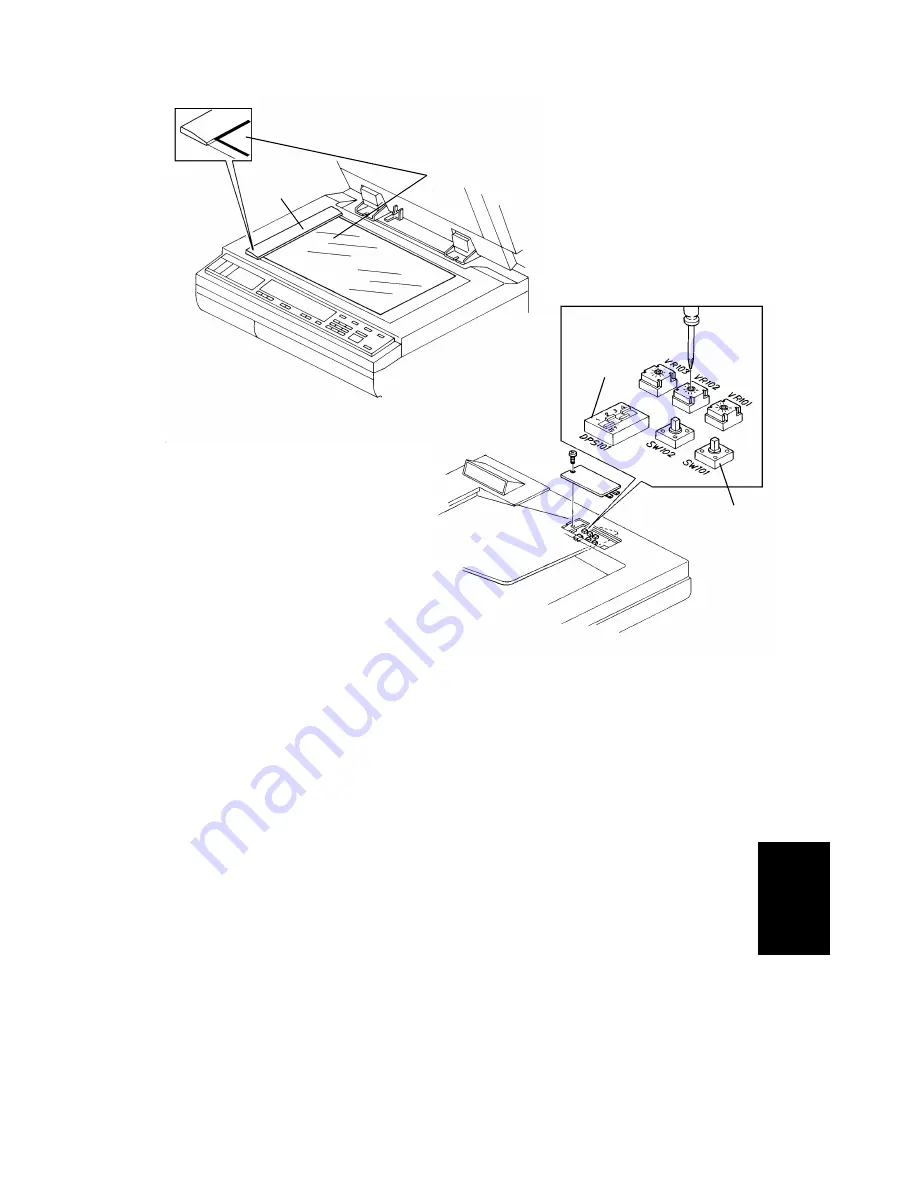
25. Confirm the original registration in two-sided original mode as follows:
NOTE: a) An original should stop pressed against the left scale [A] in DF
two-sided original mode.
b) The position of the original select switch does not matter.
1) Set DIP SW101 [B] on the main control board as follows:
ON: 101–2, 4
OFF:101–1, 3
2) Set a sheet of A3/11" x 17" paper [C] on the DF then press SW 101 [D]
to feed the paper into the DF belt section.
3) When the paper stops on the exposure glass after the inversion, open
the DF slowly so that the paper does not move from the stop position.
4) Confirm that the paper has stopped against the left scale.
[B]
[D]
[A]
[C]
ARDF
12 February 1992
INSTALLATION
27
Summary of Contents for FT5233
Page 1: ...FT5233 5433 5733 SERVICE MANUAL...
Page 4: ...SECTION 1 OVERALL MACHINE INFORMATION...
Page 29: ...SECTION 2 DETAILED SECTION DESCRIPTIONS...
Page 147: ...SECTION 3 INSTALLATION...
Page 177: ...SECTION 4 SERVICE TABLES...
Page 223: ...6 Duplex Tray PREVENTIVE MAINTENANCE SCHEDULE 12 February 1992 4 46...
