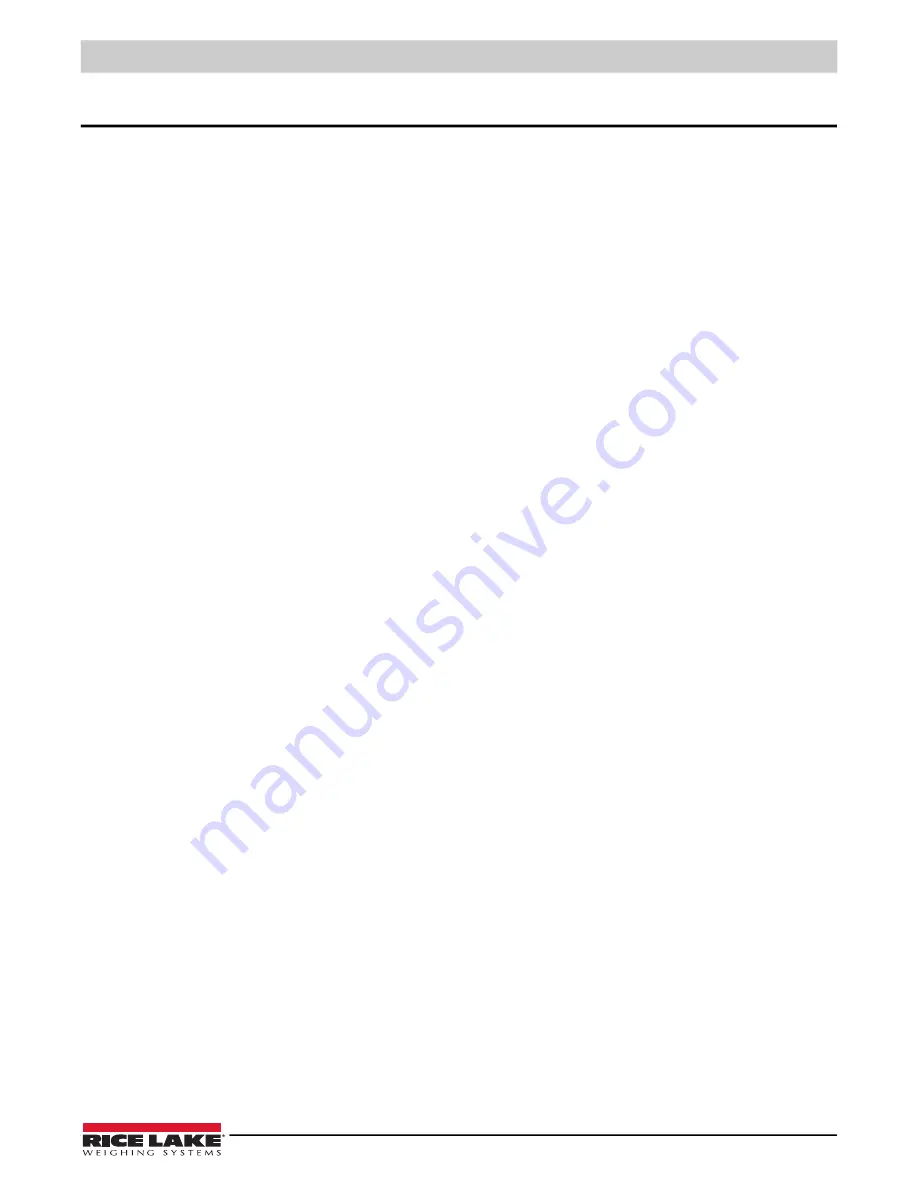
Preventative Maintenance
© Rice Lake Weighing Systems
●
All Rights Reserved
29
10.0 Preventative Maintenance
A preventative maintenance program is a key element in maximizing the life, performance and accuracy of truck scales.
Maintenance frequency is directly related to the daily truck volume and axle loads of the vehicles being weighed. At a minimum,
inspections are recommended every six months depending on equipment usage. A comprehensive program would consist of
inspections in the following areas:
• Weighbridge
• Foundation
• Load cells
• Junction box
• Grounding
• Calibration and testing
10.1 Weighbridge
Proper weighbridge inspection is essential to ensure accuracy and consistent performance of a truck scale.
• Visual inspection of the top-deck surface, including welds, should be performed on each maintenance visit
• Areas beneath the bridge should be inspected for potential mechanical bindings as a result of debris accumulation, loose
bolts and misalignment of the suspension system
• Debris or ice buildup between the approach bulkhead and the end of the scale, as well as between the scale modules,
should also be checked and removed
• Paint coating conditions on the scale should be examined and noted yearly
• Depending on weighbridge design, geographical location, load material and environmental factors, removing the
weighbridge from the foundation for sandblasting and paint may be required
• Excessive corrosion could also indicate complete replacement of the weighbridge
10.2 Foundation
A truck scale is only as good as the foundation on which it rests. Keeping the foundation clean and well drained provides more
accurate and dependable vehicle weighing.
• A quick visual check of sump pumps and drains should be done at least once a month
• The condition of the concrete piers or slab and concrete approaches are important for maximum equipment
performance; approaches to and from the scale should be level to ensure a smooth transition from the approach to the
scale; steel coping or trim on the approach head walls and/or pit walls should be checked for proper anchoring or wear
• Areas around the load cells should be inspected for binding due to debris build-up; a minimum clearance of 0.75'' should
be provided between the weighbridge and the headwall and side walls when applicable
• Any cracks in the concrete or evidence of heaving due to frost or poor soil conditions should be recorded and resolved
immediately; foundation issues are common causes for inaccurate scale performance
10.3 Load Cells
Load cells should be inspected for damage to cables, cracked or loose connectors, proper alignment of suspension links and
any accumulation of debris around the load cell stand-assembly. All cable connections should be checked and any corrosion
and service-related cable splices should be removed from the system.
10.4 Junction Box
The junction box should be opened and checked for any moisture or corrosion on internal circuitry. The PreVent™ filter should
be changed on an annual basis. Desiccant packs inside the box should be examined and exchanged on an annual basis. Cable
connectors should be inspected and checked for tight fittings.