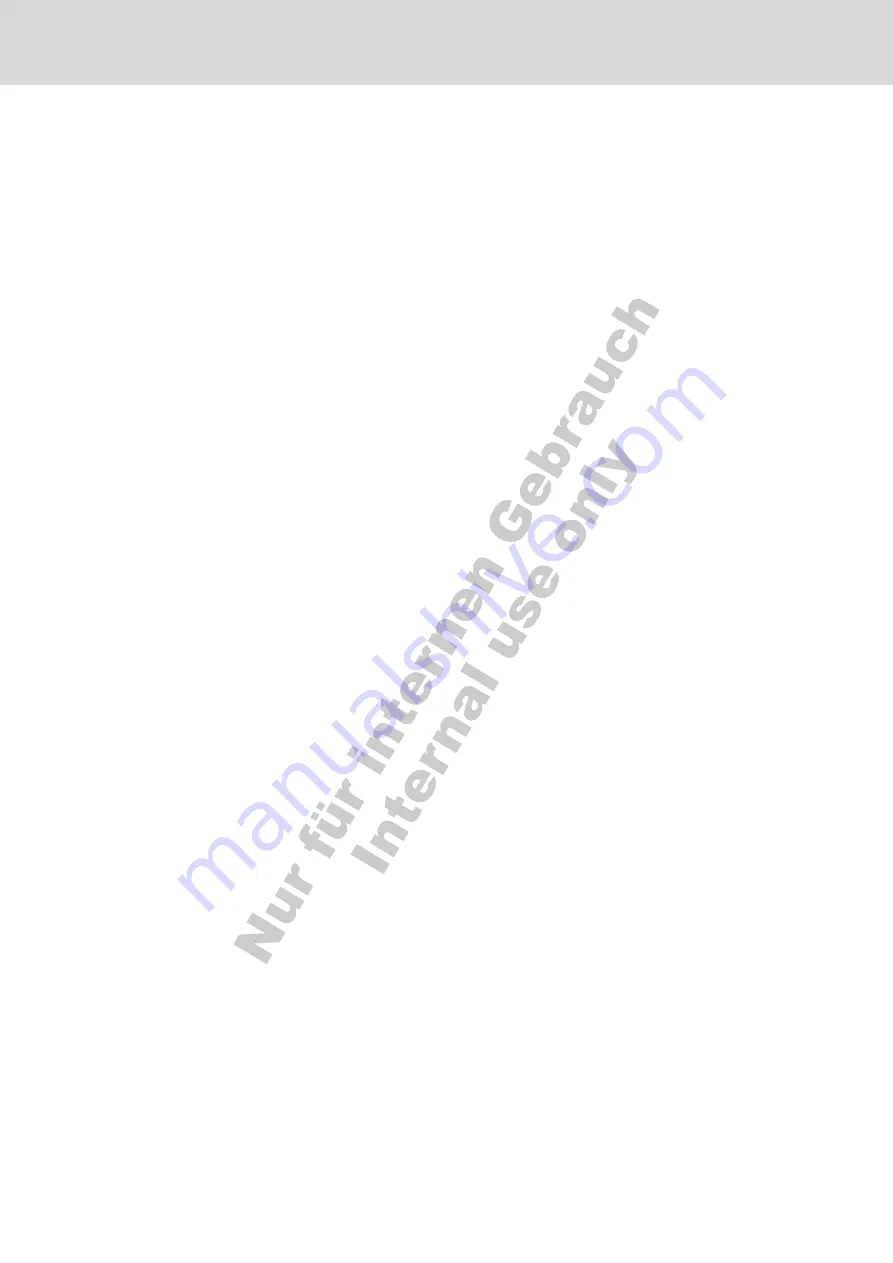
Mains Filters for AC Drives
Ideally, mount the mains filter on the parting line between area A and B.
make sure the ground connection between filter housing and housing of the
drive controllers has good electrically conductive properties.
If single-phase loads are connected on the load side of the filter, their current
may be a maximum of 10 % of the three-phase operating current. A highly
imbalanced load of the filter would deteriorate its interference suppression
capacity.
If the mains voltage is more than 480 V, connect the filter to the output side of
the transformer and not to the supply side of the transformer.
