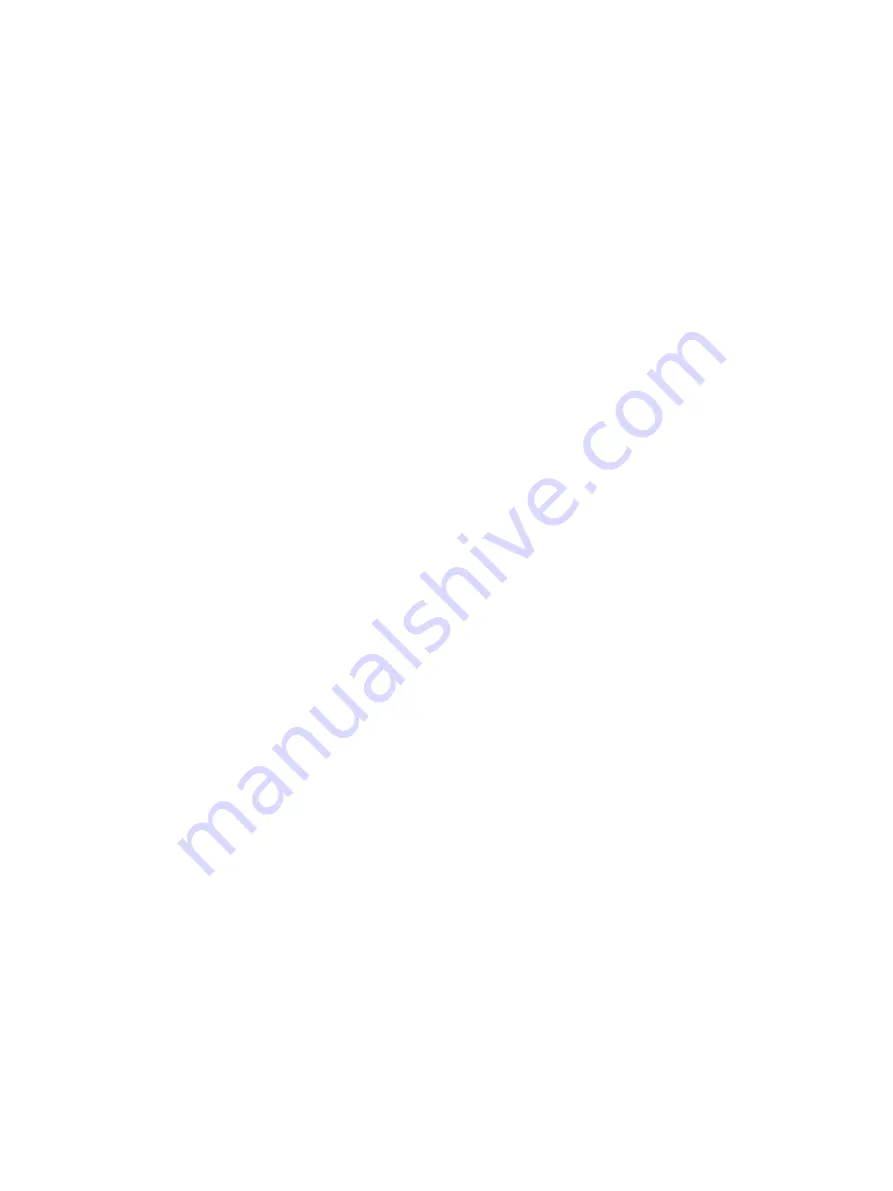
4/10
VT-HACD-DPQ
| Digital control electronics
Bosch Rexroth AG
, RE 30146, edition: 2013-10
time, and velocity limitation can be set in the holding
pressure profile.
Step 1 in the profile is started at the time of transition.
Every subsequent step in the holding pressure profile is
initiated when the previous step timer has been completed.
The velocity limitation in step 1 of the holding pressure
profile is usually used in order to avoid an early pressure/
force build-up in the injection cylinder if transition on the
basis of the position is selected. Apart from that, the DPQ
allows for faster reaction if transition is initiated based
on the internal mold pressure by reducing the command
value for the flow control valve to a smaller opening
within 2 msec in order to thus avoid pressure/force over-
shoots. In the following steps of the holding pressure
profile, the velocity limit is usually set higher so that
it does not limit the dynamics of the pressure/force con-
trol circuit.
Pre-retraction (pre-decompression)
After the last timer in the holding pressure profile has
been completed, the VT-HACD-DPQ will automatically
unload the worm. Pre-retraction is active if the position
parameter for the pre-decompression is larger than the
actual position of the injection cylinder at the end of the
holding pressure phase. The velocity parameter for the
pre-retraction is a valve control command. Pre-retraction is
complete as soon as the position of the injection cylinder
is equal to or larger than the pre-retraction position param-
eter. At the end of the pre-retraction, the VT-HACD-DPQ
will send a signal to the machine control and signal com-
pletion of the retraction. At the end of the pre-retraction,
the valve outputs will be set to 0 V.
Back pressure
Starting of the back pressure requires activation by the
machine control via the discrete input DI. The
VT-HACD-DPQ will then control the retraction of the injec-
tion unit on the basis of position and pressure and/or
force parameters in a 3-stage retraction profile.
The back pressure is changed in a regulated manner; it
does moreover have a subordinate controlled velocity
limitation. The next step in the retraction profile is trig-
gered during the ongoing retraction by a higher cylinder
position. In applications with hydraulic circuit with only
one injection valve, the velocity parameter is set for every
back pressure step as limitation of the valve pre-opening.
In a circuit with a separate proportional pressure relief
valve for the back pressure, the velocity parameter can be
Functional description: Injection control
(continued)
set to any valve value which is necessary for the propor-
tional directional valve for the injection, for some hydraulic
systems, this is e.g. the worm motor speed.
The worm retraction phase is completed if the injection
cylinder position is equal to or larger than the injection
position. The VT-HACD-DPQ signals reaching of the injec-
tion position to the machine control. The back pressure
control is maintained until post-decompression starts.
Post-retraction (post-decompression)
If the discrete input (DI6) for the post-retraction is activated
by the machine control, the post-decompression phase
starts when injection cylinder position is equal to or larger
than the the injection position. The velocity parameter for
the post-decompression is a valve control command.
Post-decompression is completed when the injection
cylinder position is equal to or larger than the post-decom-
pression position value. When post-decompression is
reached, the VT-HACD-DPQ will set the valve outputs to
0 V and signal this to the machine control.
Injection configuration options
Depending on the hydraulic system, the VT-HACD-DPQ can
be used with one of the two injection configurations.
1. Preferred configuration: Velocity control profile and
pressure control with one proportional injection valve
and one analog valve output. This system type controls
the rate of injection profile, the pressure profile, the
back pressure and the worm decompression by means
of a proportional directional valve. With this system
type, the available response dynamics are better than
with systems with separate valves for flow and pressure
control; this means that the control loop can be
adjusted for faster and exacter control.
2. Velocity control profile and open-loop or closed-loop
pressure control with one proportional directional valve
or flow control valve for the velocity profile and one
proportional pressure control valve for the injection
pressure control. For this configuration, two analog
valve outputs are available. This configuration does not
require the same degree of dynamic response from the
proportional flow control valve as the configuration
with a separate valve. Due to the limitations caused by
the distribution of current and pressure control func-
tions to several valves and the design-inherent dynamic
limitations of proportional pressure valves, the control
of the overall system is not as dynamic and repeatable.