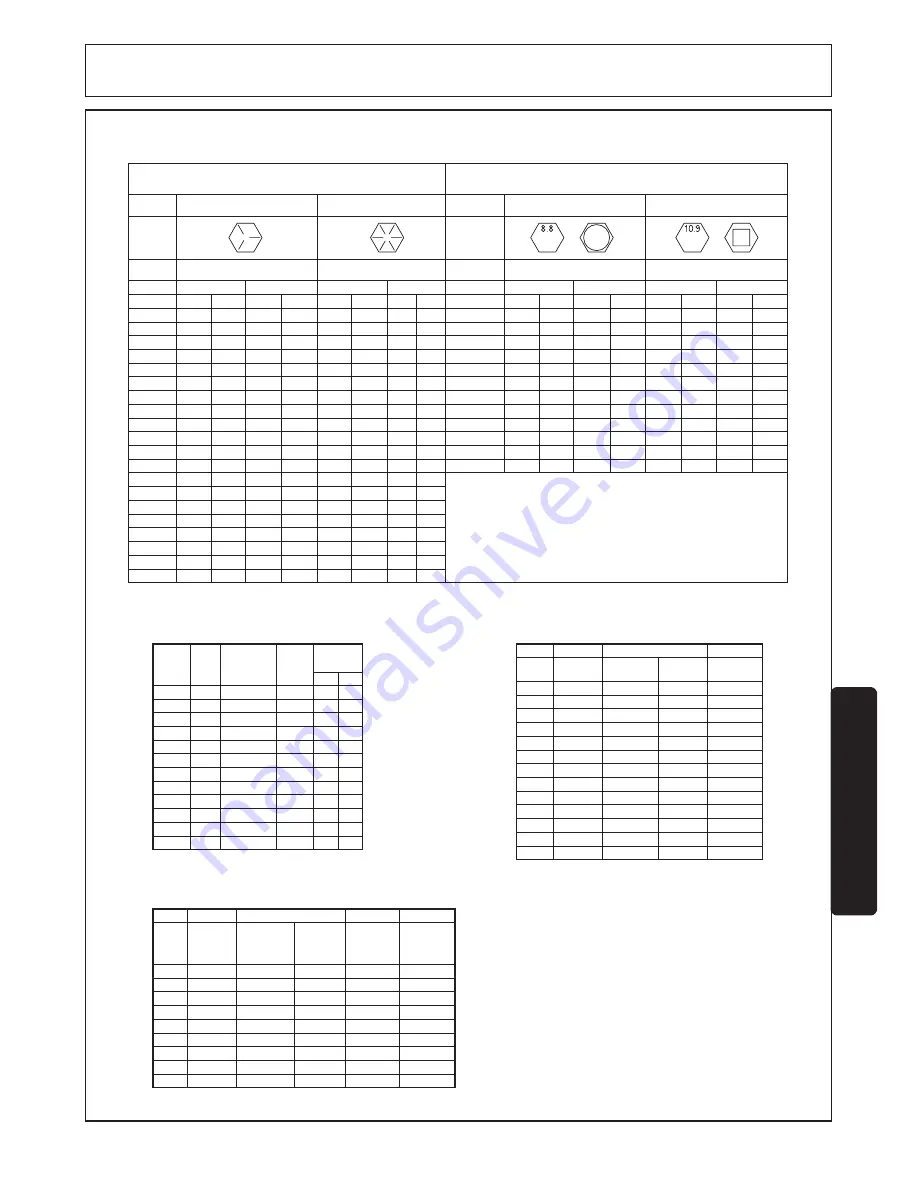
© 2004
Alamo Group Inc.
MAINTENANCE
MAINTENANCE
F-3778-12-04
Maintenance Section 5-7
GENERAL TORQUE SPECIFICATIONS
USE THE FOLLOWING TORQUES WHEN SPECIAL TORQUES ARE NOT GIVEN
AMERICAN STANDARD CAP SCREWS
METRIC CAP SCREWS
SAE
Cap
Grade
Size
Inches
MIN
MIN
MIN
MIN
MIN
MAX
MAX
MAX
MAX
MAX
MIN
MAX
MIN
MIN
MAX
MAX
FT-LBS
FT-LBS
N·m
FT-LBS
N·m
N·m
FT-LBS
N·m
Size
Millimeters
1/4-20
6.25
12
9
8
6
7.25
15
11
11
8
8.5
10
8.25
11
9.5
13
M6 x 1.00
1/4-28
8
31
23
21.5
16
9
36.5
27
27
20
11
12
10.5
14
12
16
M8 x 1.25
5/16-18
14
57
42
39
29
15
70
52
47
35
19
20
18.5
25
20
27
M10 x 1.50
5/16-24
17.5
102
75
70
52
19
123
91
84
62
23
26
23
31
25
34
M12 x 1.75
3/8-16
26
163
120
115
85
28
198
146
139
103
35
38
35
47.5
37
50
M14 x 2.00
3/8-24
31
238
176
176
130
34
293
216
214
158
42
46
41
55.5
45
61
M16 x 2.50
7/16-14
41
325
240
233
172
45
398
294
284
210
55.5
61
55
74.5
60
81
M18 x 2.50
7/16-20
51
465
343
335
247
55
577
426
408
301
69
74.5
68
92
75
102
M20 x 2.50
1/2-13
65
639
472
450
332
72
780
576
547
404
88
97.5
86
116
96
130
M22 x 2.50
1/2-20
76
812
599
573
423
84
992
732
700
517
103
114
102
138
112
152
M24 x 3.00
9/16-12
95
1217
898
863
637
105
1488
1098
1055
779
129
142
127
172
140
190
M27 x 3.00
9/16-18
111
1658
1224
1181
872
123
2027
1496
1444
1066
150
167
148
200
164
222
5/8-11
126
139
171
188
168
228
185
251
5/8-18
152
168
206
228
203
275
224
304
3/4-10
238
262
322
355
318
431
350
474
3/4-16
274
305
371
409
365
495
402
544
7/8-9
350
386
474
523
466
631
515
698
7/8-14
407
448
551
607
543
736
597
809
1-8
537
592
728
802
716
970
790
1070
1-14
670
740
908
1003
894
1211
987
1337
M30 x 3.00
10.9
8.8
Metric Class
Screw
Cap Screw
Typical
Grade ID
Markings
on Head
Typical
Grade ID
Markings
on Head
8
5
TORQUE
TORQUE
TORQUE
TORQUE
NOTE:
These values apply to fasteners as
received from supplier, dry or when lubricated
with normal engine oil. They do not apply if
special graphite or molydisulphide greases or
other extreme pressure lubricants are used.
