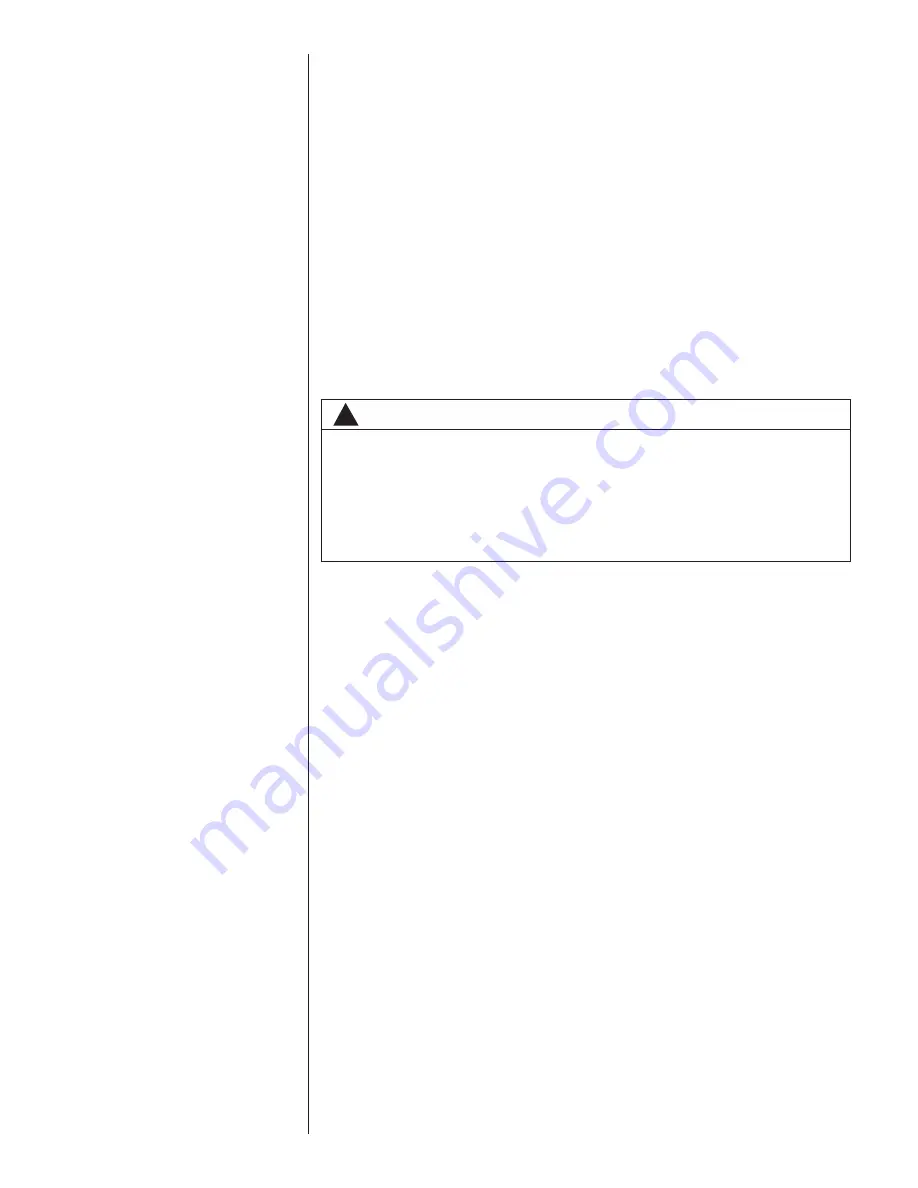
12
TO REASSEMBLE:
To attach coil casing to blower unit, make sure 3/4” flanges on back and sides of
return air opening of blower casing are bent along perforated edge to inside of casing.
Clearance holes in flange should match up with drive holes on inside of blower cas-
ing. Make sure 3/4” flanges on coil casing are bent up (back and 2 sides only) on sup-
ply air side of coil casing along perforated edge. Do not bend flange on front of coil
casing. Set supply air side of coil casing (3/4” flanges) into return air opening of blow-
er casing. Replace 6 - #8 screws through flange in coil casing, flange in blower casing
and into drive holes on inside of blower casing, two screws in back and two screws in
each side. Do not overtighten sheet metal screws, they will strip easily if overtight-
ened.
IMPORTANT: Configure the unit with the indoor coil casing installed on air inlet
(return) side of the blower section. Do not try to configure unit with indoor coil on
discharge (supply) side of blower section.
2.7 VERTICAL UPFLOW
• Electrical connections can be made from either the left or right side of the unit.
Refrigerant and condensate drain connections are made on the front of the unit (see
Figures 3 & 4).
• If return air is to be ducted, install duct flush with floor. Use fireproof resilient gasket 1/8
to 1/4 in. thick between duct, unit and floor. Set unit on floor over opening.
2.8 VERTICAL DOWNFLOW
Conversion to Vertical Downflow: A vertical upflow unit may be converted to vertical
downflow. (See Figure 3)
• Remove the indoor coil.
• Install coil rails in the top of the coil box (supplied).
• Rotate unit into the downflow position, with the coil compartment on top and the blower com-
partment on bottom.
• Reinstall the indoor coil in its new position.
• Rotate the circuit breaker(s) 180° (see instructions for rotating breaker(s) that follow).
IMPORTANT NOTE:
• In a downflow configuration the internal air filter must not be used.
• A remote air filter should be installed in the return air system
• The remote air filter should be sized for a maximum of 300 feet per minute of air veloci-
ty for the CFM required.
!
WARNING
IF UNIT IS TO BE INSTALLED WITHOUT AN INDOOR COIL, RETURN DUCT OR
PLENUM, IT MUST NOT BE IN STALLED DIRECTLY OVER COMBUSTIBLE MATE-
RIAL. IF INSTALLED WITHOUT AN INDOOR COIL WITH A RETURN DUCT OR
PLENUM, THE AIR PLENUM OR DUCT MUST HAVE A SOLID SHEET METAL
BOTTOM WITH NO RETURN AIR OPENINGS, REGISTERS OR FLEXIBLE AIR
DUCTS LOCATED DIRECTLY UNDER THE UNIT. EXPOSING COMBUSTIBLE
MATERIAL TO THE RETURN OPENING OF AN UPFLOW UNIT WITHOUT AN
INDOOR COIL CAN CAUSE A FIRE RESULTING IN PROPERTY DAMAGE, PER-
SONAL INJURY OR DEATH.