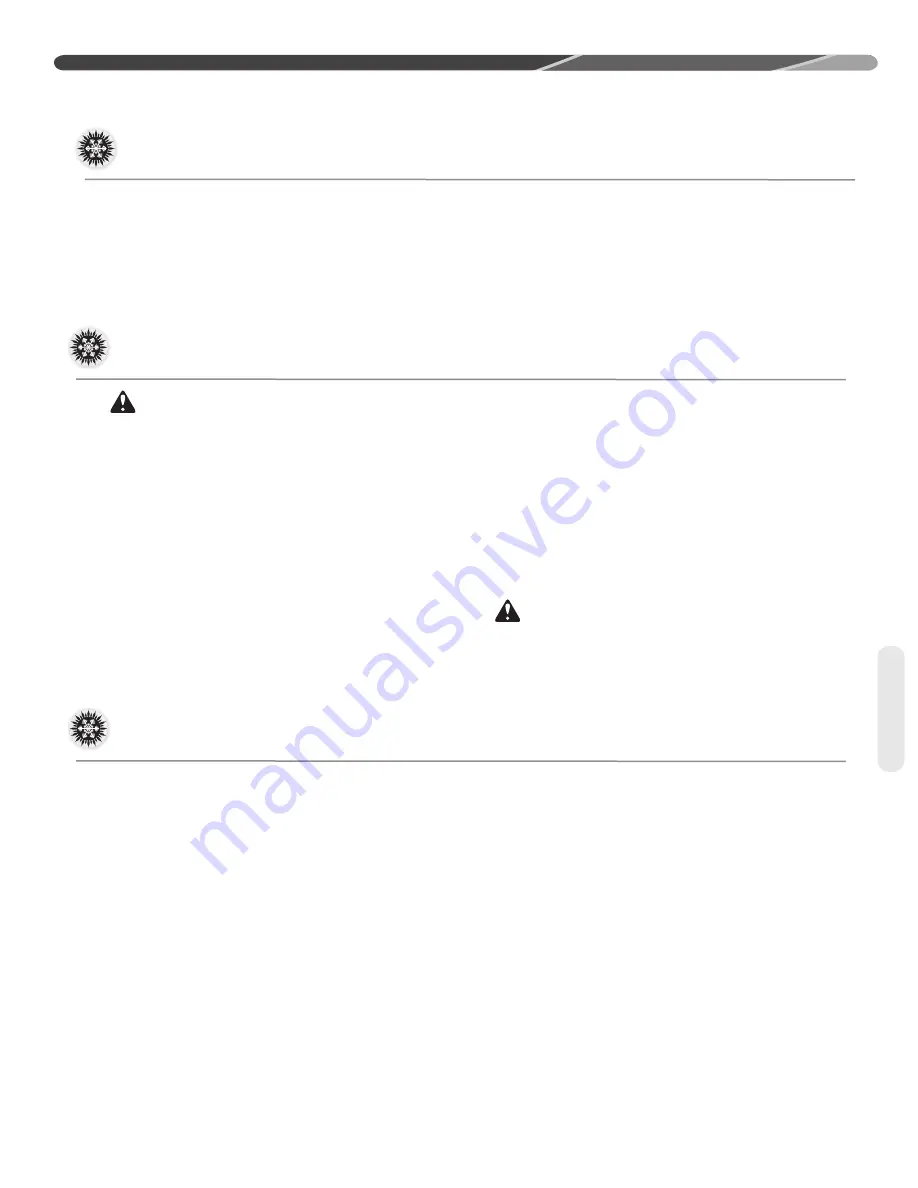
11
INSTALLATION
Replacement Units
To prevent failure of a new unit, the existing line set
must be correctly sized and cleaned or replaced�
Care must be exercised that the expansion device
is not plugged� For new and replacement units, a
liquid line filter drier must be installed and refrigerant
tubing must be properly sized� Test the oil for acid� If
positive, a suction line filter drier is mandatory�
IMPORTANT:
When replacing an
R-22 unit with an R-410A unit, either replace
the line set or ensure that residual mineral oil is
drained from existing lines, including oil trapped in
low spots�
Indoor Coil
CAUTION:
Only use evaporators
approved for use on R-410A systems that are
specifically matched with the outdoor unit per
the manufacturer’s specification sheets� Use
of existing R-22 evaporators can introduce
mineral oil to the R-410A refrigerant, forming two
different liquids and decreasing oil return to the
compressor� This can result in compressor failure�
REFER TO INDOOR COIL MANUFACTURER’S
INSTALLATION INSTRUCTIONS.
IMPORTANT:
The manufacturer is not
responsible for the performance and operation of
a mismatched system or for a match listed with
another manufacturer’s coil�
The thermostatic expansion valve in the
matching coil is specifically designed to operate
with R-410A�
DO NOT use an R-22 TXV or
evaporator� The existing evaporator must
be replaced with the factory-specified TXV
evaporator specifically designed for R-410A�
Location
Do not install the indoor coil in the return duct
system of a gas or oil furnace� Provide a service
inlet to the coil for inspection and cleaning� Keep
the coil pitched toward the drain connection�
CAUTION:
When coil is installed
over a finished ceiling and/or living area, it is
required that a secondary condensate pan be
installed under entire unit� Failure to do so can
result in property damage�
Interconnecting Tubing
The purpose of this section is to specify the
best construction/sizing practices for installing
interconnection tubing between the indoor and
outdoor unit�
Refrigerant Level Adjustment
All units are factory-charged with R-410A
refrigerant to cover 15 feet of standard size
interconnecting liquid and vapor lines with a
required field installed filter drier. Adjustment of
charge may be necessary even if the application
has exactly 15 feet of line set due to other
installation variables such as pressure drop,
vertical lift, and indoor coil size. For different
lengths, adjust the charge as indicated below�
adjust the charge as indicated below�
• 1/4” ± .3 oz./foot [6.4 mm ± 8.5 g/.30 m]
• 5/16” ± .4 oz./foot [7.9 mm ± 11.3 g/.30 m]
• 3/8” ± .6 oz./foot [9.5 mm ± 17.0 g/.30 m]
• 1/2” ± 1.2 oz./foot [12.7 mm ± 34.0 g/.30 m]
• 6 oz. Required factory supplied field installed
•
filter dry
Charge Adjustment = (Line Set (oz. /ft.) x Total
Length) – Factory Charge for Line Set
Example:
A three ton condensing unit with factory
installed 3/8” liquid service valve
requires 75 ft of line set with a liquid line diameter
of 1/2”.
Factory Charge for Line Set
= 15ft x �6 oz� = 9 oz�
Charge Adjustment
= (1�2 oz� x 75 ft�) – 9 oz� =
+81 oz�
Tubing