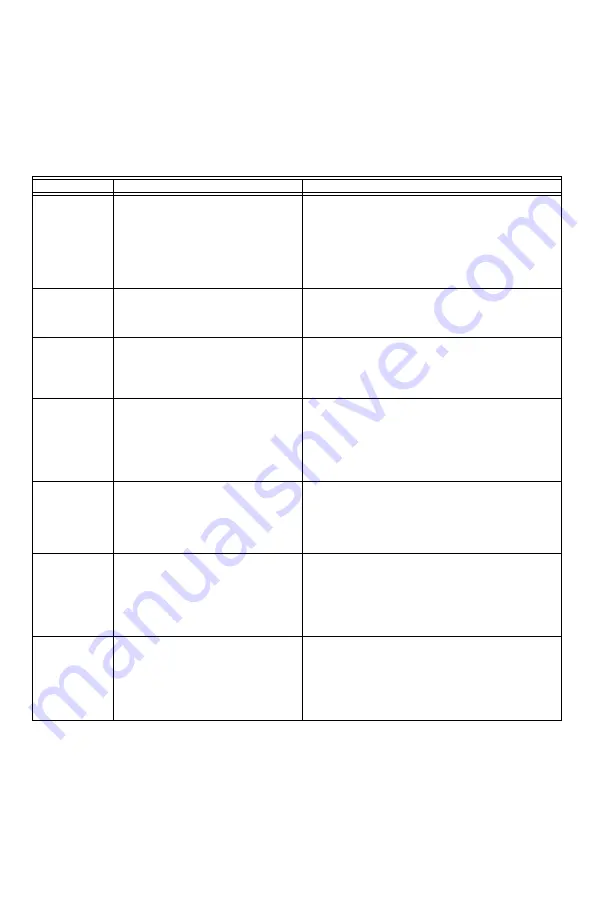
SV9541, SV9641 SMARTVALVE™ SYSTEM CONTROLS
69-2012—01
16
1.
Check the system thermostat to make sure it is
calling for heat. (Do not cycle the thermostat on
and off at this time.)
2.
Remove the appliance burner compartment door.
Do not interrupt power to the SV9541 or SV9641 by
opening any electrically interlocked
panels.
3.
Observe the LED indicator on the SV9541 or
SV9641; check and repair system as noted in
Table 9. Troubleshooting with LED indicator assistance for ignition controls using
ST9160 Fan Timer or 208907 Terminal Board.
LED Status
Indicates
Check/Repair
OFF
No power to system control
1.
Line voltage input power at L1 and L2 connectors
on ST9160 Electronic Fan Timer (EFT) or 208907
Terminal Board.
2.
Low voltage (24V) power at 24 VAC and COM ter-
minals on ST9160 or Terminal Board.
3.
Fuse on ST9160 EFT if provided.
4.
System wiring harness is in good condition and
securely connected at both ends.
Bright-Dim
Normal Operation
This indication shows whenever the
system is powered, unless some
abnormal event has occurred.
Not Applicable
2 Flashes
Airflow proving switch remains closed
longer than 30 second after a call for
heat begins.
Combustion air blower is not energized
until airflow proving switch opens.
1.
Airflow proving switch stuck closed.
2.
Airflow proving switch miswired or jumpered.
3 Flashes
Airflow proving switch remains open
longer than 30 seconds after
combustion air blower energized.
System goes into 5 minute delay period,
with combustion air blower off. At the
end of the 5 minute delay, another
ignition cycle will begin.
1.
Ignition system control switch must be in the ON
position.
2.
Airflow proving switch operation, tubing, and wir-
ing.
3.
Obstructions or restrictions in appliance air intake
or exhaust flue system that prevent proper com-
bustion airflow.
4 Flashes
Limit string is open.
Combustion air blower is energized. If
control system includes ST9160
Electronic Fan Timer, the heat speed
circulating air fan will be energized until
the limit string resets.
1.
Open manual reset or auto reset burner rollout
switch.
2.
Open high temperature or auxiliary limit switch.
3.
Limit and rollout switch wiring is in good condition
and securely connected.
5 Flashes
Flame signal sensed out of proper
sequence.
Combustion air blower is energized. If
control system includes ST9160
Electronic Fan Timer, the heat speed
circulating air fan will be energized after
the selected heat fan on delay.
Flame at pilot burner.
6 Flashes
System Lockout
After 5-minute delay time, control
system resets and initiates a new
ignition sequence if the call for heat is
still present.
1.
Gas supply off or at too low pressure to operate.
2.
Damaged or broken HSI element.
3.
Flame sense rod contaminated or in incorrect
location.
4.
Pilot burner located in incorrect position.
5.
Pilot burner leadwires are in good condition and
properly connected.