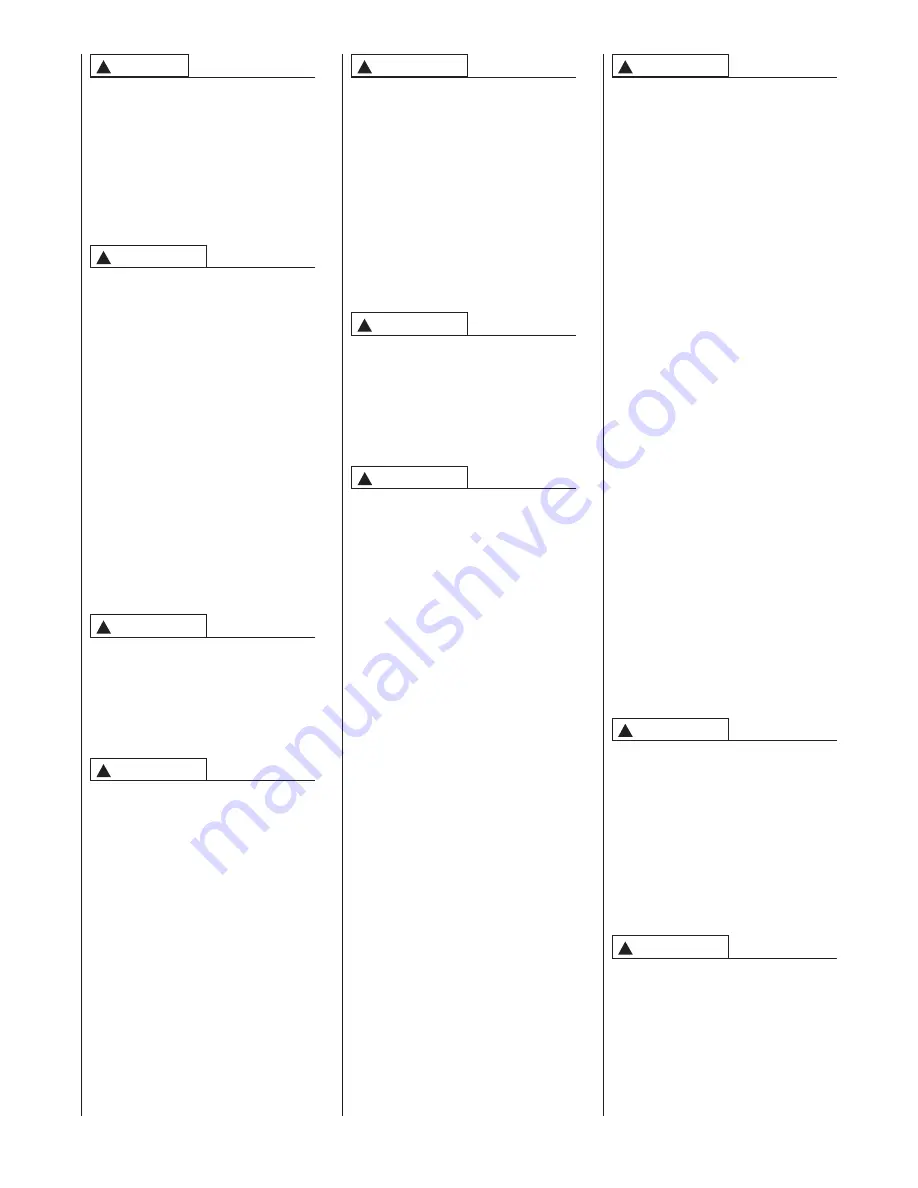
6
DO NOT USE THIS FURNACE
DURING CONSTRUCTION IF AIR
LADEN CORROSIVE COMPOUNDS
ARE PRESENT SUCH AS
CHLORINE AND FLUORINE.
OTHERWISE, PROVISIONS MUST
BE TAKEN TO PROVIDE CLEAN,
UNCONTAMINATED COMBUSTION
AND VENTILATION AIR TO THE
FURNACE. FURNACE
COMBUSTION AND VENTILATION
AIR CONTAMINATED WITH THESE
COMPOUNDS FORMS ACIDS
DURING COMBUSTION WHICH
CORRODES THE HEAT
EXCHANGER AND COMPONENT
PARTS. SOME OF THESE
CONTAMINANTS ARE FOUND IN,
BUT NOT LIMITED TO, PANELING,
DRY WALL, ADHESIVES, PAINTS,
STAINS, VARNISHES, SEALERS,
AND MASONRY CLEANING
MATERIALS.
If this furnace is installed in a
garage, attic and/or any
unconditioned space, install a self-
regulating heat tape around the
condensate trap and along the
entire length of the condensate
drain in the unconditioned space.
See Figure 4.
WHEN THIS FURNACE IS
INSTALLED IN A RESIDENTIAL
GARAGE, IT MUST BE INSTALLED
SO THE BURNERS AND IGNITION
SOURCE ARE LOCATED NO LESS
THAN 18 INCHES ABOVE THE
FLOOR. THIS IS TO PREVENT
THE RISK OF IGNITING
FLAMMABLE VAPORS WHICH
MAY BE PRESENT IN A GARAGE.
ALSO, THE FURNACE MUST BE
LOCATED OR PROTECTED TO
AVOID PHYSICAL DAMAGE BY
VEHICLES. FAILURE TO FOLLOW
THESE WARNINGS CAN CAUSE A
FIRE OR EXPLOSION, RESULTING
IN PROPERTY DAMAGE,
PERSONAL INJURY OR DEATH.
!
