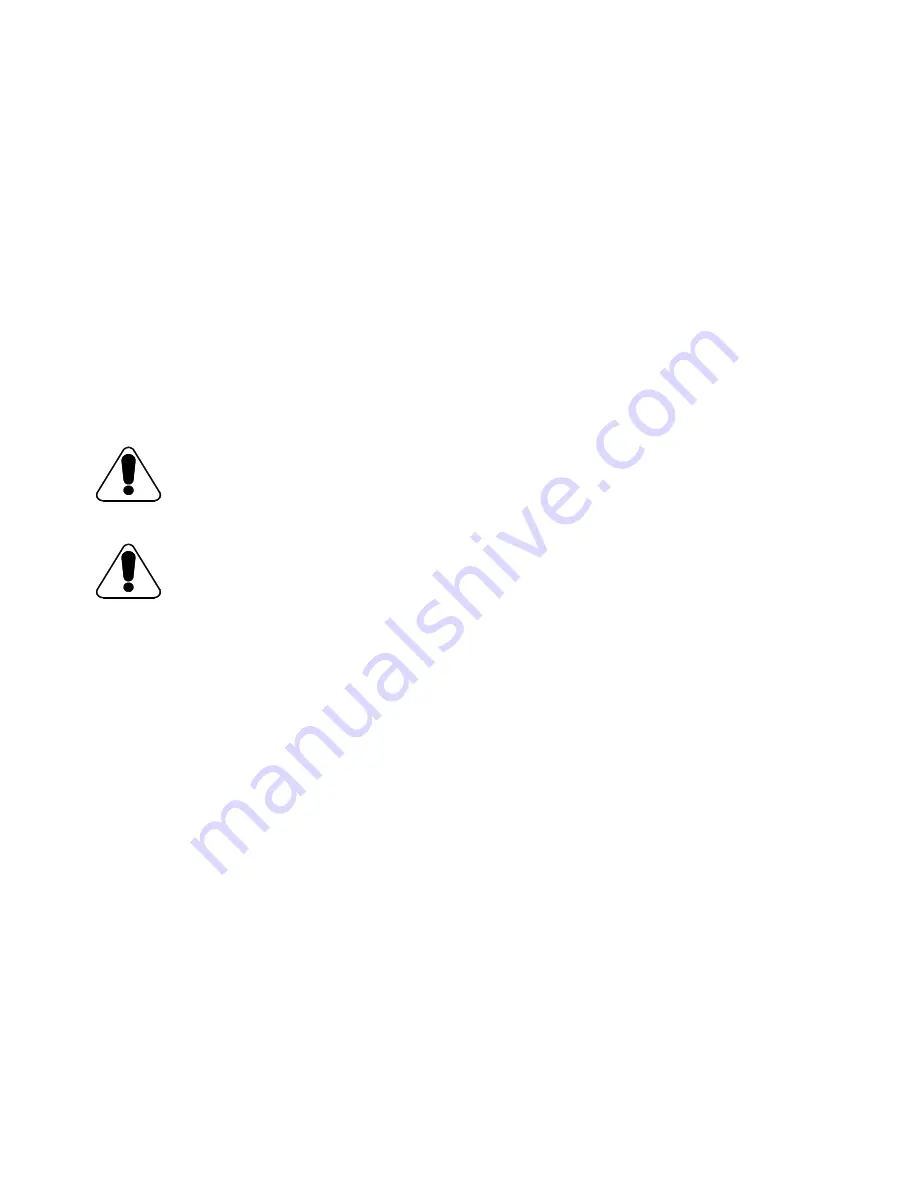
4
INSPECTION AND MAINTENANCE
4.1
GENERAL MAINTENANCE RULES
Hydraulic fluid can become contaminated after extended periods of use which can cause restrictions in the system. Check
to see that the fluid is clean, and change at recommended intervals to extend tool’s life. Refer to the respective manual for
maintenance information on the hydraulic power source.
1.
Proper maintenance of the Rock Drill and related equipment requires timely adhering to all the guidelines given in this
chapter. Proper maintenance is required to maintain the system in good condition and free of defects.
2.
Review and follow all the safety rules given in Chapter 1 before attempting any maintenance.
3.
Only authorized personnel should be allowed in the maintenance area. Authorized personnel are the trained people as
defined below and their supervision.
4.
Repairs must be made only by trained personnel. A trained person is one who has read and thoroughly understands this
instruction manual and related equipment manuals and, through training and experience, has shown knowledge
regarding the safe operational procedures.
CAUTION:
BEFORE STARTING ANY MAINTENANCE, DISCONNECT FROM HYDRAULIC POWER
SOURCE TO PREVENT ACCIDENTAL STARTUP.
WARNING:
DURING ANY MAINTENANCE OR REPAIR PROCEDURES, DO NOT ATTEMPT ANY
DRILLING. THIS CAN CAUSE SERIOUS PERSONAL INJURY AND/OR EQUIPMENT
DAMAGE.
4.2
DAILY MAINTENANCE
1.
Wipe couplings clean and connect hydraulic hoses to an unpowered (not activated) hydraulic source.
2.
Remove the tool steel. With a clean object, push the piston through the bushing to it’s inner most position. Remove
the object and using the grease nipple located in the nose assembly, lubricate the bushing with Molykote grease, like
Mobiletac 81 or similar. Failure to grease the nose assembly every 8 hours of operation will cause the drive system to
stop rotating.
3.
Clean off any accumulation of particles from beneath the trigger area. Spray with a light oil and wipe off excess.
4.
Disconnect hydraulic hoses and wipe couplings clean, especially before a connection is made. This is the single most
common point of entry for foreign particles which can cause premature wear of hydraulic components in the system.
5.
Check that all hardware on the Rock Drill is tight.
6.
Check the hoses before each use for damage. Replace a damaged hose immediately. Never repair the hose.
7.
Before each use
,
insure that all broken, worn or defective parts are repaired or replaced.
8.
Insure the tool steel is sharp to give maximum drilling power and operator comfort.
8