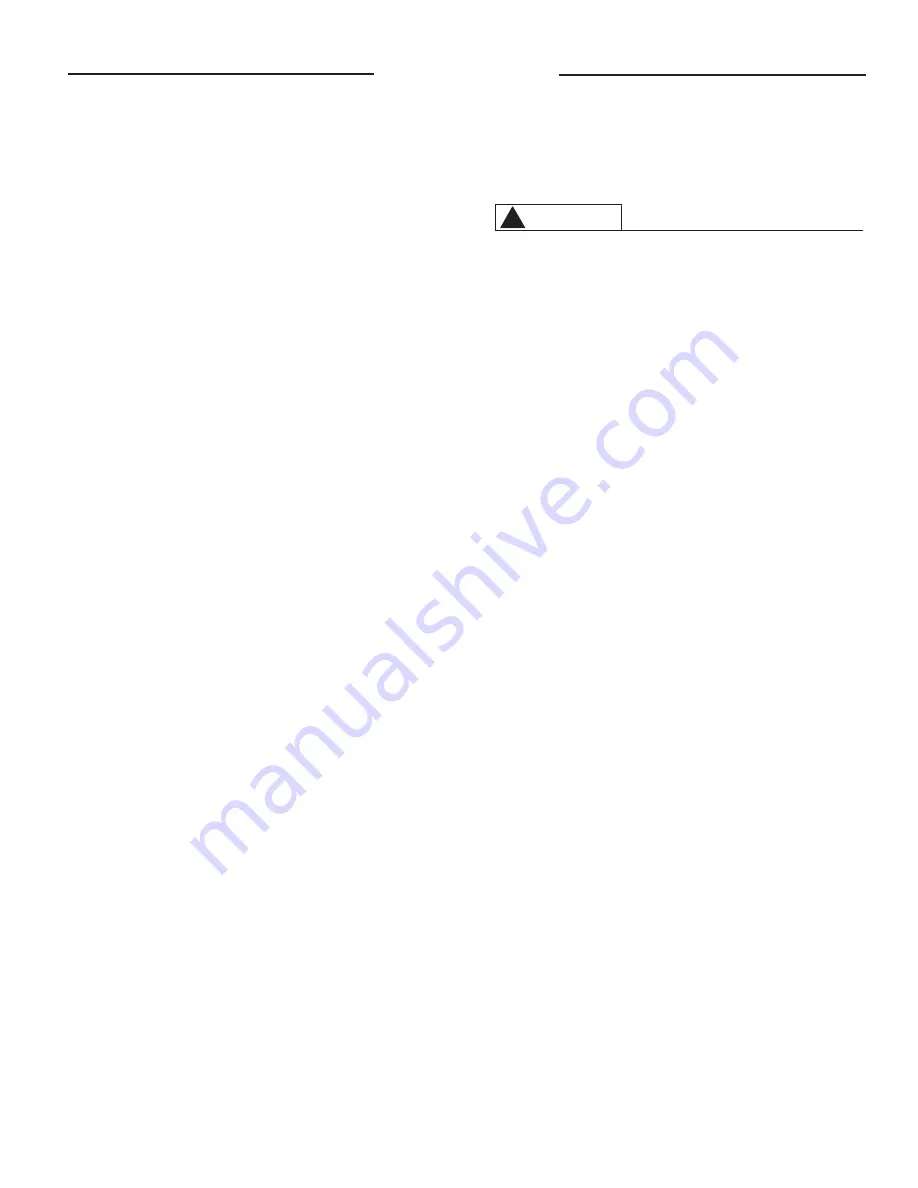
7
the resulting rapid, and repeated expansion and
contraction of components in the water heater and
piping system can cause premature failure of the
relief valve, and possibly the heater itself. Replac-
ing the relief valve will not correct the problem!
The suggested method of controlling thermal ex-
pansion is to install an expansion tank in the cold
water line between the water heater and the check
valve. The expansion tank is designed with an air
cushion built in that compresses as the system
pressure increases, thereby relieving the over pres-
sure condition and eliminating the repeated opera-
tion of the relief valve. Other methods of controlling
thermal expansion are also available. Contact your
installing contractor, water supplier, or plumbing
inspector for additional information regarding this
subject.
If a recirculation line is installed, the return con-
nection should be made to a tee close to the inlet
connection on the water heater. A check valve
should always be installed in the recirculation line
to prevent cold water from entering.
3.
