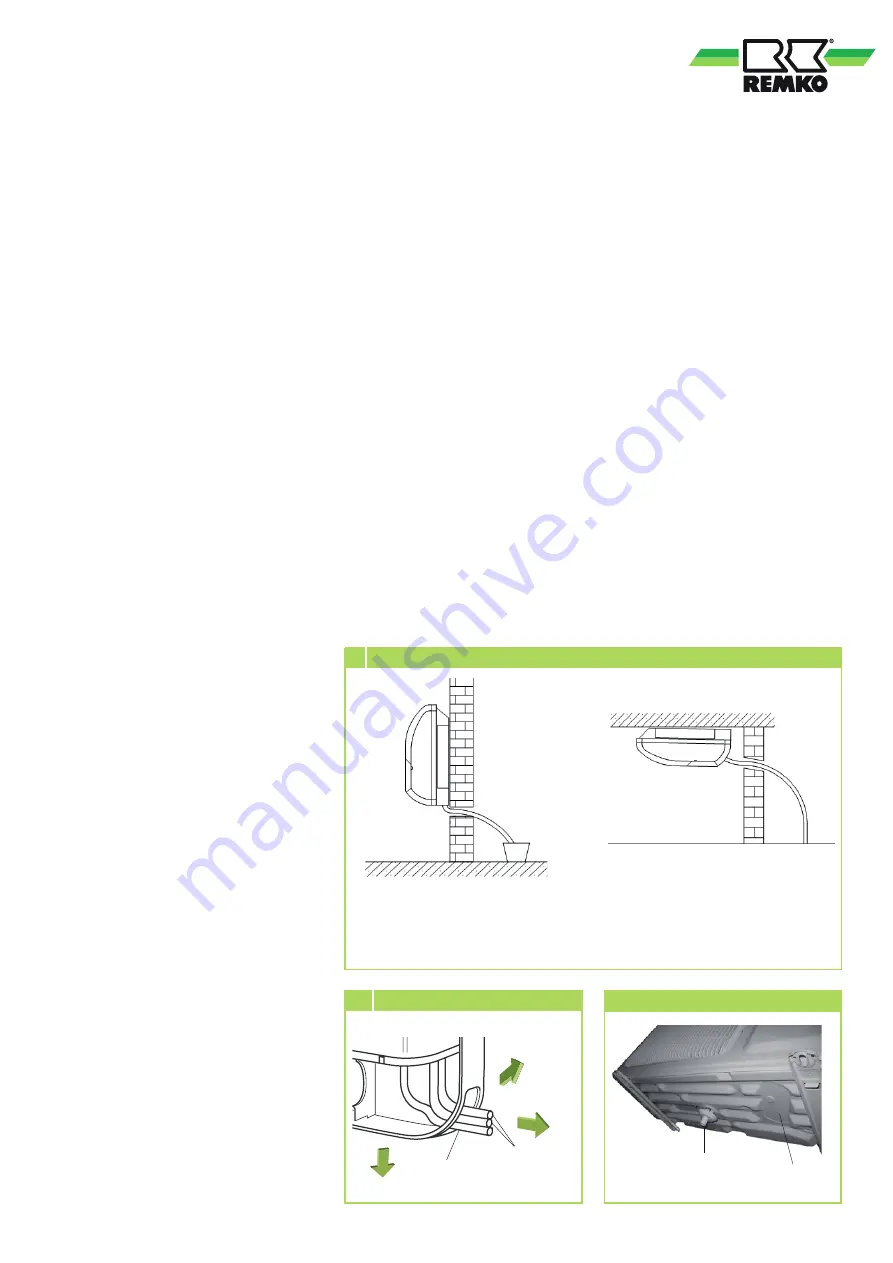
10
Slope of the condensate line
Wall installation:
The condensation hose is led out of
the bottom or rear of the indoor unit
Ceiling installation:
The condensation hose is led out of
the unit through the oval opening in
the housing, near to the grill
11
Condensate drain, wall installation
Refrigerant pipe
Condensate drain
Wall installation
1. Use the outlet on the side,
bottom or back of the unit
(Fig. 11)
.
2. If necessary, remove the break
out opening of the housing and
connect the condensate line to
the condensate hose.
Installation location
Condensate connection, outdoor component
Condensation pan of
the outdoor component
Condensate connection
Ceiling installation
The unit is attached by means of
the ceiling bracket, taking account
of the air outlet side, which is
located on the front of the unit.
1. Mark the mounting points on
the structurally permissible
building sections according to
the dimensions of the ceiling
bracket.
2. Remove the housing's break
out opening if necessary.
3. Hook the unit on to the
previously attached support rail.
4. Fit the unit such that it is
attached 5 mm lower in the
connection area (air intake)
than on the air outlet side!
5. Connect the refrigerant
pipes, electrical cables and
condensation pipe to the indoor
unit as described below.
Condensate connection
If the temperature falls below the
dew point, condensation will form
on the finned condenser during
heating mode
.
Below the register is a collection
tray, which must be connected to
a drain.
■
The condensate line should
have a fall of min. 2 %.
This is the responsibility of the
customer.
(Fig. 10)
. If necessary,
fit vapour diffusion proof
insulation.
■
Route the condensate line of
the unit freely into the drain
line. If the condensation runs
directly into a sewer pipe,
install a trap to prevent any
unpleasant odours.
■
When operating the unit at
outdoor temperatures below 4 °C,
make sure to route the condensate
line so that freezing is prevented.
The lower part of the housing
must also be kept frost free by the
user, in order to ensure permanent
draining of the condensate.
If necessary, fit a pipe heater.
■
After installation is complete,
check for unobstructed
condensation run off and
ensure that a permanent seal is
provided.
Safe drainage in the event of
leakage
Local regulations or environmental
laws, for example the German Water
Resource Act (WHG), can require
suitable precautions to protect
against uncontrolled drainage in
case of leakage to provide for safe
disposal of escaping air conditioning
fluid or hazardous media.
Condensate connection
and safe drainage
21