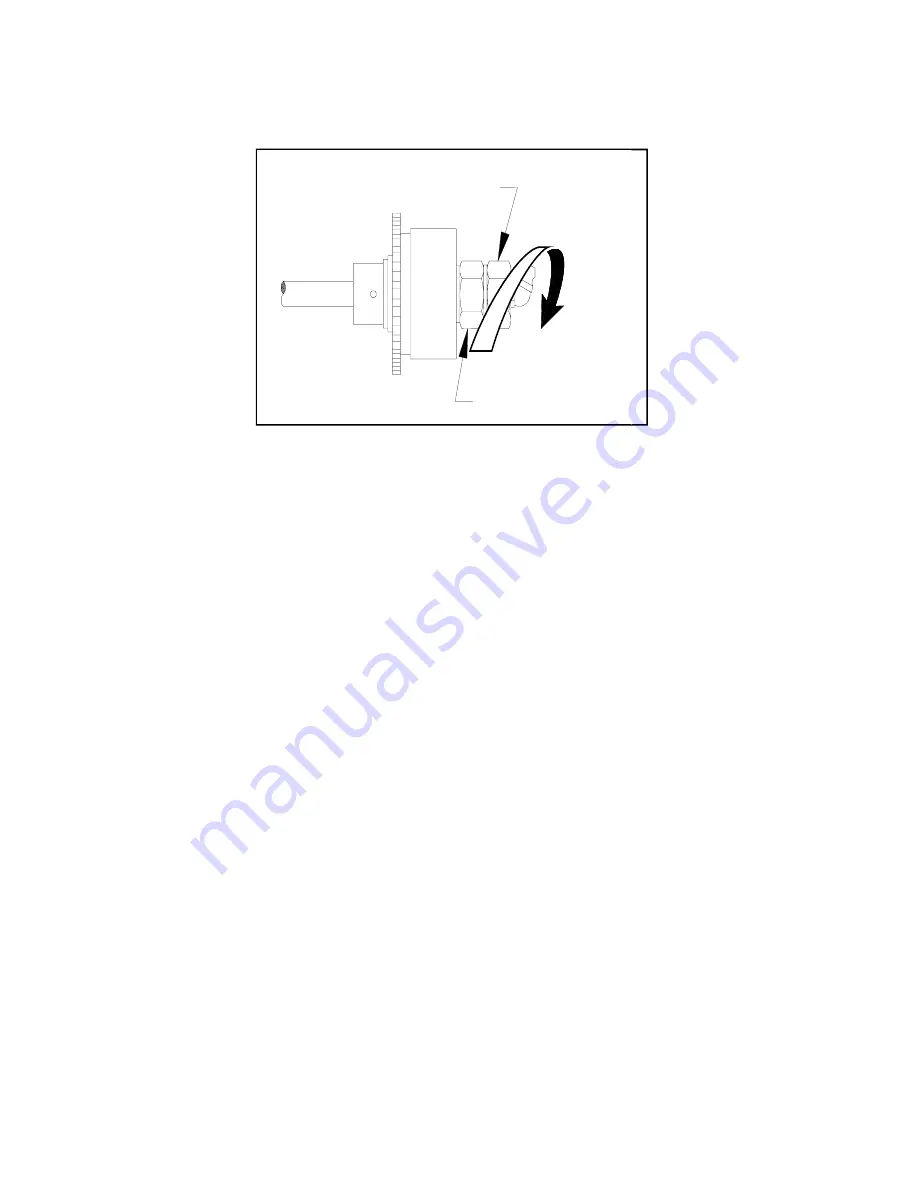
32DF9T02.C
4 - 19
5)
Rotate intermediate shaft until clutch slips. Maximum torque occurs at point where clutch
first begins to slip
. Breakaway must occur between 24–28 ft-lbs.
ADJUST:
1)
Refer to
Figure 4-19
. Do the following, if clutch adjustment is necessary:
2)
Loosen 15/16" jam nut.
3)
Rotate nut clockwise to increase torque, or counter-clockwise to decrease torque. Adjust in
small increments and check breakaway torque each time.
4)
Hold adjusting nut and tighten jam nut to 40–50 ft-lbs.
5)
Refer to Drive Chain Installation and Adjustment sections and install both drive chains.
4.
INTERMEDIATE SHAFT AND FINAL DRIVESHAFT
The intermediate shaft transfers power from primary drive chain to final drive chain. The final drive-
shaft transfers power from final drive chain to pinion gears. The pinion gears mesh with gear track (at-
tached to inside of enclosure).
a.
