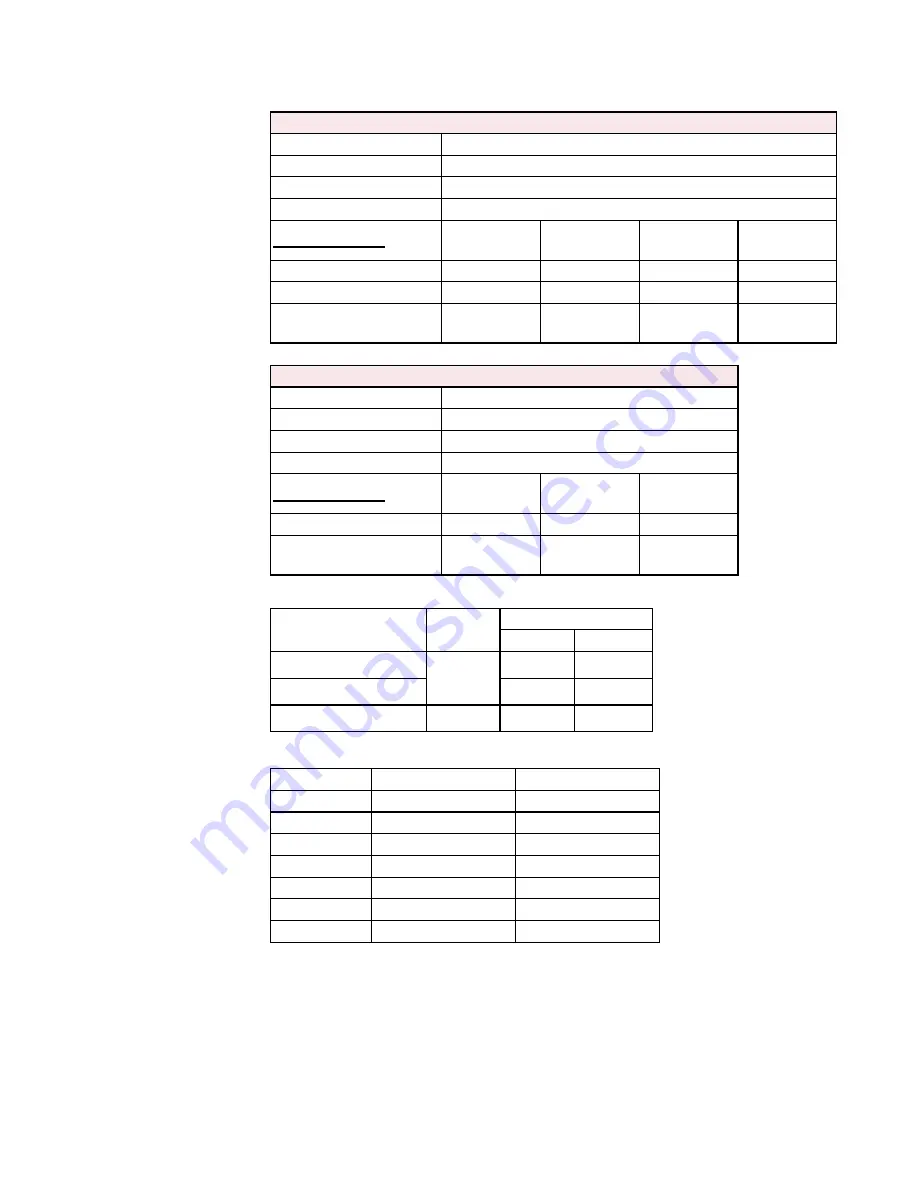
Form I-VR (10-14), P/N 205202 R14, Page 46
Model VR/GVR
Configuration Drawings
..................... Form T-VR-CNFG
Replacement
Parts ...........................................................Form P-VR/RIH
REFERENCES
(Forms are available on Website
www.ReznorHVAC.com or from
your Distributor.)
Addendum
(cont’d)
Model VR/GVR
Technical Information
Model VR (std 60 Hertz)
Voltage/Phase
Standard 115/1; Optional 208/1, 230/1
Frequency
60 hertz
Control Amps (24V)
0.8
Main Burner Ignition
Direct Spark
Full Load Amps
Sizes 50, 75,
and 100
Sizes 125
and 150
Size 175
Size 200
115V
1.1
0.8
1.2
1.2
Optional 208V or 230V
0.5
0.5
0.6
N/A
Maximum Overcurrent
Protection
15
15
15
15
BTUH Input
Gas Type
Supply Pressure
Minimum Maximum
50,000 - 150,000
Natural
Gas
4.5” w.c.
14” w.c.
175,000 - 200,000
6” w.c.
14” w.c.
50,000 - 200,000
Propane
11” w.c.
14” w.c.
BTUH Input
Minimum Length
Maximum Length
50,000
20 feet (6.1M)
40 feet (12.2M)
75,000
20 feet (6.1M)
40 feet (12.2M)
100,000
30 feet (9.1M)
50 feet (15.2M)
125,000
30 feet (9.1M)
60 feet (18.3M)
150,000
40 feet (12.2M)
60 feet (18.3M)
175,000
40 feet (12.2M)
70 feet (21.3M)
200,000
50 feet (15.2M)
70 feet (21.3M)
Gas Type and Supply
Gas Pressure
Electrical
Characteristics
BTUH/Length/
Configurations
Model VR (optional 50 Hertz) and Model GVR (std 50 Hertz)
Voltage/Phase
220-240/1 (Option AK11)
Frequency
50 hertz
Control Amps (24V)
0.8
Main Burner Ignition
Direct Spark
Full Load Amps
Sizes 50, 75,
and 100
Sizes 125
and 150
Size 175
Optional 220-240/1/50
0.5
0.5
0.6
Maximum Overcurrent
Protection
15
15
15