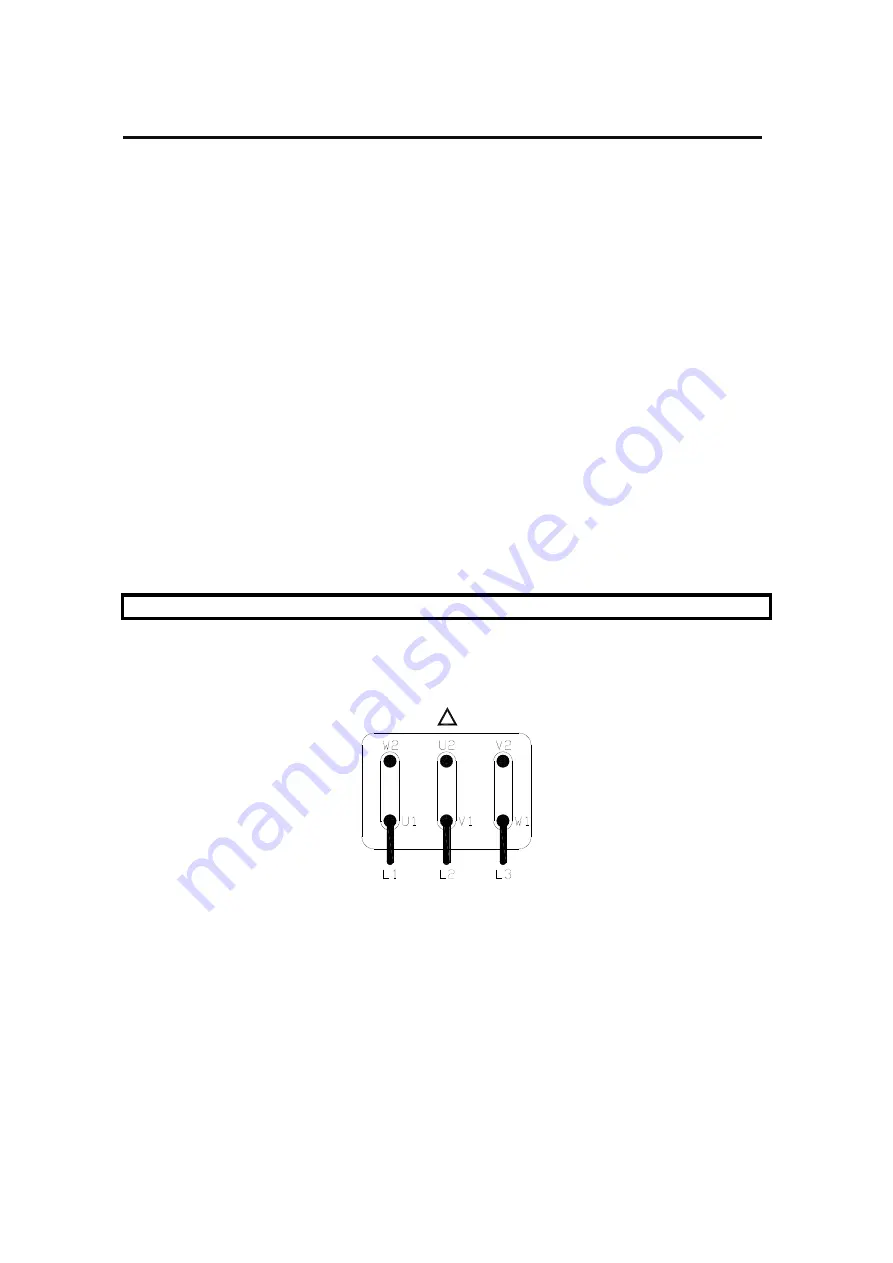
def
jPM Series
Gears
INSTALLATION & MAINTENANCE GUIDE
16
Appendix C
MOTOR CIRCUIT DIAGRAMS
The following motor circuit diagrams are relevant for jPM Series gear units supplied with our standard
motors already fitted. For motor ready gear units, please refer to the motor supplier’s installation and
maintenance instructions for that particular motor.
Standard motors are provided with a terminal box, which contains six connections, to which six leads
from the winding are connected either in a delta connection, or in a star connection by means of metallic
connection links.
Usually, two voltages will be displayed on the rating plate of the motor. This means that the motor can be
connected to a circuit which has one of these voltages. If the mains voltage corresponds to the lowest
indicated voltage shown on the rating plate, then the motor winding has to be connected as a Delta
connection (refer to C.1). However, if the mains supply has a voltage equalling the highest indicated
voltage as shown on the rating plate, then the motor must be connected as a Star connection (refer to C.2).
For example, a motor with 230/400V indicated on its rating plate, is suited either to a circuit with a
voltage of 230V with the winding connected in a Delta connection; or on a circuit with a voltage of 400V
with the winding connected in a Star connection.
For pole change motors (for two or more speeds) and brake motors, please refer to the wiring connection
diagram which will be sent with the motorised gear unit.
WARNING:
Electrical connections should only be carried out by a fully qualified electrician.
C.1
Delta Connection Procedure
To complete a Delta connection:
I.
Link W2-U1, U2-V1 and V2-W1 using the metallic strips provided.
II.
Connect Line 1 (L1) to U1, Line 2 (L2) to V1 and Line 3 (L3) to W1.
III.
Connect the Earth wire to the separate terminal supplied.
IV.
Turn on the power supply and check the direction of rotation.
V.
If the direction of rotation is incorrect, swap over any two of the “line - in” wires. For example, Line 1
(L1) to V1 and Line 2 (L2) to U1, etc.