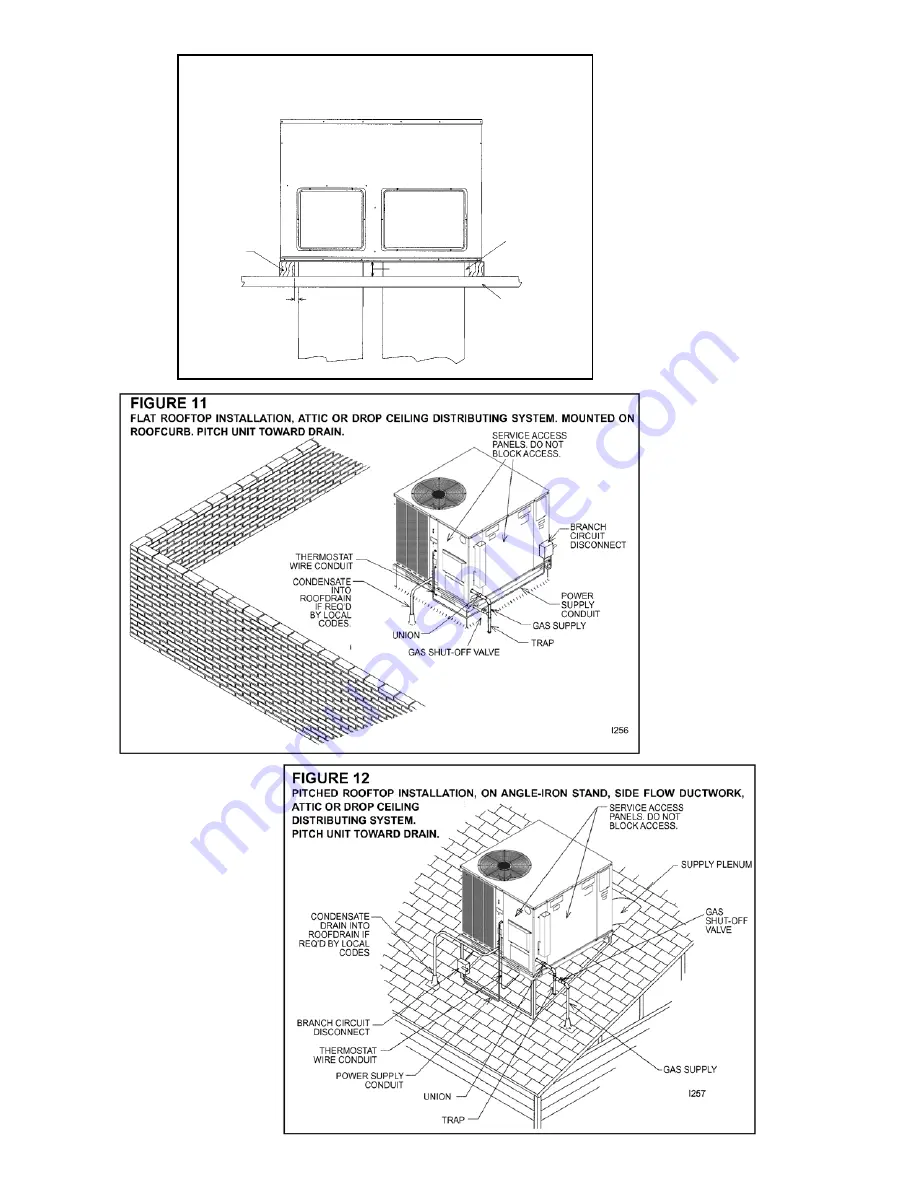
12
FIGURE
10
EXCEPTION TO NON-COMBUSTIBLE FLOORING REQUIREMENT
I458
BOTH ENDS
MUST BE
OPEN FOR
DOWNFLOW
OR SIDEFLOW
DUCTWORK
TO PROVIDE
VENTILATION
COMBUSTIBLE
STRUCTURE
1” MIN.
NOMINAL
4 x 4 TIMBER
(SIDES ONLY)
SIDEFLOW
SUPPLY
PLENUM
CONNECTION
SUPPLY
PLENUM
(DOWNFLOW)
RETURN PLENUM
(DOWNFLOW)
SIDEFLOW
RETURN PLENUM
CONNECTION
3-1/2” MIN.
Summary of Contents for RRNA-B SERIES
Page 46: ...46 FIGURE 24 WIRING DIAGRAM...
Page 47: ...47 FIGURE 25 WIRING DIAGRAM...
Page 48: ...48 FIGURE 26 WIRING DIAGRAM...
Page 49: ...49 FIGURE 27 WIRING DIAGRAM...
Page 50: ...50 FIGURE 28 WIRING DIAGRAM...
Page 51: ...51 FIGURE 29 SYSTEM CHARGE CHARTS 2 TON COOLING 13 SEER...
Page 52: ...52 FIGURE 30 SYSTEM CHARGE CHARTS 2 5 TON COOLING 13 SEER...
Page 53: ...53 FIGURE 31 SYSTEM CHARGE CHARTS 3 TON COOLING 13 SEER...
Page 54: ...54 FIGURE 32 SYSTEM CHARGE CHARTS 3 5 TON COOLING 13 SEER...
Page 55: ...55 FIGURE 33 SYSTEM CHARGE CHARTS 4 TON COOLING 13 SEER...
Page 56: ...56 FIGURE 34 SYSTEM CHARGE CHARTS 5 TON COOLING 13 SEER...
Page 58: ...58 FIGURE 36 15 SECOND PREPURGE...
Page 59: ...59...
Page 60: ...60 CM 1005...