WARNING
UPFLOW AND HORIZONTAL
FURNACES ARE DESIGN-
CERTIFIED FOR INSTALLATION
ON COMBUSTIBLE FLOORS.
NOTE, HOWEVER, THAT
FURNACES MUST NOT BE
INSTALLED DIRECTLY ON
CARPETING, TILE OR OTHER
COMBUSTIBLE MATERIAL OTHER
THAN WOOD FLOORING.
INSTALLATION ON A
COMBUSTIBLE MATERIAL CAN
RESULT IN FIRE, CAUSING
PROPERTY DAMAGE, PERSONAL
INJURY OR DEATH.
!
WARNING
!
CAUTION
!
WARNING
IMPROPER INSTALLATION, OR
INSTALLATION NOT MADE IN
ACCORDANCE WITH THE CSA
INTERNATIONAL (CSA)
CERTIFICATION OR THESE
INSTRUCTIONS, CAN RESULT IN
UNSATISFACTORY OPERATION
AND/OR DANGEROUS CONDI-
TIONS AND ARE NOT COVERED
BY THE UNIT WARRANTY.
!
NOTICE
!
WARNING
DO NOT INSTALL THIS FURNACE
IN A MOBILE HOME!!
This furnace
is not approved for installation in a
mobile home. Doing so could cause
FIRE, PROPERTY DAMAGE,
PERSONAL INJURY OR DEATH.
!
WARNING
DO NOT LIFT THE UNIT BY THE
HEAT EXCHANGER TUBES.
DOING SO CAN CRACK THE HEAT
EXCHANGER ASSEMBLY AND
CAUSE CO2 TO BE RELEASED
INTO THE ENVIRONMENT, WHICH
CAN RESULT IN PERSONAL
INJURY OR DEATH.
UPFLOW FURNACE:
A SOLID
METAL BASE PLATE MUST BE
INSTALLED IN THE FURNACE
BOTTOM WHEN USING SIDE
RETURN. FAILURE TO INSTALL A
BASE PLATE COULD CAUSE THE
PRODUCTS OF COMBUSTION TO
CIRCULATE INTO THE LIVING
SPACE AND CREATE POTENTIAL -
LY HAZARDOUS CONDITIONS,
INCLUDING CARBON MONOXIDE
POISONING OR DEATH.
!
WARNING
!
WARNING
!
WARNING
NEVER ALLOW THE PRODUCTS
OF COMBUSTION FROM THE
FLUE TO ENTER THE RETURN AIR
DUCTWORK OR THE CIRCULATED
AIR SUPPLY. ALL RETURN
DUCTWORK MUST BE
ADEQUATELY SEALED AND
SECURED TO THE FURNACE
WITH SHEET METAL SCREWS;
AND JOINTS, TAPED. ALL OTHER
DUCT JOINTS MUST BE SECURED
WITH APPROVED CONNECTIONS
AND SEALED AIRTIGHT. WHEN
AN UPFLOW FURNACE IS
MOUNTED ON A PLATFORM WITH
RETURN THROUGH THE BOTTOM,
IT MUST BE SEALED AIRTIGHT
BETWEEN THE FURNACE AND
THE RETURN AIR PLENUM. THE
FLOOR OR PLATFORM MUST
PROVIDE SOUND PHYSICAL
SUPPORT OF THE FURNACE
WITHOUT SAGGING, CRACKS, OR
GAPS, AROUND THE BASE,
PROVIDING A SEAL BETWEEN
THE SUPPORT AND THE BASE.
FAILURE TO PREVENT
PRODUCTS OF COMBUSTION
FROM BEING CIRCULATED INTO
THE LIVING SPACE CAN CREATE
POTENTIALLY HAZARDOUS
CONDITIONS, INCLUDING
CARBON MONOXIDE POISONING
THAT COULD RESULT IN
PERSONAL INJURY OR DEATH.
DO NOT, UNDER ANY
CIRCUMSTANCES, CONNECT
RETURN OR SUPPLY DUCTWORK
TO OR FROM ANY OTHER HEAT
PRODUCING DEVICE SUCH AS A
FIREPLACE INSERT, STOVE, ETC.
DOING SO MAY RESULT IN FIRE,
CARBON MONOXIDE POISONING,
EXPLOSION, PERSONAL INJURY
OR PROPERTY DAMAGE.
COMBUSTIBLE MATERIAL MUST
NOT BE PLACED ON OR AGAINST
THE FURNACE JACKET. THE AREA
AROUND THE FURNACE MUST BE
KEPT CLEAR AND FREE OF ALL
COMBUSTIBLE MATERIALS
INCLUDING GASOLINE AND
OTHER FLAMMABLE VAPORS AND
LIQUIDS. PLACEMENT OF
COMBUSTIBLE MATERIALS ON,
AGAINST OR AROUND THE
FURNACE JACKET CAN CAUSE
AN EXPLOSION OR FIRE
RESULTING IN PROPERTY
DAMAGE, PERSONAL INJURY OR
DEATH. THE HOMEOWNER
SHOULD BE CAUTIONED THAT
THE FURNACE AREA MUST NOT
BE USED AS A BROOM CLOSET
OR FOR ANY OTHER STORAGE
PURPOSES.
Summary of Contents for GF901D Series
Page 60: ...60 FIGURE 52 MODELS WITH UT ELECTRONIC CONTROLS 1097 200 ...
Page 61: ...61 FIGURE 53 MODELS WITH UT ELECTRONIC CONTROLS 1097 200 ...
Page 62: ...62 ...
Page 63: ...63 ...
Page 64: ...64 CM 0611 ...