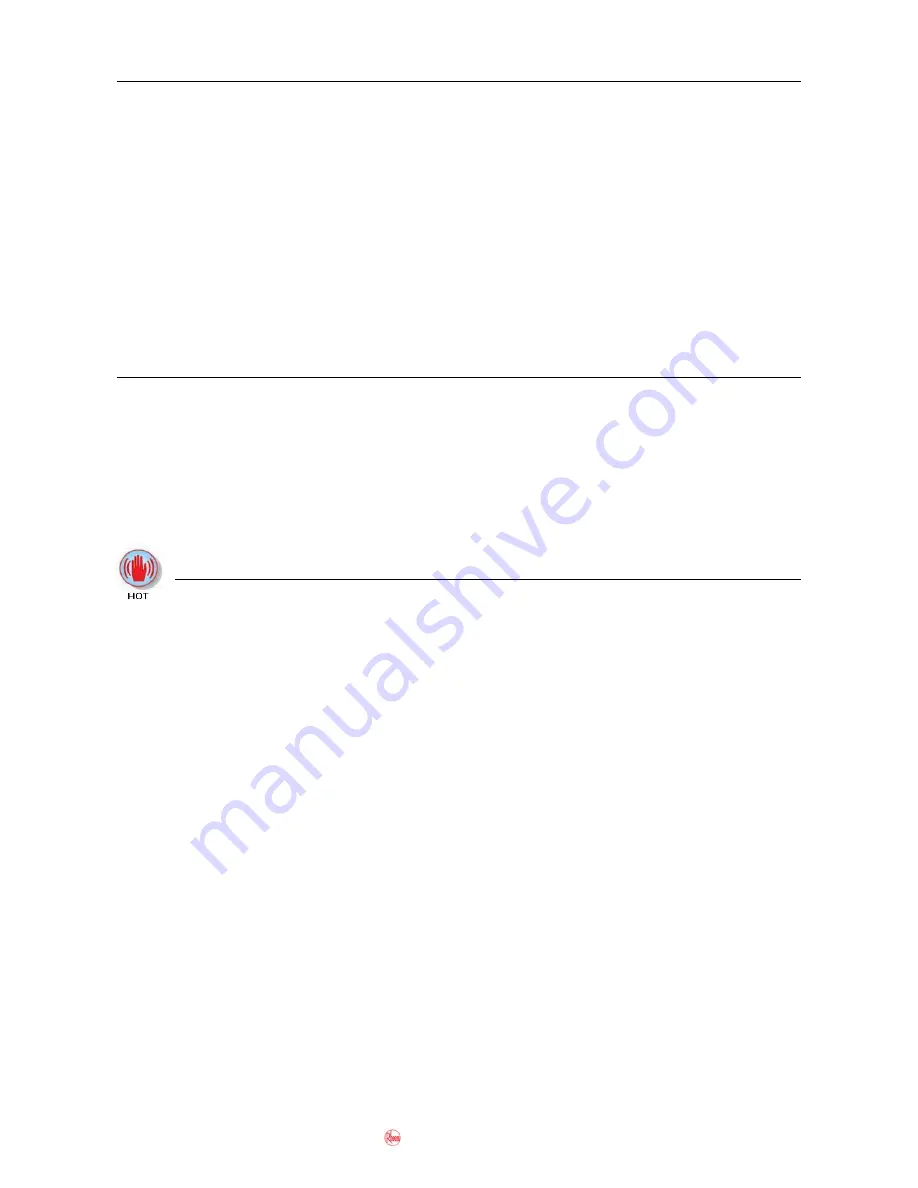
54
TM061 Rheem 27 Water Star Service Instructions
– Issued: 11/10
REV A Issued 08/13
This document is stored and maintained electronically by
Service. Al
l printed copies not bearing this statement in RED are deemed “uncontrolled”
Cold Water Inlet Thermistor: (Procedure 16)
1.
Isolate power and water supplies.
2. Unscrew the water drain plug and pressure relief valve and drain the water heater.
3. Remove the front cover, control PCB, power supply PCB and water bypass control
assembly. Refer to procedures 1, 2, 3 and 12.
4. Rotate the water volume control assembly to the left to expose the cold water inlet
thermistor.
5. Remove the thermistor retaining screw and withdraw the thermistor taking care not to
damage the o‟ring. Ensure o‟ring remains located within thermistor housing.
6. Disconnect the cold inlet thermistor lead from the white cable connector.
7. Reassemble in reverse order of above.
Ambient Air Thermistor: (Procedure 17)
1.
Isolate power supply.
2. Remove front cover, control PCB and power supply PCB. Refer to procedures 1, 2 and 3.
3. Locate the ambient air thermistor and remove retaining screw.
Thermistor is mounted on
bracket at right hand side of fan housing. Remove the thermistor from retaining bracket.
4. Disconnect the ambient thermistor lead from the blue cable connector.
5. Reassemble in reverse order of above.
Hot Water Outlet Thermistor: (Procedure 18)
1.
Isolate power and water supplies.
2. Relieve water pressure through a hot tap.
3. Remove front cover, control PCB and power supply PCB. Refer to procedures 1, 2 and 3.
4. Locate the hot water outlet thermistor at the hot water outlet connection on left hand side
of heater cabinet.
5. Remove the two thermistor retaining screws and withdraw the thermistor taking care not
to damage the o‟ring.
Note:
Water may escape during this procedure.
Ensure o‟ring
remains located within thermistor housing.
6. Disconnect the hot outlet thermistor lead from the black cable connector.
7. Reassemble in reverse order of above.