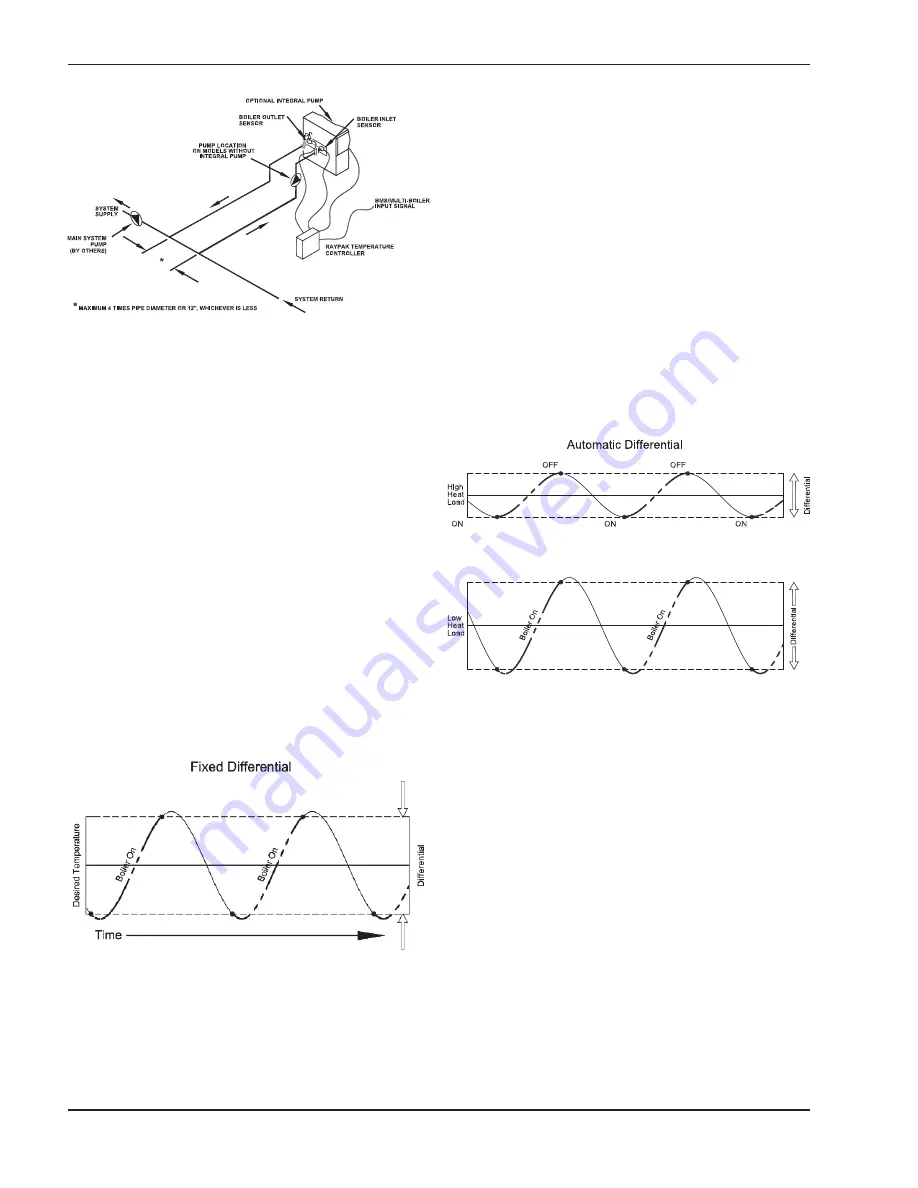
8
Proportional, Integral & derivative
(PId)
After the heater is turned on in the firing sequence, the
Controller waits a minimum amount of time before
modulating. The control error is determined using PID
logic.
Proportional
compares the actual operating sensor
temperature to the heater target temperature. The
colder the temperature, the sooner the heater modu-
lates up.
Auto differential
If Auto Differential is selected, the control automatical-
ly determines the best differential as the load changes,
thereby improving efficiency. During light loads, the dif-
ferential is increased to allow longer on and off times
to reduce the potential for short-cycling. During large
loads, the differential is narrowed thereby improving
comfort in heating spaces by reducing temperature
swing.
Tank differential
Tank Differential is subtractive to the set point. For
example, in the case of a 130
°F
set point with a 3
°F
differential, the control will energize the heater when
the tank temperature drops to 127
°F
and then will shut
the heater off at 130
°F
.
Fig. 16: Auto Differential
Code descriptions
Heater differential (dIFF)
A heat source must be operated with a differential in
order to prevent short cycling. The heater differential is
divided around the heater target temperature. The
stage contact will close when the water temperature at
the operating sensor is 1/2 of the differential setting
below the heater target temperature, and will open
when the water temperature at the operating sensor is
1/2 of the differential setting above the heater target
temperature.
Manual differential
The differential can be manually set using the DIFF
setting in the Adjust menu.
Fig. 15: Fixed Differential
Fig. 14: External Direct Drive Operation (Mode 8)