Grounding
In the case of bad ground connections in the installation, the distance be‐
tween the lines to the grounding points E1, E2 in area A and the other
grounding points of the drive system should be at least d4=400 mm, in order
to minimize interference injection from ground and ground cables to the pow‐
er input lines.
See also
"Division into areas (zones)" on page 155
Point of Connection for Environ‐
ment Grounding Conductor at Ma‐
chine, Installation, Control Cabinet
The equipment grounding conductor of the power cable of the machine, in‐
stallation or control cabinet has to be permanently connected at point PE and
have a cross section of at least 10 mm
2
or to be complemented by a second
equipment grounding conductor via separate terminal connectors (according
to EN 61800-5-1: 2007, section 5.3.2.1). If the cross section of the outer con‐
ductor is bigger, the cross section of the equipment grounding conductor
must be accordingly bigger.
Design and installation in area B – interference –susceptible area of control
cabinet
Arranging Components and Lines
Modules, components and lines in area B should be placed at a distance of
at least d1=200 mm from modules and lines in area A.
Alternative: Shield modules, components and lines in area B by distance
plates mounted vertically on the mounting plate from modules and lines in
area A or use shield lines.
Only connect power supply units for auxiliary or control voltage connections
in the drive system to the mains via a mains filter. See
.
Install the shortest possible lines between drive controller and filter.
Control Voltage or Auxiliary Volt‐
age Connection
Only in exceptional cases should you connect power supply unit and fusing
for the control voltage connection to phase and neutral conductor. In this
case, mount and install these components in area A far away from area B
and C of the drive system.
Run the connection between control voltage connection of the drive system
and power supply unit used through area B over the shortest distance.
Line Routing
Run the lines along grounded metal surfaces, in order to minimize radiation
of interference fields to area A (transmitting antenna effect).
Design and installation in area C – strongly interference-susceptible area of
control cabinet
Area C mainly concerns the motor power cables, especially at the connection
point at the drive controller.
Influence of the Motor Power Ca‐
ble
The longer the motor cable, the greater its leakage capacitors. To comply
with a certain EMC limit value, the allowed leakage capacitance of he mains
filter is limited.
●
Run the shortest possible motor power cables.
Routing the Motor Power Cables
and Motor Encoder Cables
Route the motor power cables and motor encoder cables along grounded
metal surfaces, both inside the control cabinet and outside of it, in order to
Bosch Rexroth AG
DOK-RCON02-FV*********IB01-EN-P
Rexroth Frequency Converter Fv
158/219
Technical Data
Summary of Contents for Fv Series
Page 20: ...Bosch Rexroth AG DOK RCON02 FV IB01 EN P Rexroth Frequency Converter Fv 18 219...
Page 30: ...Bosch Rexroth AG DOK RCON02 FV IB01 EN P Rexroth Frequency Converter Fv 28 219...
Page 34: ...Bosch Rexroth AG DOK RCON02 FV IB01 EN P Rexroth Frequency Converter Fv 32 219...
Page 52: ...Bosch Rexroth AG DOK RCON02 FV IB01 EN P Rexroth Frequency Converter Fv 50 219...
Page 58: ...Bosch Rexroth AG DOK RCON02 FV IB01 EN P Rexroth Frequency Converter Fv 56 219...
Page 144: ...Bosch Rexroth AG DOK RCON02 FV IB01 EN P Rexroth Frequency Converter Fv 142 219...
Page 164: ...Bosch Rexroth AG DOK RCON02 FV IB01 EN P Rexroth Frequency Converter Fv 162 219...
Page 180: ...Bosch Rexroth AG DOK RCON02 FV IB01 EN P Rexroth Frequency Converter Fv 178 219...
Page 214: ...Bosch Rexroth AG DOK RCON02 FV IB01 EN P Rexroth Frequency Converter Fv 212 219...
Page 216: ...Bosch Rexroth AG DOK RCON02 FV IB01 EN P Rexroth Frequency Converter Fv 214 219...
Page 220: ...Bosch Rexroth AG DOK RCON02 FV IB01 EN P Rexroth Frequency Converter Fv 218 219...
Page 221: ...Notes DOK RCON02 FV IB01 EN P Rexroth Frequency Converter Fv Bosch Rexroth AG 219 219...