Torque Specifications for
37° JIC Fittings
Torque Specifications for
SAE O-Ring Fittings
Size
-4
140 ± 10
12 ± 1
2
2
7/16-20
-5
180 ± 15
15 ± 1
2
2
1/2-20
-6
250 ± 15
21 ± 1
1 1/2
1 1/4
9/16-18
-8
550 ± 25
45 ± 5
1 1/2
1
3/4-16
-12
1000 ± 50
85 ± 5
1 1/4
1
1 1/16-12
-16
1450 ± 50
120 ± 5
1
1
1 5/16-12
-20
2000 ± 100
170 ± 10
1
1
1 5/8-12
-24
2400 ± 150
200 ± 15
1
1
1 7/8-12
-32
3200 ± 200
270 ± 20
1
1
2 1/2-12
in.·lb.
Assembly Torque
ft.·lb.
Tube
Connection
F.F.F.T
Thread
Size
Swivel Nut
or Hose
Connection
F.F.F.T
Assembly Torque
Size
2
5/16-24
90 ± 5
7.5 ± 0.5
1 ± .25
3
3/8-24
170 ± 10
14 ± 1
1 ± .25
4
7/16-20
220 ± 15
18 ± 1
1 ± .25
5
1/2-20
260 ± 15
22 ± 1
1 ± .25
6
9/16-18
320 ± 20
27 ± 2
1.5 ± .25
8
3/4-16
570 ± 25
48 ± 2
1.5 ± .25
10
7/8-14
1060 ± 50
90 ± 5
1.5 ± .25
12
1 1/16-12
1300 ± 50
110 ± 5
1.5 ± .25
14
1 3/16-12
1750 ± 75
145 ± 6
1.5 ± .25
16
1 5/16-12 1920 ± 125
160 ± 6
1.5 ± .25
20
1 5/8-12
2700 ± 150
225 ± 12
1.5 ± .25
24
1 7/8-12
3000 ± 150
250 ± 12
1.5 ± .25
32
2 1/2-12
3900 ± 200
325 ± 15
1.5 ± .25
F.F.F.T.
in.·lb.
ft.·lb.
Swivel Nut
or Hose
O-Ring Face Seal Hose/
Tube Swivel Nut
Swivel Nut
Torque
Swivel
Nut Hex
Size
(in.)
Thread
Size
(in.)
Dash
Size
-3
-4
-5
-6
-8
-10
-12
-14
-16
-20
-24
-32
5
6
8
10
12
16
20
22
25
32
38
50.8
--
9/16 - 18
--
11/16 - 16
13/16 - 16
1 - 14
1-3/16 - 12
1-3/16 - 12
1-7/16 - 12
1-11/16 - 12
2 - 12
--
--
11/16
--
13/16
15/16
1-1/8
1-3/8
--
1-5/8
1-7/8
2-1/4
--
--
16
--
24
50
69
102
102
142
190
217
--
--
N·m lb
f
·ft
12
--
18
37
51
75
75
105
140
160
--
Metric
Tube
O.D.
(mm)
Summary of Contents for RHINO 7214 MSL
Page 4: ...2004 Alamo Group Inc SAFETY SECTION Safety Section 1 1...
Page 16: ...2004 Alamo Group Inc INTRODUCTION SECTION Introduction Section 2 1...
Page 19: ...2004 Alamo Group Inc ASSEMBLY SECTION Assembly Section 3 1...
Page 23: ...2004 Alamo Group Inc OPERATION SECTION Operation Section 4 1...
Page 34: ...2004 Alamo Group Inc MAINTENANCE SECTION Maintenance Section 5 1...
Page 44: ...7214 MSL SOM 12 04 Printed In U S A P N F 3778...