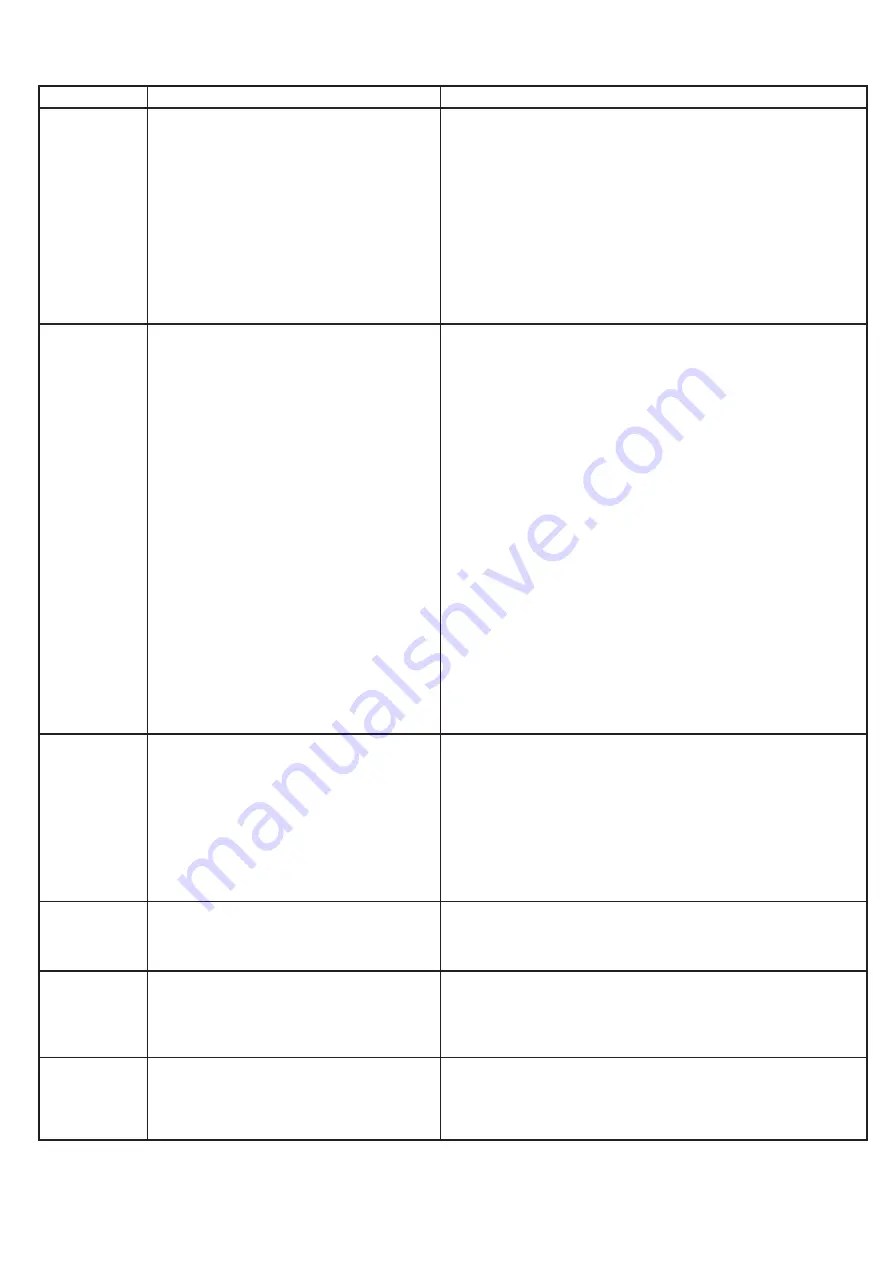
1801UDSBD-4E,--EN, Pag. 31/35
PROBLEM
PROBABLE CAUSE
REMEDY
Venter motor will
not start
1. No power to unit
2. No power to venter motor
3. Integrated burner relay defective.
4. Defective venter motor.
5. Fluse blown (F3.1).
6. Fuse burner relay blown.
7. LC1 open.
8. LC3 open.
9. Unit in lock-out.
10. Room thermostat open.
1. Turn on power, check supply fuses or circuit breaker.
2. Check connections at burner relay and/or venter motor terminals.
3. Replace burner relay.
4. Replace venter motor. See Section 26.
5. Replace fuse.
6. Replace fuse.
7. a) Set heater on ventilation until LC1 closes.
b) Replace LC1.
c) Check if there is obstruction at the fan side.
8. a) Reset LC3.
b) Replace LC3.
9. Push on reset button.
10. Set thermostat above room temperature.
Burner will
not light
1. Main valve not operating
2. Air in the gas line.
3. Gas pressure too high or too low.
4. No spark:
a) Loose wire connections.
b) Incorrect spark gap.
c) Spark cable has a short circuit to ground.
d) Spark electrode has a short circuit to ground.
e) Burner relay not grounded.
f) Unit not properly grounded.
g) Faulty burner relay.
5. Combustion airs pressure switch not closing
upon power to venter.
1. a) Check voltage on valve during ignition period.
b) Check connector on main gas valve.
c) Check connector on burner relay.
d) Replace valve.
2. Purge gas line.
3. a) Supply pressure should be 15 mbar for natural gas (UK only) or 37
mbar for propane gas (UK only).
b) Obstruction in the gas line.
c) Gas line connection diameter too small.
4. Check the following:
a) Be certain all wire connections are solid.
b) Maintain spark gap at 3 mm.
c) Replace worn or grounded spark cable.
d) Replace if ceramic spark electrode is cracked or grounded.
e) Check burner relay ground wire.
f) Make certain unit is properly field grounded (earthed) and properly
phased
(L1 to hot lead, L2 to neutral).
g) If voltage is available to the burner relay and all other causes have been
eliminated, replace burner relay.
5. First check the following:
a) Make sure unit is properly vented.
b) Remove obstructions from vent.
c) Replace faulty tubing to pressure switch.
d) Replace faulty pressure switch.
Burner cycle
on and off
1. Gas pressure too high or too low.
2. Burner relay not grounded.
3. Faulty burner relay.
4. Flame sensor grounded.
5. Cracked ceramic at sensor.
6. Incorrect polarity.
1. Supply pressure should be 15 mbar for natural gas (UK only) or 37 mbar
for propane gas (UK only).
2. Check burner relay ground wire connection.
3. If (220/240) volts is available to the burner relay and all other causes have
been eliminated, replace burner relay.
4. Be certain flame sensor lead is not grounded or insulation or ceramic is
not cracked. Replace as required.
5. Replace sensor.
6. Check polarity switch and if necessary reverse line voltage wires to termi-
nal block connections.
Blower will not
run
1. Circuit open.
2. Defectivetime delay relay for the fan (KFC).
3. Defective motor.
1. Check wiring and connections.
2. a) Replace the time delay relay.
b) Check voltage on anticipation resistor when gas valve is open.
3. Replace blower & motor.
Blower or venter
motor turns on
and off while
burner is operat-
ing
1. Motor internal thermal protection device cycling
on and off.
1. Check motor load against motor rating plate. Replace motor if needed.
Venter
motor turns off in
case of thermal
overload
1. Electrical current too high or too low
2. Motor defect
3. Air flow insufficient
4. Faulty bearing
1. Correct
2. Replace motor
3. Clean motor, venter & filter
4. Oil bearing or replace motor
General troubleshooting