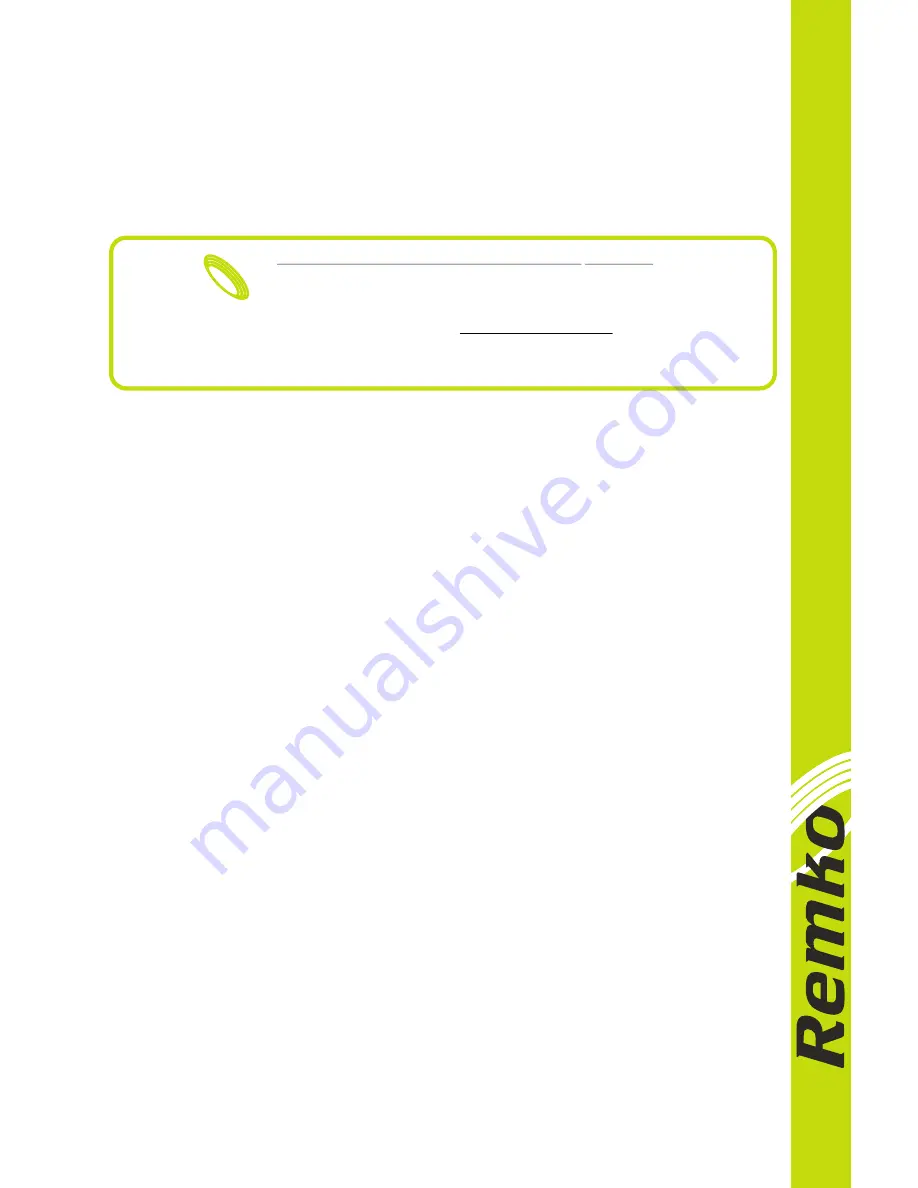
16
Liquid Temperature and Overheating
The
maximum
liquid temperature for this pump is 71º C. Do not apply it at a higher
operating temperature.
Overheating can occur if operated with the valves in the suction or discharge lines
closed. Operating against closed valves could bring the liquid to a boil, build pressure,
and cause the pump to rupture or explode. If overheating occurs, stop the pump and
allow it to cool before servicing it. Refill the pump casing with cool liquid.
Allow an over-heated pump to cool before servicing. Do not remove
plates, covers, gauges, or fittings from an overheated pump. Liquid
within the pump can reach boiling temperatures, and vapour
pressure within the pump can cause parts being disengaged to be
ejected, with great force. After the pump cools, drain the liquid from
the pump by removing the casing drain plug. Use caution when
removing the plug to prevent injury to personnel from hot liquid.
DANGER!
As safeguard against rupture or explosion due to heat, this pump is equipped with a
pressure relief valve which will open if vapour pressure within the pump casing reaches
a critical point. If overheating does occur, stop the pump immediately and allow it to
cool before servicing it. Approach any overheated pump cautiously. It is recommended
that the pressure relief valve assembly be replaced at each overhaul, or any time the
pump casing overheats and activates the valve. Never replace this valve with a
substitute which has not been specified or provided by Remko.
Strainer Check
If a suction strainer has been shipped with the pump or installed by the user, check the
strainer regularly, and clean it as necessary. The strainer should also be checked if
pump flow rate begins to drop. If a vacuum suction gauge has been installed, monitor
and record the readings regularly to detect strainer blockage.
Never
introduce air or steam pressure into the pump casing or piping to remove a
blockage. This could result in personal injury or damage to the equipment. If back
flushing is absolutely necessary, liquid pressure
must
be limited to 50% of the
maximum permissible operating pressure show on the pump performance curve.
Pump Vacuum Check
With the pump inoperative, install a vacuum gauge in the system, using pipe dope on
the threads. Block the suction line and start the pump. At operating speed the pump
should pull a vacuum of 508mm or more of mercury. If it does not, check for air leaks in
the seal, gasket, or discharge valve.
Open the suction line, and read the vacuum gauge with the pump primed and at
operation speed. Shut off the pump. The vacuum gauge reading will immediately drop
proportionate to static suction lift, and should then stabilize. If the vacuum reading falls
off rapidly after stabilization, an air leak exists. Before checking for the source of the
leak, check the point of installation of the vacuum gauge.