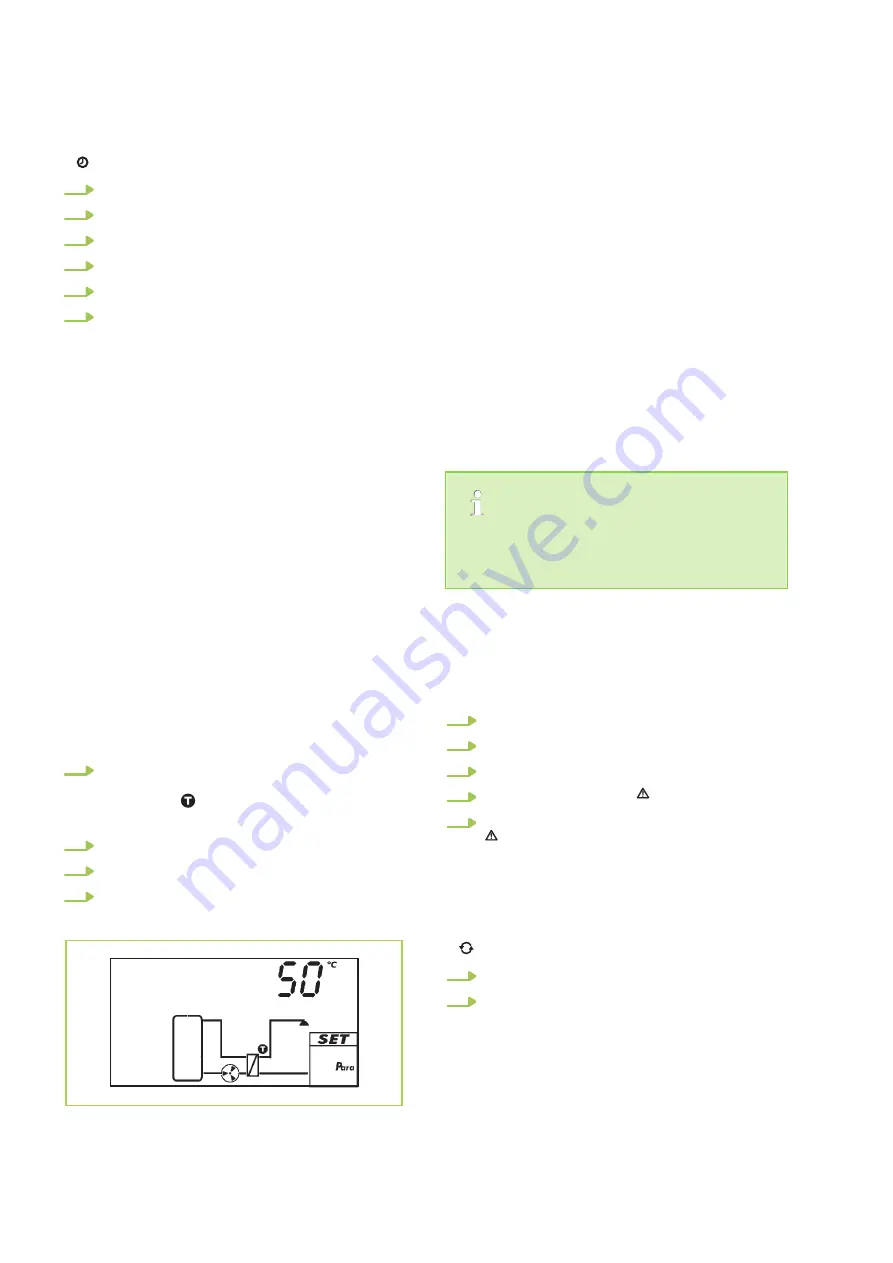
Setting the time
√ flashes.
1.
Press "SET". The hour flashes.
2.
Press "
rs
" to set the hour.
3.
Press "SET". The minute flashes.
4.
Press "
rs
" to set the minute.
5.
Press "SET".
6.
Repeat steps 4 and 5 to set the year, month
and date.
Set functions
√
Func
flashes.
Proceed as described in
Set the domestic hot water target temperature
Method of operation
The controller attempts to regulate the hot water
temperature to the set value. The hot water tem-
perature can be changed within the following limits:
Minimum: 20 °C
Maximum: 90 °C
Factory setting: 50 °C
Operation
√
Para
flashes.
1.
Press "SET". The domestic hot water target
temperature is displayed, the corresponding
component in the system diagram flashes
2.
Press "SET". The temperature value flashes.
3.
Press "
r
s
" to change the value.
4.
Press "SET", the change is applied.
Fig. 9: Set the domestic hot water target tempera-
ture
Switch on thermal disinfection
Method of operation
If required, the fresh water module provides higher
domestic hot water temperatures, in order to kill
dangerous germs. At the same time, the circulation
pump is activated, as long as the circulation func-
tion was activated. If the circulation function was
not activated, only the domestic hot water target
temperature is increased to the disinfection tem-
perature. Thermal disinfection is started via the
setting menu. After a manual start, thermal disin-
fection must be stopped again manually. For safety
reasons, thermal disinfection is deactivated after
one hour of running time if it was started manually.
Detailed settings for thermal disinfection must be
made in the corresponding function (F:08), see
‘Thermal disinfection’ on page 22
.
In cascade operation, the master controller
releases both modules during the disinfection
period.
Operation
√ The "Thermal disinfection (F:08)" function was
activated, see the "Thermal disinfection" section.
Otherwise, "---" is displayed. √
Legio
flashes.
1.
"StArt" is displayed.
2.
Press "SET". "oFF" is displayed.
3.
Press "SET". "oFF" flashes.
4.
Press "
rs
". "on" and
Legio
flash.
5.
Press "SET". The changes are applied.
Legio
flashes. The controller remains in the
Legio menu until thermal disinfection is deac-
tivated manually.
Reset to factory setting
√ flashes, "RESEt" is displayed.
1.
Press "SET" for 5 seconds.
2.
After a short running display, the controller
switches to "Automatic" operating mode.
4.4 Functions
General information for operating the functions
Display functions
When displaying the functions, the following infor-
mation is visible:
REMKO fresh water station Controller
16
Summary of Contents for EFS 25
Page 35: ......