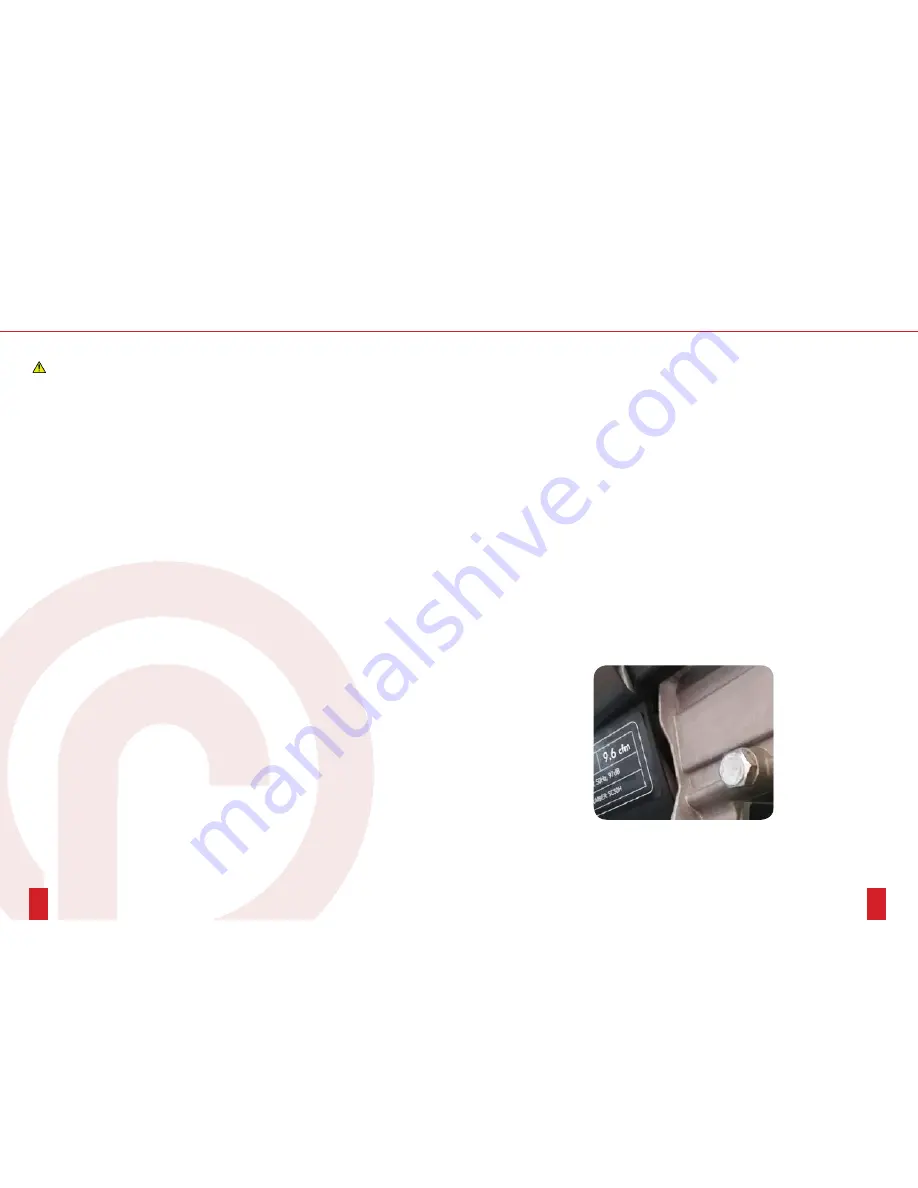
SAFETY PRECAUTIONS
MAINTENANCE
2
•
Never unscrew any connecting parts while the tank is
still under pressure.
•
Never disassemble any electrical parts before
disconneting the electrical plug.
•
Always use caution when adjusting the safety valve.
•
Never use the compressor when the volatage is too low
or too high.
•
Never use electrical cable more than 5m long with less
than a 1.5 mm section rated to 16A.
•
Never disconnect the plug to stop the compressor, turn
the switch to the OFF position.
•
If the release valve does not work when the motor is
stopped find the cause immediately to prevent damage to
the motor.
•
Before restarting the motor by pressing the RESET
button check the air compressor for problems and check
the pressure in the air tank to ensure it is under 0.8Mpa.
•
Disconnect the plug to cut off the power supply and open
the outlet valve and discharge all the air in the air tank
after use.
1.
Before any maintenance operation stop the air compressor,
cut off the power supply and discharge all the air in the tank.
2.
Clean the crank case and renew lubricating oil after the
first10 working hours. Check the oil through the oil level
sightglass after every 20 working hours and replenish if
necessary; you can replenish by inbolting the sump bolt, and
srain off any old oil.
3.
Have the safety valve and pressure gauge checked by a
certified repair centre every 6 months to ensure they are in
correct working condition.
4.
Make sure there is no rust on the air tank and the air tank is
not damaged.
5.
Have the thickness of the air tank checked by a certified
repair centre every year to ensure the tank thinkness is not
less than 2.1mm.
CAUTION
MAINTENANCE PROCEDURE
Sump bolt
11
10