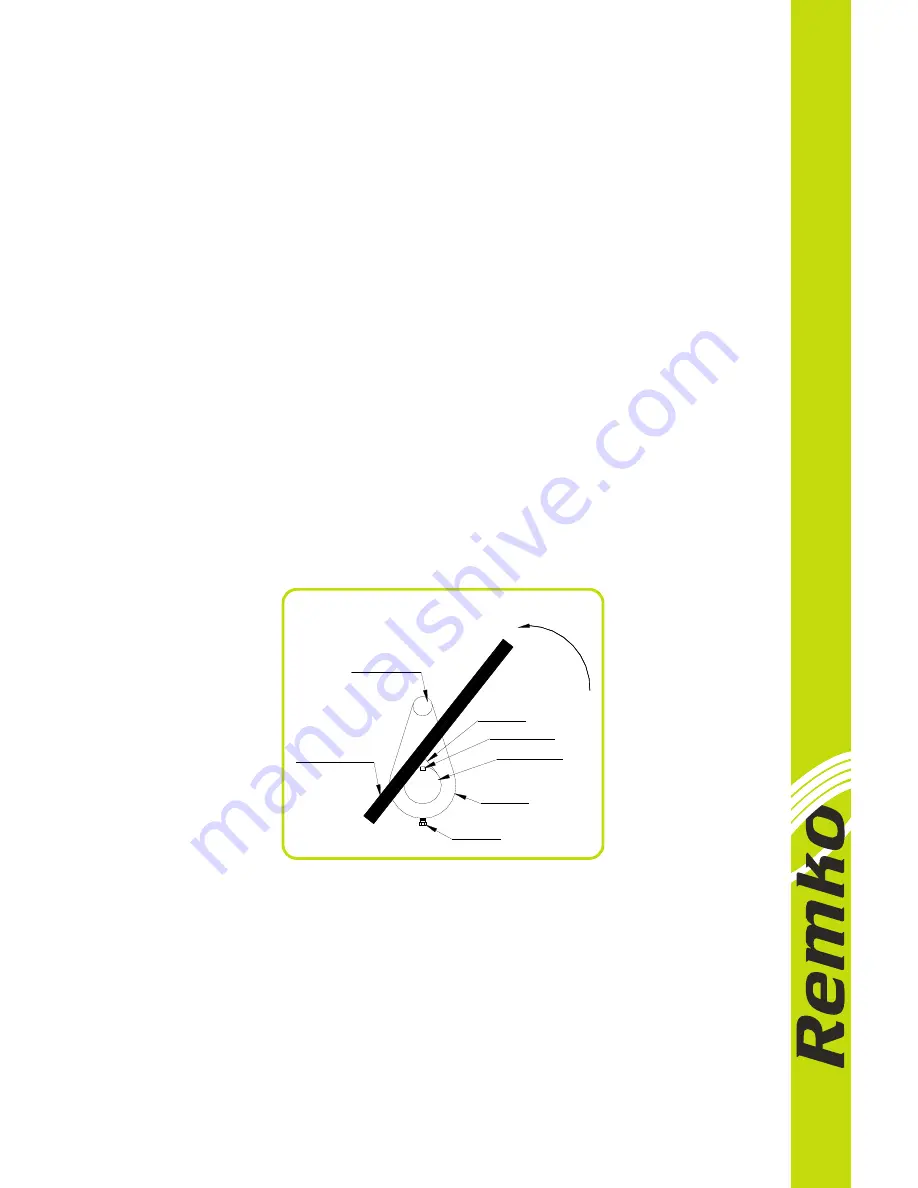
27
Figure 12. Loosening impeller
(Figure 10, Page 21)
Remove the hardware (13 and 14) securing the rotating assembly to the pump casing.
Separate the Rotating assembly by pulling straight away from the pump casing.
NOTE:
An optional disassembly tool is available from the factory. If the tool is
used, follow the instructions packed with it. A similar tool may be assembled
using ½ inch pipe (schedule 80 steel or malleable iron) and a standard tee (see
Figure 13, Page 27). All threads are ½ inch NPT. Do not pre-assemble the tool.
Turn
Counterclockwise
Lathe Dog Arm
Heavy Bar Stock
Set Screw
Lathe Dog
Impeller Shaft
Shaft Keyway
"V" Notch
NOTE:
Further disassembly of the check valve is not required since it must be
replaced as a complete unit. Individual parts are not sold separately.
Rotating Assembly Removal
(Figure 11, Page 23)
The rotating assembly may be serviced without disconnecting the suction or discharge
piping; however, the power source must remove to provide clearance.
The impeller (1) should be loosened while the rotating assembly is still secured to the
pump casing. Before loosening the impeller, remove the seal cavity drain plug (24) and
drain the seal lubricant. This will prevent the oil in the seal cavity from escaping when
the impeller is loosened. Clean and reinstall the seal cavity drain plug.
Immobilize the impeller by wedging a wood block between the vanes and the pump
casing, and remove the impeller cap screw and washer (10 and 12).
Install a lathe dog on the drive end of the shaft (17) with the “V” notch positioned over
the shaft keyway.
With the impeller rotation still blocked, see Figure 12 below and use a long piece of
heavy bar stock to pry against the arm of the lathe dog in a counterclockwise direction
(when facing the drive end of the shaft).
Use caution
not to damage the shaft or
keyway. When the impeller breaks loose, remove the lathe dog and wood block.
NOTE:
Do not remove the impeller until the rotating assembly has been removed
from the pump casing.