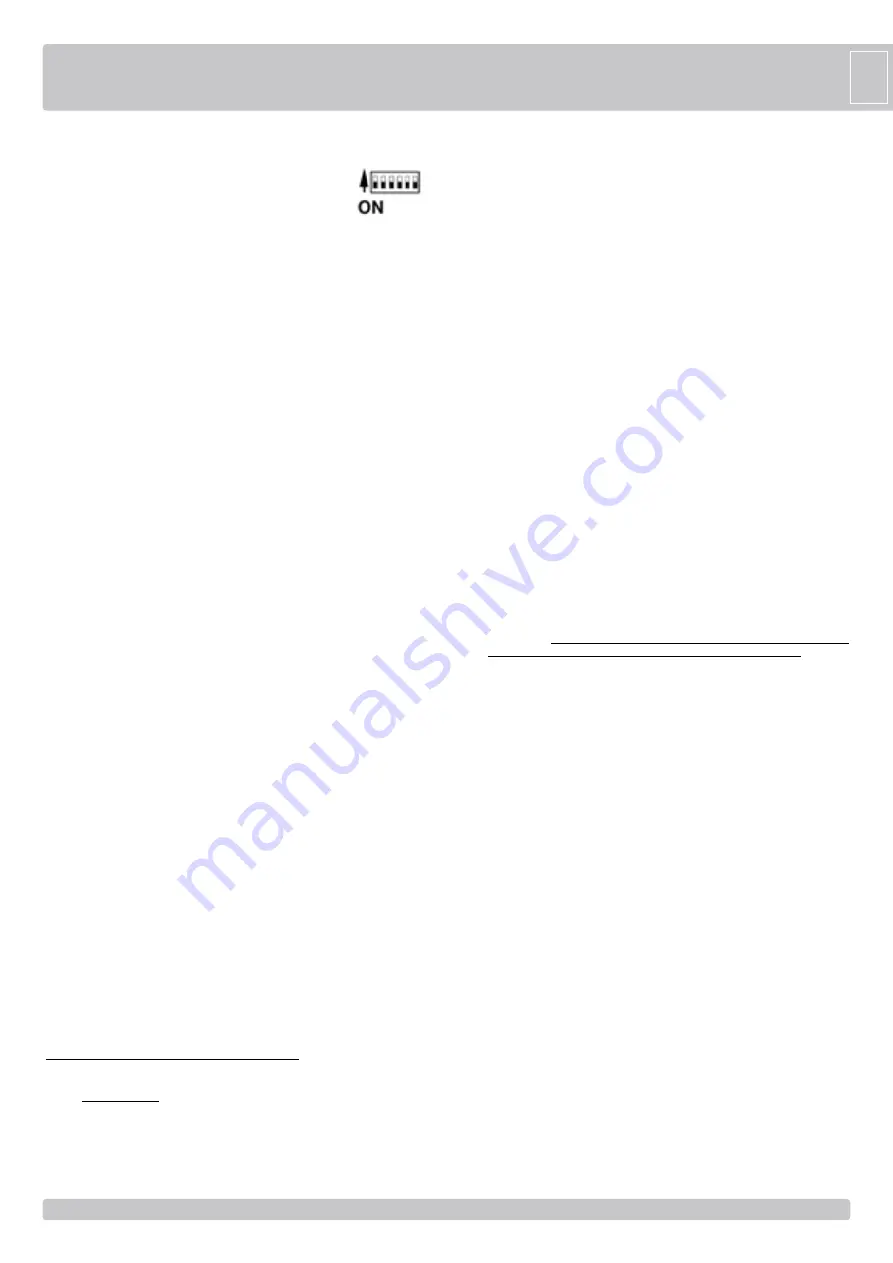
29
29
G
B
POINT B
- SETTINGS
DIP 1 (ON) MOTOR ROTATION DIRECTION CHECK (See Point
C
)
DIP 2 (ON)
PROGRAMMING (See Point D)
DIP 1-2
STORAGE/DELETION OF RADIO CODES FOR COMPLETE
OPENING (DIP 1 ON followed by DIP 2 ON) (POINT G)
ONLY FOR CRX MODELS
DIP 1-3
STORAGE/DELETION OF RADIO CODES FOR PEDESTRIAN OPENING
(DIP 1 ON followed by DIP 3 ON) (POINT H) ONLY FOR CRX MODELS
DIP 2-1 PROGRAMMING OF THE PEDESTRIAN OPENING (See Point F)
DIP 3
ON - Automatic Closing ENABLED
OFF - Automatic Closing DISABLED
DIP 4
ON - Photocells active only in closing
OFF - Photocells always active
DIP 5
ON - blinker pre-flashing
OFF - blinker normal-flashing
DIP 6
OFF - STEP BY STEP
Single pulse contact (K BUTT)
Pedestrian button (PED BUTT)
Radio Receiver command
ON - AUTOMATIC
Single pulse contact (K BUTT)
Pedestrian button (PED BUTT)
Radio Receiver command
DIP 7
ON - low speed in approaching ENABLED
OFF - low speed in approaching DISABLED
DIP 8
ON - electric lock command ENABLED
OFF - electric lock command DISABLED
DIP 9
ON - Hammering on complete close position to ease Manual Release
- Hammering before opening to ease electric lock unlocking
OFF - no impulse
DIP 10
ON - Extra thrust when reached closing position to make sure that the
mechanical bolt is fixed into the ground
OFF - no impulse
DIP 11
ON - black out function ENABLED (See chart 1)
OFF - black out function DISABLED
DIP 12
ON - close command after the transit through the photocell ENABLED
OFF - close command after the transit through the photocell DISABLED
DIP 13
ON - safety strip self-test ENABLED
OFF - safety strip self-test DISABLED
DIP 14
OFF OBLIGATORY FOR R50 MOTOR
DIP 15
ON OBLIGATORY FOR R50 MOTOR
DIP 16
ON OBLIGATORY FOR R50 MOTOR
JP 17
OPEN JUMPER 1 motor (M1) - 1 leaf
CLOSE JUMPER 2 motors (M1 and M2) - 2 leaves
JP1 =>
Pay attention that the jumper is inserted!
JP2 =>
