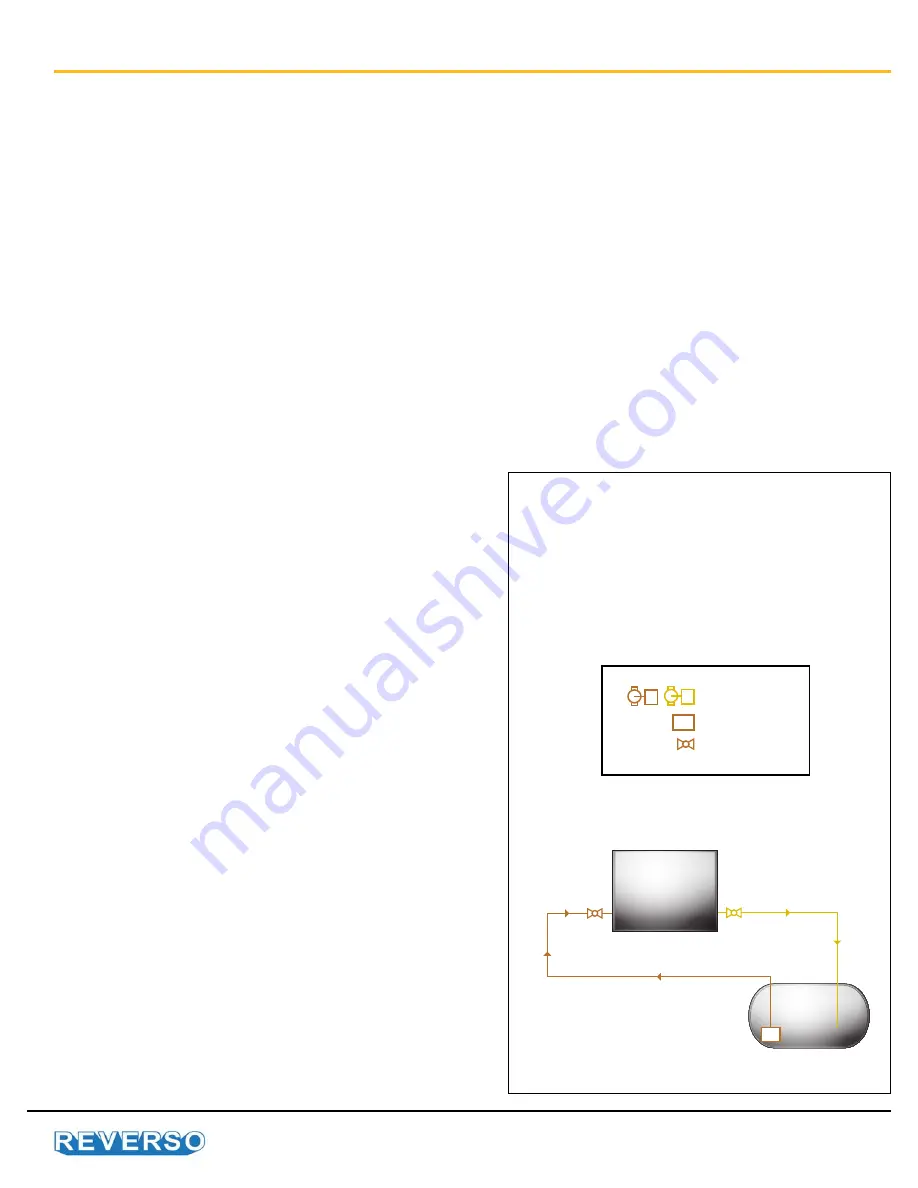
7
Reverso Pumps, Inc. www.reversopumps.com | [email protected] | Ph: (954) 522-0882
Primary Inspection, Installation, & Electrical Installation
Primary Inspection
• Upon delivery inspect the FPS (Fuel Polishing
System) for any damage that may have occurred
during shipment.
• Inspect the interior of the unit for mechanical or
electrical damage.
• If the unit is damaged upon delivery, contact the
shipping company immediately.
Mounting
• The FPS should be wall mounted on a hard, vertical
surface capable of supporting the weight of the unit.
• The control electronics are enclosed in a NEMA 4
weather proof box and will withstand being located
outside.
• In all cases the unit should be located as close as
possible to the tank being serviced. (see Max. Lift in
Technical Specifications).
• When installing the unit below the level of the fuel
on above ground fuel tanks, consideration should
be made to the installation of an anti-syphon valve
to prevent fuel spillage in the case of a leak in the
piping system.
Electrical
• Installation of unit should only be performed by
qualified installation personnel who have thoroughly
read and understands the installation instructions
covered in this manual.
• To avoid the risk of electric shock, make sure that
the power supply is disconnected. Ensure that the
power supply is at zero volts with a multimeter before
making any electrical connections.
• To ensure operator safety the FPS must be
connected to properly grounded power sources.
• Make sure that your unit and power supply are
configured for the same voltage rating.
• External control voltage must be supplied by
customer.
Piping
Use quality approved fuel line materials with at least
1/2” inner diameter line. Smaller plumbing will place
excessive load on the motor and shorten its life. A full
port ball valve should be installed on the inlet and outlet
ports of the FPS.
The pickup line(s) (suction) should originate from the
lowest point of the tank and should be connected directly
to the inlet. For optimal performance, ensure that this line
is free and nothing is restricting flow. It is recommended
to install a foot valve to keep the system primed,
especially if the system is located above the lowest
possible fuel level in the tank.
If the FPS is mounted below tank top level, a priming
tee should be installed on the highest point of the
suction line to be able to easily prime the systems
suction line.
The return line(s) (discharge) should be connected to
the outlet and enter the tank as far as possible from
the pick up tube and extending 2/3 down into the
tank. For optimal performance, ensure that the outlet,
discharge or return, line(s) are free and nothing is
restricting their flow.
The suction line of the FPS must be independent and
separate from the suction line of the engine. Do not
integrate into engine fuel system.
When installing this unit, FLEXIBLE CONNECTIONS
MUST BE USED TO REDUCE STRESS on the
plumbing and prevent damage to the unit.
Hoses, piping, solenoid valves and foot valves
shown in the diagrams below are not provided
with the system and must be provided by the
user/contractor, unless agreed upon otherwise.
Fuel
Tank
FV
Fuel
Polishing
System
Fuel
Tank
#
1
Fuel
Tank
#
2
Fuel
Tank
#
3
Fuel
Tank
#
4
S
S
S
S
S
S
S
S
FV
FV
FV
FV
S
S
FV
Solenoid valve
Foot valve
Ball valve