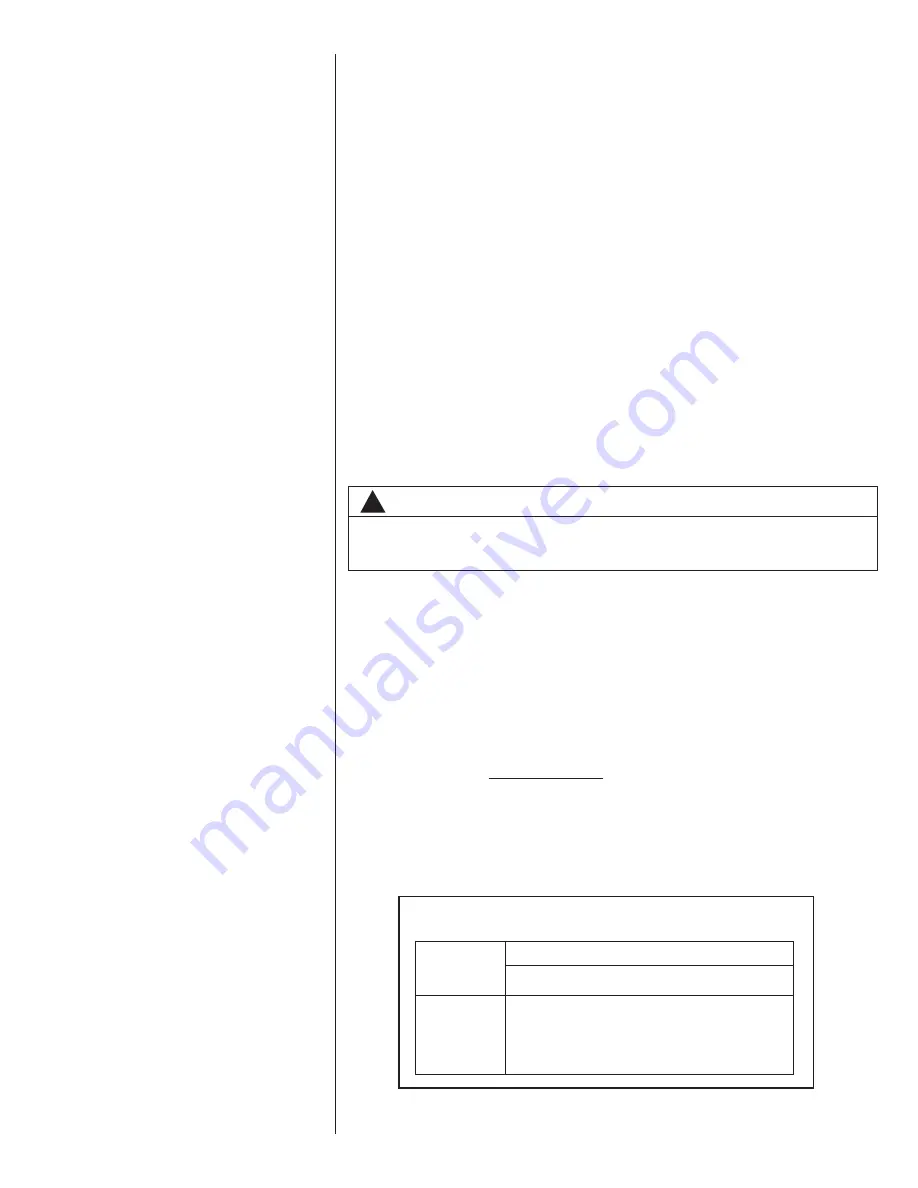
27
2. Connect the gas line to the gas valve supplied with unit. Routing can be through the
gas pipe opening shown in Figures 7 or 10 or through the base as shown in Figure
17.
3. Size the gas line to the furnace adequate enough to prevent undue pressure drop
and never less than 1/2”.
4. Install a drip leg or sediment trap in the gas supply line as close to the unit as possi-
ble.
5. Install an outside ground joint union to connect the gas supply to the control assem-
bly at the burner tray.
6. Gas valves have been factory installed. Install a manual gas valve where local codes
specify a shut-off valve outside the unit casing. (See Figure 14.)
7. Make sure piping is tight.
A pipe compound resistant to the action of liquefied
petroleum gases must be used at all threaded pipe connections.
8. IMPORTANT: any additions, changes or conversions required for the furnace to sat-
isfactorily meet the application should be made by a qualified installer, service
agency or the gas supplier, using factory-specified or approved parts. In the com-
monwealth of Massachusetts, installation must be performed by a licensed plumber
or gas fitter for appropriate fuel.
IMPORTANT:
Disconnect the furnace and its individual shutoff valve from the gas sup-
ply piping during any pressure testing of that system at test pressures in excess of 1/2
pound per square inch gauge or isolate the system from the gas supply piping system by
closing its individual manual shutoff valve during any pressure testing of this gas supply
system at pressures equal to or less than 1/2 PSIG.
TO CHECK FOR GAS LEAKS, USE A SOAP AND WATER SOLUTION OR OTHER
APPROVED METHOD. DO NOT USE AN OPEN FLAME.
IMPORTANT:
Check the rating plate to make certain the appliance is equipped to burn
the type of gas supplied. Care should be taken after installation of this equipment that
the gas control valve not be subjected to high gas supply line pressure.
In making gas connections, avoid strains as they may cause noise and damage the con-
trols. A backup wrench is required to be used on the valve to avoid damage.
The capacities of gas pipe of different diameters and lengths in cu. ft. per hr. with pres-
sure drop of 0.3 in. and specific gravity of 0.60 (natural gas) are shown in Table 1.
After determining the pipe length, select the pipe size which will provide the minimum
cubic feet per hour required for the gas input rating of the furnace. By formula:
Gas Input of Furnace
(BTU/HR)
Cu. Ft. Per Hr. Required =
Heating Value of Gas
(BTU/FT
3
)
The gas input of the furnace is marked on the furnace rating plate. The heating value of
the gas (BTU/FT
3
) may be determined by consulting the local natural gas utility or the
L.P. gas supplier.
!
WARNING
DO NOT USE AN OPEN FLAME TO CHECK FOR LEAKS. THE USE OF AN
OPEN FLAME CAN RESULT IN FIRE, EXPLOSION, PROPERTY DAMAGE, PER-
SONAL INJURY OR DEATH.
Nominal
Iron Pipe
Size,
Inches
Equivalent Length of Pipe, Feet
10
20
30
40
50
60
70
80
1
/
2
132
92
73
63
56
50
46
43
3
/
4
278
190
152
130
115
105
96
90
1
520
350
285
245
215
195
180
170
1
1
/
4
1,050
730
590
500
440
400
370
350
1
1
/
2
1,600 1,100
890
760
670
610
560
530
TABLE 1
GAS PIPE CAPACITY TABLE (CU. FT./HR.)
Summary of Contents for RKKL Series
Page 9: ...9 Illustration ST A0801 17 I FIGURE 6 ROOFCURB INSTALLATION FIGURE 5 ST A1154 02 00...
Page 41: ...41 TABLE 9 AIR FLOW PERFORMANCE 12 5 TON 43 9 kW RKKL B120 MODELS...
Page 45: ...45 FIGURE 21...
Page 46: ...46 FIGURE 22...
Page 47: ...47 FIGURE 23...
Page 48: ...48 FIGURE 24...
Page 49: ...49 FIGURE 25...
Page 50: ...50 FIGURE 26...
Page 51: ...51 FIGURE 27 RKKL SYSTEM CHARGE CHART...
Page 54: ...54...
Page 55: ...55...
Page 56: ...56 CM 1110...