Pay attention that the jumper is inserted!
JP3 =>
Pay attention that the jumper is inserted!
TORQUE TR1 Electronic regulator for motor torque
Adjustment of motor torque is carried out using the TORQUE Trimmer which varies
the output voltage to the head/s of the motor/s (turn clockwise to increase torque).
This torque control is activated after 2 seconds form any manoeuvre begging, whereas
the motor is turned on at full power to guarantee the starting at the manoeuvre begging.
PAY ATTENTION: IF THE TORQUE TRIMMER SETTING IS CHANGED, IT IS
PREFERABLE TO REPEAT THE TIME PROGRAMMING.
LOW SPEED TR2 Electronic regulator for low speed on approach
Adjustment of low speed is carried out using the LOW SPEED Trimmer which varies
the output voltage to the head/s of the motor/s (turn clockwise to increase speed).
Adjustment is carried out to establish the correct speed at the completion of opening
and closing, depending on the structure of the gate, or if there is any light friction
that could compromise the correct working of the system. The low speed is activated
(DIP7 OFF) when the gate leaf is 0.50-0.60 meters away from the complete close or
open position.
ATTENTION: WHEN USING HYDRAULIC OPERATORS
When using the hydraulic operators the deceleration phase may not operate
correctly; in that case it is advisable to disable the feature of the deceleration by
putting DIP 7 in the OFF mode.
LED WARNING
DL1 - programming activated (red)
DL2 - radio code programming (green) (only for CRX)
DL3 - gate opening M2 (green)
DL4 - gate closing M2 (red)
DL5 - gate opening M1 (green)
DL6 - gate closing M1 (red)
DL7 - photocell contact (NC) (red)
DL8 - safety strip contact (NC) (red)
FUSES
F1 T100mA Accessories protection fuse
F2 5A Motor protection fuse
POINT C
- MOTOR ROTATION DIRECTION CHECK
1 - Unlock the operators with the Manual Release - swing open the leaves about
halfway and lock again the operators.