Page 230: ...SECTION 5 REPLACEMENT AND ADJUSTMENT...
Page 349: ...SECTION 6 TROUBLESHOOTING...
Page 392: ...80 35 FRAME SECTION 4 A069 A073 A074...
Page 394: ...82 36 DRIVE SECTION 1 A069 A073 A074...
Page 396: ...84 37 DRIVE SECTION 2 A069 A073 A074...
Page 398: ...86 38 ELECTRICAL SECTION 1 A069 A073 A074...
Page 400: ...88 39 ELECTRICAL SECTION 2 A069 A073 A074...
Page 402: ...90 40 ELECTRICAL SECTION 3 A069 A073 A074...
Page 404: ...92 41 ELECTRICAL SECTION 4 A069 A073 A074...
Page 406: ...94 42 DUPLEX UNIT 1 A074...
Page 408: ...96 43 DUPLEX UNIT 2 A074...
Page 410: ...98 44 DUPLEX UNIT 3 A074...
Page 412: ...100 45 MAIN CONTROL BOARD A069 A073 A074...
Page 413: ...101 45 MAIN CONTROL BOARD A069 A073 A074...
Page 414: ...102 45 MAIN CONTROL BOARD A069 A073 A074...
Page 417: ...105 46 MEMORY BOARD A069 A073 A074...
Page 419: ...107 47 AC HARNESS A069 A073 A074...
Page 421: ...109 48 DC HARNESSTYPE 2 A069 A073 A074...
Page 423: ...111 49 DC HARNESSTYPE 4 A069 A073 A074...
Page 425: ...113 50 FUSING UNIT HARNESS A069 A073 A074...
Page 427: ...115 51 LCT HARNESS A073 A074...
Page 429: ...117 52 DECAL AND DOCUMENT A069 A073 A074...
Page 430: ...118 52 DECAL AND DOCUMENT A069 A073 A074...
Page 431: ...119 52 DECAL AND DOCUMENT A069 A073 A074...
Page 432: ...120...
Page 434: ...122 53 SPECIALTOOL A069 A073 A074...
Page 436: ...PARTS INDEX...
Page 465: ...CS120 A327...
Page 467: ...2 1 EXTERIOR A327...
Page 469: ...4 2 TRANSPORT SECTION A327...
Page 471: ...6 3 SORTER MAIN BOARD A327...
Page 473: ...8 4 SORTER MAIN HARNESS A327...
Page 475: ...10 5 DECAL AND DOCUMENT A327...
Page 477: ...PARTS INDEX...
Page 482: ...2 LOCATION OF UNIT December 1 90...
Page 483: ...3 1 MIDI SORTER 1 A411...
Page 485: ...5 2 MIDI SORTER 2 A411...
Page 488: ...8 3 SORTER BOARD A411...
Page 490: ...10 4 SORTER HARNESS A411...
Page 492: ...PARTS INDEX...
Page 497: ...CS2090 A423 This parts catalog includes MB No 1 to 4...
Page 499: ...2 1 SORTER A423...
Page 502: ...5 2 BIN MOTOR BOARD A423...
Page 504: ...7 3 SORTER HARNESS A423...
Page 506: ...9 4 DECAL AND DOCUMENT A423...
Page 508: ...PARTS INDEX...
Page 512: ...DF56 A497 This parts catalog includes MB No 1 to 11...
Page 514: ...2 LOCATION OF UNIT...
Page 515: ...3 1 EXTERIOR A497...
Page 517: ...5 2 ORIGINAL FEED SECTION 1 A497...
Page 519: ...7 3 ORIGINAL FEED SECTION 2 A497...
Page 521: ...9 4 TRANSPORT SECTION A497...
Page 523: ...11 5 INVERTER AND EXIT SECTION A497...
Page 525: ...13 6 ELECTRICAL SECTION A497...
Page 527: ...15 7 MAIN BOARD A497...
Page 528: ...16...
Page 531: ...19 8 MAIN HARNESS A497...
Page 533: ...21 9 INTERFACE HARNESS A497...
Page 535: ...23 10 FEED IN MOTOR HARNESS A497...
Page 537: ...25 11 DECAL AND DOCUMENT A497...
Page 539: ...PARTS INDEX...
Page 547: ...MR20 A952 This parts catalog includes MB No 1 to 3...
Page 549: ...2 1 MENU READER A952...
Page 551: ...4 2 DECAL AND DOCUMENT A952...
Page 553: ...PARTS INDEX...
Page 555: ...PS140 250 A325 A326...
Page 557: ...2 LOCATION OF UNIT December 1 90...
Page 558: ...3 LOCATION OF UNIT...
Page 559: ...4 1 EXTERIOR A325 A326...
Page 561: ...6 2 VERTICALTRANSPORT SECTION A326...
Page 563: ...8 3 VERTICALTRANSPORT SECTION A325...
