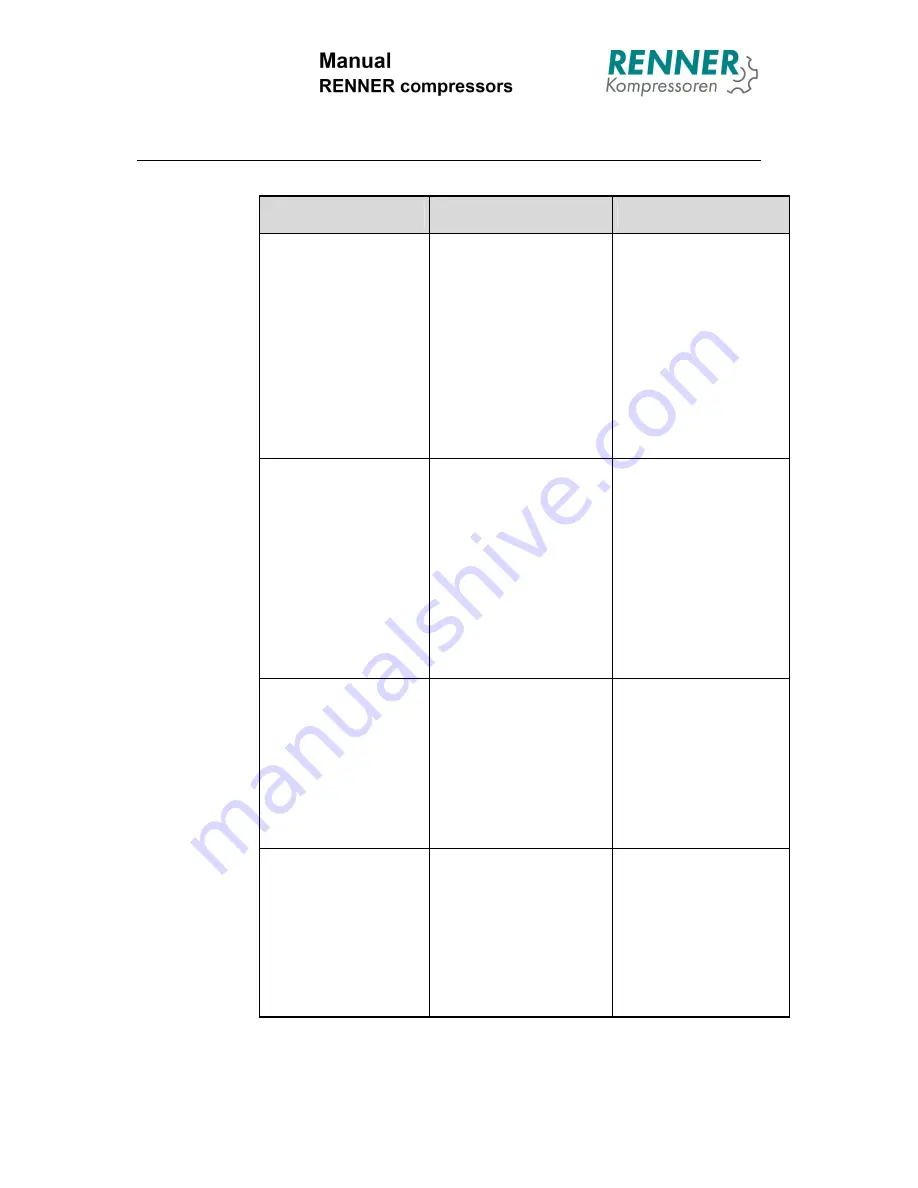
4 Operation / Normal use
4 - 13
4.6 Remedying malfunctions in normal operation (continuation)
Fault
Possible Cause
Remedy
Oil in compressed air
•
Oil scavenge line and
nozzle in oil sight
glass clogged
•
Separator cartridge
defective
•
Oil tank level too high
•
Compressor was
stopped
before end of run-on
time
Have oil scavenge
system cleaned
Check cartridge and
replace if necessary
Rectify oil level
Never switch off
compressor until run-
on time has elapsed
Compressor does not
vent during continuous
operation; compressor
does not cut out during
intermittent operation,
i.e. safety valve blows
•
Upper trigger point of
discharge pressure
switch set too high
•
Solenoid valve defec-
tive
•
Relief valve defective
•
Minimum pressure
valve jamming
Reset discharge
pressure switch
Change solenoid
valve
Change relief valve
Check and adjust
minimum pressure
valve
Compressor vents
continuously; low vol-
umetric capacity
•
Solenoid valve defec-
tive
•
Relief valve defective
•
Electric supply to so-
lenoid valve discon-
nected
•
Auxiliary contact on Y-
contactor defective
Change solenoid
valve
Change relief valve in
intake regulator
Restore supply line
connection
Check switch and
replace if necessary
Non-existent or insuffi-
cient discharge capaci-
ty
•
Intake filter clogged
•
Intake regulator or
intake valve jamming
or positioned incor-
rectly
(continuous operation)
•
Leaks in the system
Change air filter
Check regulator and
butterfly valve and
clean bearing and
guides
Rectify leaks
Continued overleaf
Malfunctions
(contd.)