2 - Turn DIP1 to ON position. The red LED DL1 starts blinking.
3 - Press the PROG button and hold it - When GREEN LEDS DL3 and DL5 are
on, the gate leaves are opening (with a phase shift of 2 seconds). Check the
leaves swinging and the opening mechanical stopper position (movement is now
performed in “man present” mode, open-close-open-etc.).
If any of the leaf closes instead of opening, release PROG button, turn off the main
power and reverse the two phase wires (V1/2 and W1/2) of the relevant motor/s.
4 - Press the PROG button and hold it to CLOSE completely the gate. When RED
LEDS DL4 and DL6 are on, the gate leaves are closing (with a phase shift of 4
seconds). Check leaves swinging and the closing mechanical stopper position.
5 - After 3 seconds motor starting and for the next 10 seconds motor working, the
torque controls automatically activated. Set the motor torque by the TORQUE
Trimmer/s which varies the output voltage to the motor/s (turn clockwise to increase
the torque).
6 - After other 10 seconds motor working, the low speed controls automatically
activated (DIP7 ON). Set the motor low speed by the LOW SPEED Trimmer to
select the gate leaf low speed in approaching.
7 - Close completely the gate.
8 - Turn DIP1 to OFF position, LED DL1 turns off.
During Point C procedure, safety devices (photocells and safetystrip) are not
active and the remote control cannot operate.
(#) In Point D, Point E and Point F procedures, all the safety devices (photocells and
safety strip) will be active, so they must be properly installed and connected to the
control board. Any changing of the safety devices input state, will stop the Point D,
Point E or Point F procedure that must be repeated from the beginning.
POINT D
- PROGRAMMING FOR 2 MOTORS (#)
1 - The gate must be fully closed.
2 - Turn
DIP2 to ON
position, LED DL1 starts blinking
3 -
Press PROG. Button
, motor M1 opens.
4 - Once reached the open position, let 1 second pass and
press the PROG button
to
cut out motor M1 (time travel of M1 has now been just stored with this operation).
5 - Motor M2 opens, automatically.
6 - Once reached the open position, let 1 second pass and
press the PROG button
to
cut out motor M2 (time travel of M2 has now been just stored with this operation).
The gap of time between now (stop of motor M2) and the next pressing of the
PROG. button (see step 7 below) will be then stored as waiting time for Automatic
Closing feature.
7 -
Press PROG. button
, M2 closes and the Automatic Closing time is stored (see
DIP3 function to enable or disable the Automatic Closing feature). The gap of time
between now (close of motor M2) and the next pressing of the PROG. button (see
step 8 below) will be stored as time delay between motor M2 and motor M1 closing,
during normal operations.
8 -
Press the PROG. button
, motor M1 closes thus setting the delay time between M2
and M1, as explained in step 7 above.
9 - The LED DL1 will turn OFF, signalling exit from the Point D procedure.
Closing of the gate will be carried out at normal speed and only on approaching
total closing at low speed (depending on the adjustment of LOW SPEED trimmer).
10 -
Turn DIP2 to OFF
position.
During Point D procedure, the safety devices (photocells and safety strip) are active.
POINT E
- PROGRAMMING FOR 1 MOTOR (M1) (#)
ATTENTION: in order to manage one motor only, OPEN JUMPER JP17.
1 - The gate must be fully closed.
2 - Turn
DIP2 to ON
position, the LED DL1 starts blinking
3 -
Press PROG. button
, the motor M1 opens.
4 - Once reached the open position, let 1 second pass and
press the PROG button
to
cut out motor M1 (time travel of M1 has now been just stored with this operation).
The gap of time between now (stop of motor M1) and the next pressing of the
PROG. button (see step 5 below) will be then stored as waiting time for Automatic
Closing feature.
5 -
Press PROG. button
, M1 closes and the Automatic Closing time is stored (see