Page 565: ...10 4 PAPER FEEDTRAY A325 A326...
Page 567: ...12 5 PAPER FEED SECTION A325 A326...
Page 569: ...14 6 TRAY LIFT SECTION A325 A326...
Page 571: ...16 7 DRIVE SECTION A325 A326...
Page 573: ...18 8 FRAME SECTION A325 A326...
Page 575: ...20 9 INTERFACE BOARD A325 A326...
Page 577: ...22 10 MAIN HARNESS A325...
Page 579: ...24 11 MAIN HARENSS A326...
Page 581: ...26 12 DECAL AND DOCUMENT A325 A326...
Page 583: ...28 13 SPECIALTOOL A325 A326...
Page 585: ...PARTS INDEX...
Page 592: ...RE12 A916...
Page 594: ...2 1 EDITOR BOARD A916...
Page 596: ...4 2 DECAL AND DOCUMENT A916...
Page 598: ...PARTS INDEX...
Page 600: ...SORTER ADAPTER TYPE G A328...
Page 602: ...2 December 1 90 1 SORTER ADAPTERTYPE G A328...
Page 604: ...PARTS INDEX...
Page 606: ...ST22 A366...
Page 608: ...2 LOCATION OF UNIT...
Page 609: ...3 LOCATION OF UNIT...
Page 610: ...4 1 EXTERIOR A366...
Page 612: ...6 2 TURN GATE A366...
Page 614: ...8 3 VERTICALTRANSPORT SECTION A366...
Page 616: ...10 4 DIAGONALTRANSPORT SECTION A366...
Page 618: ...12 5 DISTRIBUTIONTRANSPORT SECTION A366...
Page 620: ...14 6 JOGGER A366...
Page 622: ...16 7 BIN SIDE PLATE DRIVE A366...
Page 624: ...18 8 STAPLE UNIT DRIVE 1 A366...
Page 626: ...20 9 STAPLE UNIT DRIVE 2 A366...
Page 628: ...22 10 STAPLE UNIT A366...
Page 630: ...24 11 DRIVE AND ELECTRICAL SECTION 1 A366...
Page 632: ...26 12 DRIVE AND ELECTRICAL SECTION 2 A366...
Page 634: ...28 13 MAIN CONTROL BOARD A366...
Page 635: ...29 13 MAIN CONTROL BOARD A366...
Page 636: ...30 13 MAIN CONTROL BOARD A366...
Page 639: ...33 14 AC HARNESS A366...
Page 641: ...35 15 UPPER DC HARNESS A366...
Page 643: ...37 16 LOWER DC HARNESS A366...
Page 645: ...39 17 GRIPPER HARNESS A366...
Page 647: ...41 18 DECAL AND DOCUMENT A366...
Page 649: ...PARTS INDEX...
Page 660: ...AUTO REVERSE DOCUMENT FEEDER Machine Code A497...
Page 679: ...1 ARDF 12 February 1992 1...
Page 680: ...2 12 February 1992 2...
Page 681: ...3 ARDF 12 February 1992 3...
Page 682: ...4 12 February 1992 4...
Page 683: ...5 ARDF 12 February 1992 5...
Page 684: ...6 12 February 1992 6...
Page 685: ...7 ARDF 12 February 1992 7...
Page 686: ...8 12 February 1992 8...
Page 718: ...10 BIN SORTER MICRO Machine Code A327...
Page 736: ...20 BIN SORTER MIDI Machine Code A411...
Page 756: ...20 BIN SORTER MINI Machine Code A423...
Page 777: ...PAPER TRAY UNIT Machine Code A325 A326...
Page 801: ...SORTER STAPLER Machine Code A366...
Page 871: ...MENU READER Machine Code A952...
Page 888: ...FT5233 5433 5733 SERVICE MANUAL...
Page 889: ...SECTION 1 OVERALL MACHINE INFORMATION...
Page 890: ...SECTION 2 DETAILED SECTION DESCRIPTIONS...
Page 891: ...SECTION 3 INSTALLATION...
Page 892: ...SECTION 4 SERVICE TABLES...
Page 893: ...SECTION 5 REPLACEMENT AND ADJUSTMENT...
Page 894: ...SECTION 6 TROUBLESHOOTING...
Page 895: ...AUTO REVERSE DOCUMENT FEEDER Machine Code A497...
Page 896: ...EDITOR Machine Code A916...
Page 897: ...10 BIN SORTER MICRO Machine Code A327...
Page 898: ...20 BIN SORTER MINI Machine Code A423...
Page 899: ...20 BIN SORTER MIDI Machine Code A411...
Page 900: ...PAPER TRAY UNIT Machine Code A325 A326...
Page 901: ...MENU READER Machine Code A952...
Page 902: ...SORTER STAPLER Machine Code A366...
Page 907: ...Symbol Name Index No P to P H3 Tray 3 option 33...