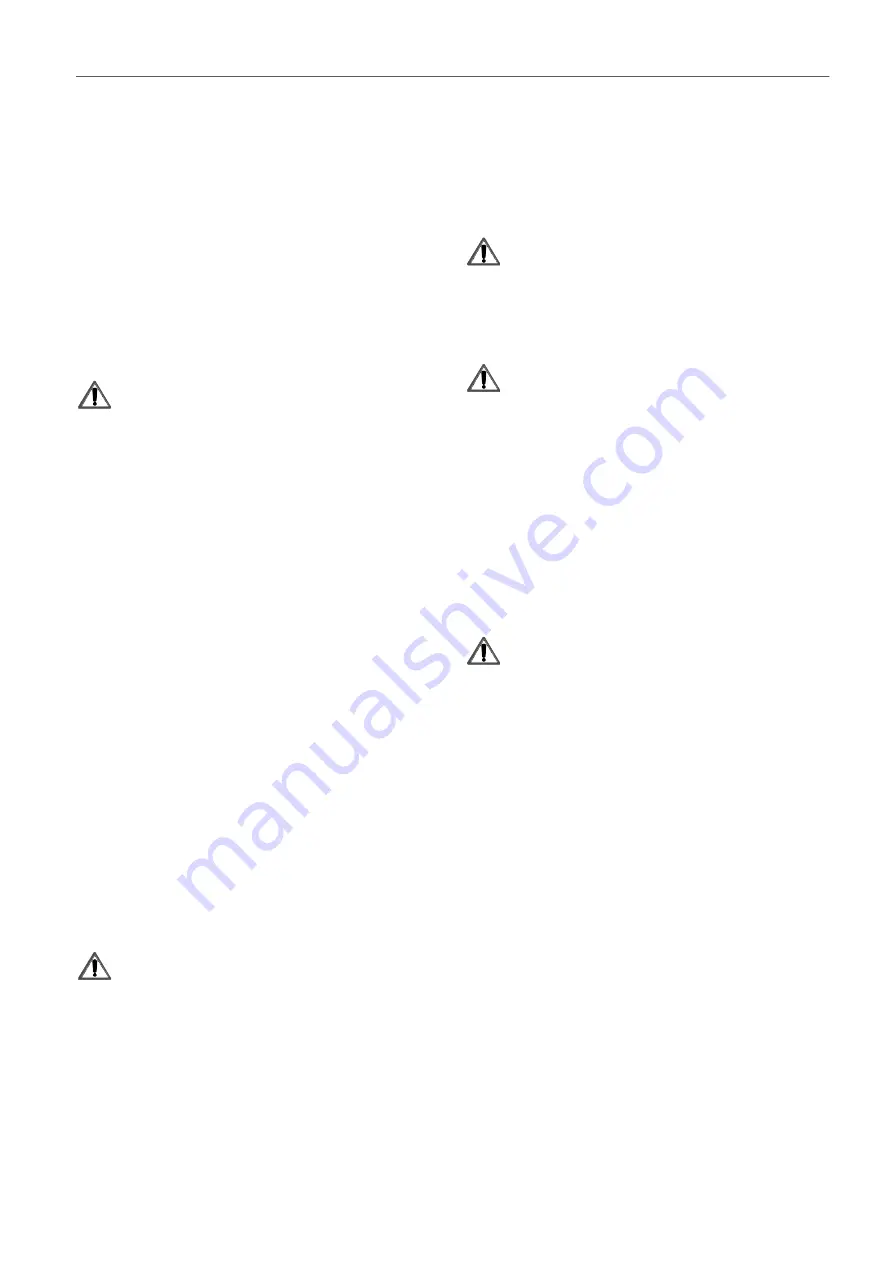
7
EN1R-1020 1004RANE
Gas leak test
•
Paint all pipe connections upstream of the gas control
with with a rich soap and water solution.Bubbles indicate
a gas leak.
•
If a gas leak is detected, tighten the pipe connection.
•
Stand clear while lighting the main burner to prevent
injury caused from hidden gas leaks, which could cause
flasback in the appliance vestibule. Light the main burner.
•
With the main burner in operation, paint all pipe joints
(including adapters) and gas control inlet and outlet with
with a rich soap and water solutionan approved leak
detection fluid.
•
If another gas leak is detected, tighten adapter screws,
joints and pipe connections.
•
Replace the part if gas leak can not be stopped.
CAUTION
Keep soap and water solution away from electrical
connections.
Electrical connections
IMPORTANT
Disconnect power supply to prevent electrical shock
and/or equipment damage.
Wiring must be in accordance with local regulations.
The appliance manufacturer’s instructions should
always be followed.
Before installing or replacing any control check that
type number is correct for the application.
Ensure combustion chamber is free of gas before
start up.
Conduct a thorough check out when installation is
completed.
At the first start the ignition control can be in lock-
out; depress reset button to free the ignition control.
Wiring
•
Use leadwire which can withstand 105 °C ambient.
•
Use leadwire which is proven against moisture.
•
Wiring between ignition control and spark sensing probe
should have good quality insulation, suitable for the
temperatures encountered.
Fusing
In order to prevent unsafe conditions at too high current, the
ignition control has an integral non replaceable fuse.
This fuse will be blown long before the maximum 16 A
external fuse switches off.
Sparkgap
Max. allowable spark gap 3.5 mm
Supply voltage polarity
WARNING
If ignition control seems to operate normally but does
not detect flame, check for right polarity of power
supply (line, neutral).
Checking flame current
•
The minimum value should be in accordance with the
specified value of the ignition control.
•
To check flame current connect a DC micro-Ampèremeter
between flame sensing wire and flame sensing rod.
•
If flame current is insufficient check that flame sensing
rod is fully enveloped by the flame and that burner is
reliable grounded to ignition control.
•
If there is no sufficient flame current due to phase-phase
mains it is recommandable to use a AT7030A or AT7030B
flame detection transformer. See also EN1R-9136
instruction sheet AT7030.
WARNING
Short
µ
A meter during ignition to prevent damage of
the
µ
A meter in single rod application.
ADJUSTMENTS
WARNING
Adjustments must be made by qualified persons only.
If the appliance manufacturer supplies checkout and/
or service and maintenance instructions carefully
follow them.
If such instructions are not provided then use the
procedure outlined below.
Adjustment can only be made with a special tool.
Pressure tap
The gas control is provided with a pressure tap of 9 mm O.D.
at inlet and outlet side.
When checking the pressure undo the screw a half turn and
slip tube over nipple.
Ensure that screw is retightened after making test.
CAUTION
To ensure a safe closing of the valves, it is essential
that voltage over the terminals of electric operators is
reduced to 0 Volt.
Offset adjustment VK41..V(B)/VK81..V(B) (see fig. 1.)
•
Remove cap screw with a Torx T-40 screw driver or 5 mm
hex key to expose offset adjustment screw.
•
Check gas supply pressure to the appliance using a
pressure gauge connected to the inlet pressure tap.
•
Start fan and check air flow.
•
Energize both electric operators in order to have gas input
to burner and ignite boiler.
•
Adjust CO
2
% at the desired value at low output with
offset adjustment screw. Turn offset adjustment screw
clockwise to increase CO
2
%.
•
Operate boiler on high output. (Only modulating
applications).
•
Replace cap screw and tighten pressure taps.