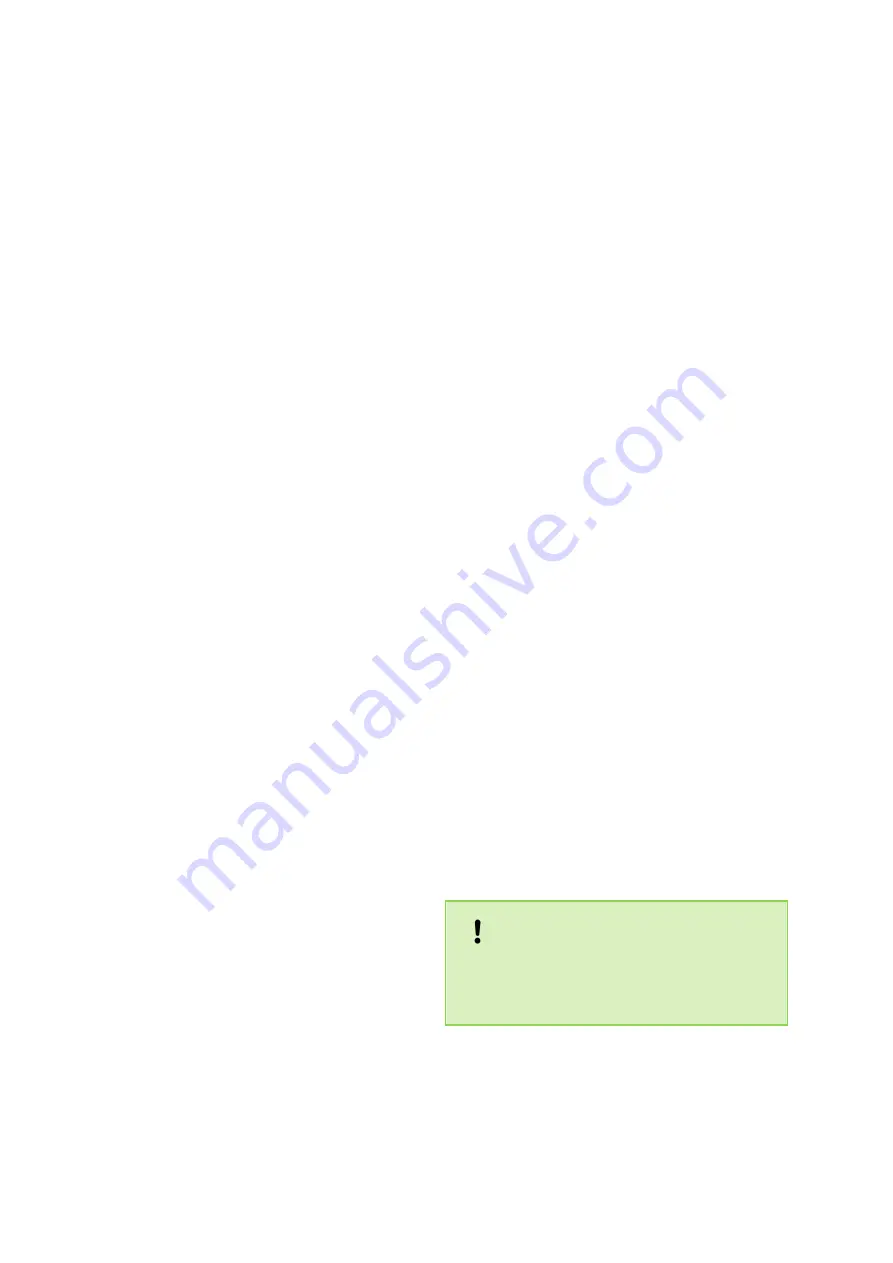
n
Sufficient ventilation
Before starting work, ensure that the working
area is outdoors or has sufficient ventilation. A
continuous ventilation stream is required while
working. The safety of the persons working
must be guaranteed by the exhaust air equip-
ment: potentially leaking refrigerant must be
lead away safely and drained into the atmos-
phere in an optimum manner.
n
Checking the refrigerant circuit
If electronic components need to be replaced,
ensure that the spare parts have the same
function and identical technical specifications.
The maintenance and replacement regulations
of the manufacturer must always be observed
and complied with. Please contact the support
of the manufacturer with any problems or
queries. The following safety checks must be
carried out when using combustible refriger-
ants:
- The fill level adjusts to the size of the rooms
in which the unit is located.
- The exhaust air equipment and its outlets
function properly and are not blocked or
obstructed.
n
Checking the electronic components
A component and safety check must be carried
out before repairing and maintaining electronic
components. If safety cannot be ensured due
to a defect on a component, installation must
not take place until safety can be guaranteed
again. If the defect on the spare part cannot be
remedied and downtime of the unit is no longer
acceptable, an adequate temporary solution
must be arranged. The owner/operator of the
unit must be informed about this. The detailed
safety check must include the following
aspects:
- Capacitors are discharged. Discharging must
be done in a safe process to prevent flying
sparks.
- There must be no electronic components
active or uninsulated wires while filling,
repairing or cleaning.
- There must be no earthing of the system.
n
Repairs to closed components
Before repairing closed components/housing
parts, the unit must be free from voltage. If car-
rying out the repairs free from voltage cannot
be avoided, the critical points of potential refrig-
erant leakages must be checked using a leak
detector.
The following notes must be observed when
working on electronic components if the
housing is changed in such a way that its
safety is influenced. This also relates to cases
where the lines are damaged, there is exces-
sive or incorrect pin assignment, connections
are not assigned in the original way or similar
deviations to the expected condition are deter-
mined.
n
Repairing of intrinsically safe components
Do not introduce permanent inductive or
capacitive loads into the existing circuits
without ensuring that the maximum permitted
voltages and amperages of the assemblies and
lines are not exceeded. Intrinsically safe com-
ponents are individual components that can be
operated in the presence of flammable sub-
stances. The test equipment must be adjusted
according to the situation-dependent condi-
tions. Only use components which are officially
approved by the manufacturer as spare parts.
Unapproved components can cause a fire in
the event of a leakage in the refrigerant circuit.
n
Wiring
Lines must be checked for the following
damage:
- Damage to the insulation
- Corrosion at the contact points
- Excessive pressure on the lines
- Damage due to vibrations
- Damage due to sharp edges
- Damage due to other influences not men-
tioned here
Also consider the ageing of the material and
continuous vibration loads due to compressors
or fans when checking.
n
Identify combustible refrigerant
Do not use any potential ignition source when
searching for refrigerant leaks under any cir-
cumstance. The use of a leak detection lamp
or other similar devices with a naked flame is
not permitted.
1. Ensure that the components are installed
correctly.
2. Ensure that sealing materials are not
changed in such a way that combustible gases
or objects could penetrate into the interior of
the components.
3. Spare parts must correspond to the manu-
facturer’s specifications.
NOTICE!
The use of silicones can influence the effective-
ness of leak detection devices! Intrinsically safe
components must not be insulated before
starting work.
REMKO MKT ECO series
8
Summary of Contents for MKT 255 ECO S-Line
Page 26: ...REMKO MKT ECO series 26...
Page 27: ......