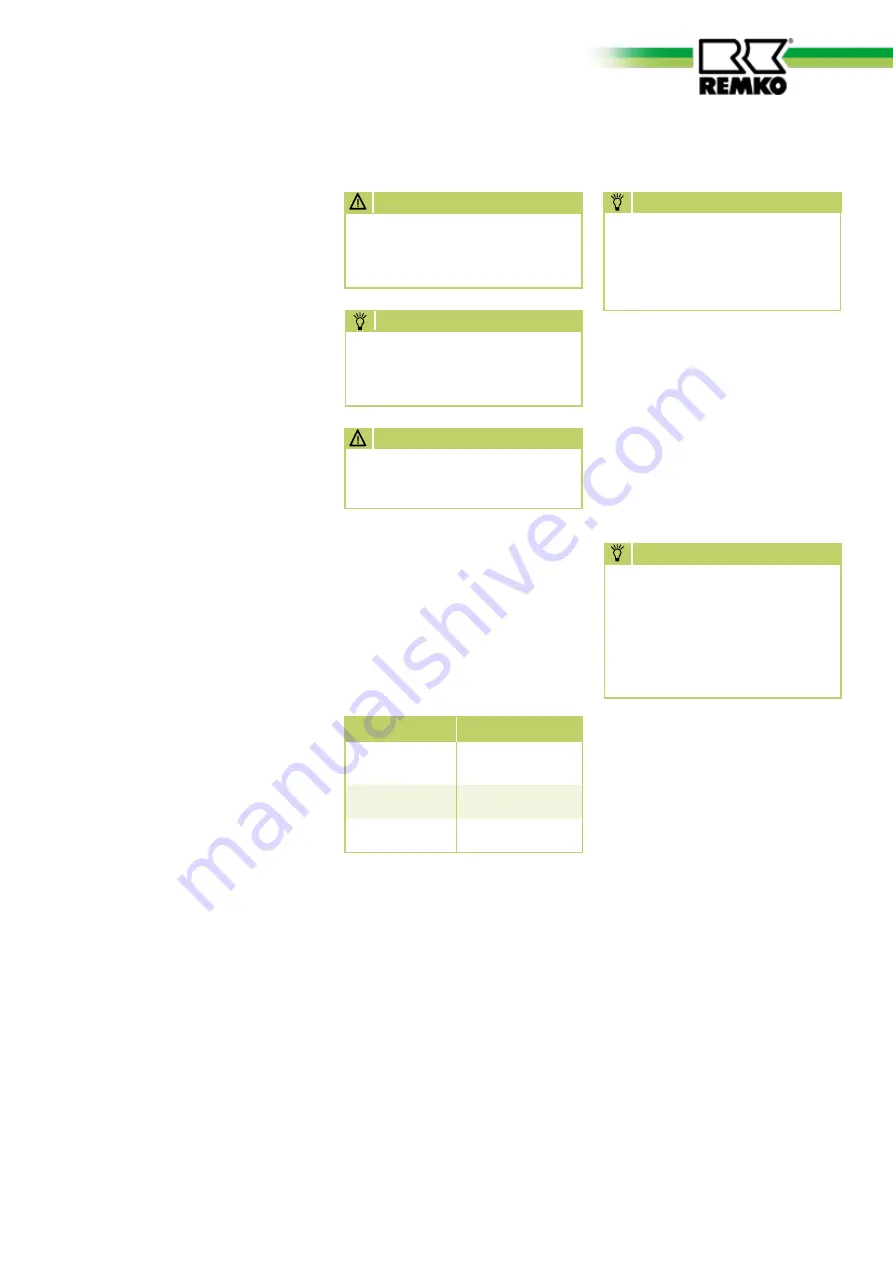
Add refrigerant
The equipment contains a basic
quantity of refrigerant. Beyond
these conditions, for refrigerant
pipe lengths of more than 5 meters
per circuit, an additional amount
of refrigerant must be added,
according to the following chart:
RVT 261 / 351
Basic pipe length
Additional fill
quantity
Up to and incl.
5m
0 g/m
5m to max. 15m
30 g/m
After the tightness check has
been successfully completed,
connect the vacuum pump via
the pressure gauge station to
the valve connections on the
outdoor component (see chapter
"Tightness check") and create a
vacuum.
Perform the following checks
prior to commissioning the
unit for the first time and after
any interventions affecting the
refrigerant circuit. Record the
results in the commissioning
report:
■
Check of all refrigerant
pipes and valves with leak
detection spray or soapy water
for leaks and for inadvertent
mix up of suction and injection
pipe, with the unit at a
standstill.
■
Check of all refrigerant
pipes and insulation for
damage.
■
Check of all electrical
connections between indoor
unit and outdoor component
for correct polarity.
■
Check that all fastenings,
mountings etc. are firm and at
the correct level.
Before
commissioning
Note that the employed
refrigerant is always filled in
liquid form!
CAUTION
NOTE
Check the overheating to
determine the refrigerant fill
quantity
Wear protective clothing when
handling refrigerant.
CAUTION
Commissioning
Commissioning should only
be performed
and documented by specially
trained personnel.
NOTE
The system can be commissioned
once all the components have
been connected and tested.
A functional check should be
performed to verify its correct
function and identify any unusual
operational behaviour prior to
handing it over to the operator.
Function test and test run
Check the following points:
■
Leak tightness of refrigerant
pipes.
■
Compressor and fan running
smoothly.
■
In cooling mode, cold air should
be output by the indoor unit,
and warm air should be output
by the outdoor component.
■
Functional test of the indoor
unit and all program sequences
■
Check of the surface
temperature of the suction
pipe and determination of
vaporiser overheating. To
measure the temperature, hold
the thermometer to the suction
Check that the stop valves
and valve caps are tight after
carrying out any work on the
refrigerant circuit. If necessary,
use appropriate sealant
products.
NOTE
25
Summary of Contents for MD 261
Page 2: ......
Page 31: ...Notes 31...