Intermediate Shaft and Final Driveshaft Removal
INTERMEDIATE SHAFT–
1)
Refer to Torque Limiting Clutch Removal section and remove clutch assembly.
2)
Refer to
Figure 4-17
. Slide intermediate shaft assembly out of intermediate shaft support.
3)
Remove washer from shaft. Remove roll pin fastening intermediate shaft sprocket to inter-
mediate shaft, and remove sprocket.
4)
Remove bushings from intermediate shaft support; replace, if necessary.
FINAL DRIVESHAFT–
1)
Refer to Carriage Removal section and remove carriage from enclosure.
2)
Refer to Drive Chain Removal section and remove both drive chains.
3)
Refer to
Figure 4-17
. Remove two screws fastening intermediate shaft bracket to carriage.
Slide intermediate shaft bracket away from final driveshaft (to provide clearance for drive-
shaft removal).
4)
Remove two shoulder bolts fastening driveshaft support arms to carriage.
5)
Remove final driveshaft and support arms from carriage.
6)
Remove roll pins fastening two pinion gears and one driveshaft sprocket to final driveshaft.
7)
Twist and slide pinion gears, support arms, and sprocket off final driveshaft.
8)
Slide spacers and collar off driveshaft.
ADJUSTING NUT
JAM NUT
INCREASE
FIGURE 4-19: TORQUE LIMITING CLUTCH ADJUSTMENT
Summary of Contents for Mirage F9T
Page 32: ...32DF9T02 B 3 9 D HYDRAULIC SYSTEM DIAGRAM FIGURE 3 1 F9T HYDRAULIC SYSTEM ...
Page 35: ...32DF9T02 B 3 12 FIGURE 3 2 F9T DEDICATED ENTRY ELECTRICAL DIAGRAM SHEET 1 ...
Page 36: ...32DF9T02 B 3 13 FIGURE 3 3 F9T DEDICATED ENTRY ELECTRICAL DIAGRAM SHEET 2 ...
Page 37: ...32DF9T02 B 3 14 FIGURE 3 4 F9T STEPWELL ELECTRICAL DIAGRAM SHEET 1 ...
Page 38: ...32DF9T02 B 3 15 FIGURE 3 5 F9T STEPWELL ELECTRICAL DIAGRAM SHEET 2 ...
Page 71: ...32DF9T02 C 5 2 FIGURE 5 1 STEPWELL MODEL DECALS LOCATIONS AND PART NUMBERS ...
Page 72: ...32DF9T02 C 5 3 FIGURE 5 2 F9T DEDICATED ENTRY MODEL DECALS LOCATIONS AND PART NUMBERS ...
Page 73: ...32DF9T02 C 5 4 FIGURE 5 3 F9T PUMP BOX ASSEMBLY ...
Page 75: ...32DF9T02 C 5 6 FIGURE 5 4 F9T LIFTING FRAME ASSEMBLY ...
Page 77: ...32DF9T02 C 5 8 FIGURE 5 10 F9T ENCLOSURE ASSEMBLY TOP BOTTOM ...
Page 79: ...32DF9T02 C 5 10 FIGURE 5 6 F9T PLATFORM ASSEMBLY DEDICATED ENTRY ...
Page 81: ...32DF9T02 C 5 12 FIGURE 5 7 F9T PLATFORM ASSEMBLY STEPWELL ...
Page 83: ...32DF9T02 C 5 14 FIGURE 5 8 F9T PLATFORM ASSEMBLY LEFT SIDE DETAIL ...
Page 85: ...32DF9T02 C 5 16 FIGURE 5 9 F9T PLATFORM ASSEMBLY RIGHT SIDE DETAIL ...
Page 87: ...32DF9T02 C 5 18 FIGURE 5 10 F9T BRIDGEPLATE ASSEMBLY DEDICATED ENTRY ...
Page 89: ...32DF9T02 C 5 20 FIGURE 5 11 F9T BRIDGEPLATE ASSEMBLY STEPWELL ...
Page 91: ...32DF9T02 C 5 22 FIGURE 5 12 F9T CARRIAGE ASSEMBLY SHEET 1 ...
Page 92: ...32DF9T02 C 5 23 FIGURE 5 13 F9T CARRIAGE ASSEMBLY SHEET 2 ...
Page 94: ...32DF9T02 C 5 25 This page intentionally left blank ...
Page 95: ...32DF9T02 C 5 26 FIGURE 5 14 F9T PENDANT ASSEMBLY ...