WATER CONNECTIONS
— This water heater may
be connected individually, in multiples with others,
or with an external hot water storage tank.
Inlet water connections are made to the lower
coupling on the heater, and outlet water connec-
tions are made to the upper coupling.
Each water heater is supplied with the necessary
components (Diffuser tubes) to make the water
connections that will ensure proper performance.
The components are supplied in a bag attached
to the water heater. If special instructions are re-
quired for any specific water heater, they will be
included in the bag.
Cap or plug unused connections. Use only clean,
new galvanized steel, copper or approved plastic
pipe for water connections. Local codes or regula-
tions shall govern the exact type of material to be
used. The installation of unions on the inlet and
outlet water lines and a shut-off valve in at least
the cold water inlet line is recommended, so the
water heater may be easily disconnected for ser-
vicing. Dielectric unions are not required for pro-
tection of water heater.
When this water heater is supplying general pur-
pose hot water requirements for use by individu-
als, a thermostatically controlled mixing valve is
recommended to reduce the risk of scald injury.
Contact a licensed plumber or the local plumbing
authority for further information.
Thermometer(s) should be installed so that they
indicate the temperature of the water at or near
the outlet of the water heater and storage tank(s) if
provided.
4. RELIEF VALVE
— A new factory installed com-
bination pressure and temperature relief valve,
complying with the Standard for Relief Valves and
Automatic Gas Shutoff Devices for Hot Water Sup-
ply Systems, ANSI Z21.22, or Standard CSA 4.4,
Temperature, Pressure, Temperature and Pressure
Relief Valves and Vacuum Relief Valves, is provid-
ed with the water heater. No valve is to be placed
between the relief valve and the water heater. For
a circulating tank installation, the separate storage
tank(s) must have similar protection. The pres-
sure rating of the relief valve
MUST NOT EXCEED
150 psi (1034 kPa) (160 psi for ASME models), the
maximum working pressure as marked on front of
the water heater.
WARNING
!
Connect the outlet of the relief valve to a suitable open drain.
The discharge line must pitch downward from the valve to
allow complete draining (by gravity) of the relief valve and
discharge line, and be no smaller than the outlet of the valve.
The end of the discharge line should not be threaded or con-
cealed and should be protected from freezing. No valve of
any type, restriction or reducer coupling should be installed
in the discharge line. Local codes shall govern the installation
of relief valves.
The Btu/h rating of the relief valve must equal or exceed the
Btu/h input of the water heater as marked on its rating plate.
5. GAS SUPPLY —
Prior to installation, contact your local
gas utility to confirm that sufficient gas service is available
for the water heater. The gas meter must have adequate
capacity to supply the rated maximum gas input of the
water heater in addition to other gas fired equipment con-
nected to the meter.
Minimum Gas Supply Pressure:
The gas supply must be capable of maintaining a
minimum pressure at the inlet of the gas control
during water heater operation at maximum input.
The pressure will be lowest at the gas control dur-
ing water heater operation (i.e. gas is flowing) at
maximum input. For natural gas models, during
operation at maximum input, the supply pressure
at the gas control must be at least 6" W.C. For LP
gas models, during operation at maximum input,
the supply pressure at the gas control must be at
least 8" W.C.
Refer to table 3 for gas supply line sizing. The table shows
maximum input in thousands of BTU's per hour for various
pipe sizes and lengths. The table assumes gas supply pres-
sures of 14" W.C. or less and a pressure drop of 0.3" w.c.
Maximum Gas Supply Pressure
The gas supply pressure shall never be greater
than 14" W.C. Pressures greater than 14" W.C. may
damage the gas control which could cause a fire
or explosion.
A ground joint union and manual shutoff valve
should be installed in the gas line near the water
heater so that the burner assembly may be easily
removed. The shut-off valve must be readily ac-
cessible for turning on or off. See Figure 6.
Where a sediment trap is not incorporated as
part of the appliance, a sediment trap shall be in-
stalled downstream of the equipment shutoff valve
as close to the inlet of the appliance as practi-
cal at the time of the appliance installation. The
sediment trap shall be either a tee fitting with a
capped nipple in the bottom outlet or other device
recognized as an effective sediment trap. See Fig-
ure 6.
Introduction
Summary of Contents for GHE 125-500A
Page 20: ...20 Installation Schematic Diagram Figure 18...
Page 25: ...25 Operation Steps to adjust the setpoint temperature Figure 21...
Page 37: ...37 Notes...
Page 38: ...38 Notes...
Page 39: ...39 Notes...