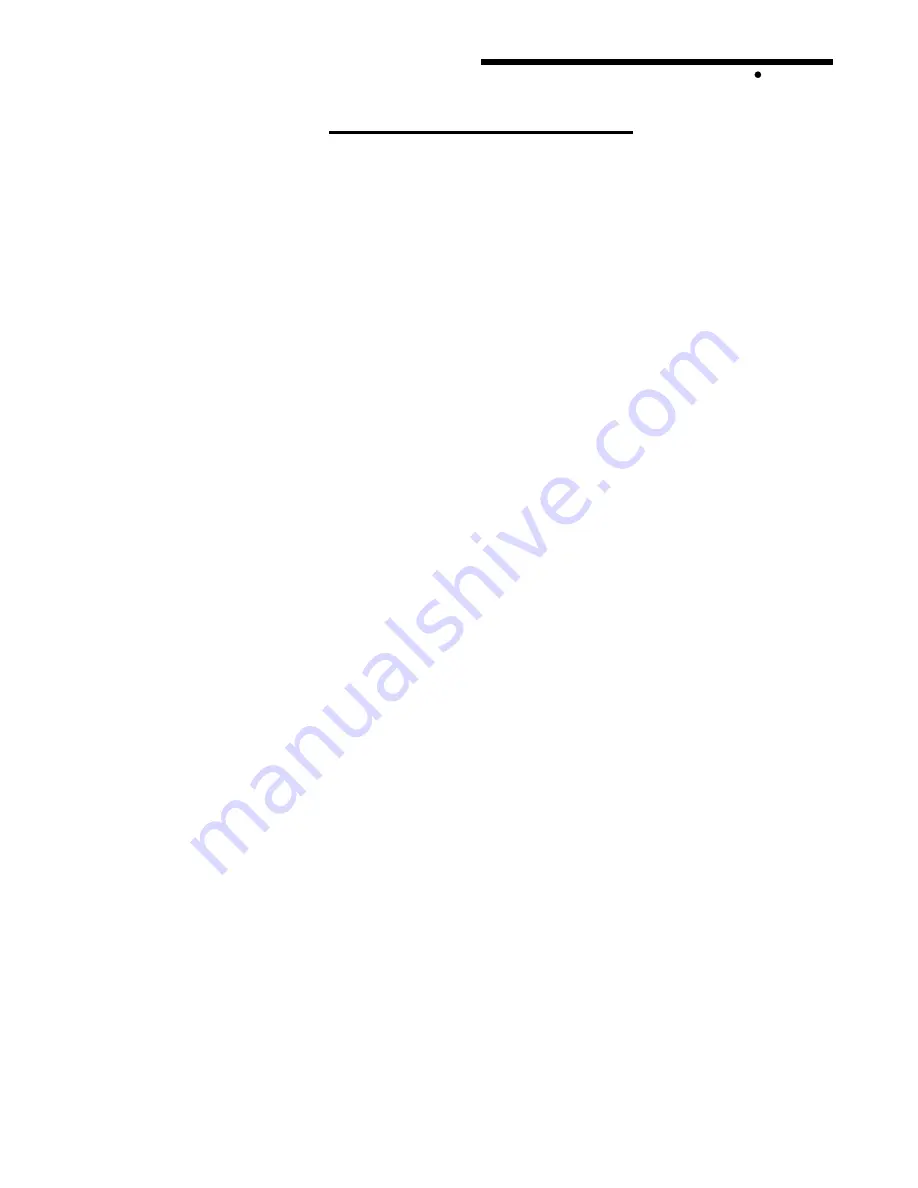
PARTS LISTINGS & SCHEMATICS PAGE 55
LOWER UNIT - 3KR1 ENGINE
ITEM
PART NUMBER
DESCRIPTION
QTY
1 30344000
BASE FRAME 3KR1
1
2 30601000
BEATER DRUM
1
3 30501000
BLOWER HOUSING
1
4 30892040
SIDE PLATE BRACE ASSEMBLY
1
5 30341070
SHAFT BEARING SUPPORT
1
6 31651000
SHAFT BEARING GUARD
1
7 30101100
BOOM TRANSPORT BRACKET
1
8 HA7160.01
HAIRPIN COTTER
1
9 30801000
FEED TRAY ASSEMBLY - FOLDING
1
10 BA8802.01
BATTERY 12v GRP 24
1
11 31471010
BATTERY HOLD DOWN BRACKET
1
12 BA8808.01
BATTERY HOLD DOWN BOLT
2
13 FA1241.03
3/8-16 NYLON INSERT NUT
2
14 FA0320.03
3/8 COMMERCIAL FLATWASHER
2
15 BA8806.03
BATTERY CABLE 36-38 (+)
1
16 BA8850.01
BATTERY BOOT (RED)
1
17 BA8807.01
BATTERY GROUND STRAP
1
18 SI0901.05
SIGNAL HORN
1
19 EL2101.61
FOOT SWITCH
1
20 32512000
FUEL TANK KIT (DIESEL)
20.1 TA6036.00
TANK 12 GALLON
1
20.2 TA6036.01
TANK HOLD DOWN CABLE
2
20.3 FA1241.03
3/8-16 NYLON INSERT NUT
2
20.4 FA0330.03
3/8 SPLIT LOCKWASHER
2
20.5 HO7303.11
FUEL HOSE/FT
4
20.6 HO7301.81
RETURN HOSE/FT
4 .5
20.7 TA2010.12
FELT TAPE 1/8 x 1
1
21 31631010
PRECLEANER FOAM
1
22 EN3112.00
ISUZU 3KR1 SPEC #VA07
1
23 EN3107.09
MUFFLER
1
24 EX3055.28
EXHAUST CAP
1
25 30891030
EXHAUST ADAPTER
1
26 IN3601.00
HOUR METER
1
27 30892060
HOUR METER BRACKET
1
28
07845000
RADIATOR ENCLOSURE
1
29
07892030
RADIATOR DEBRIS SCREEN
1
30
07921020
SCREEN BRACKET
2
31 FA1112.06
¼-20 x 3/4 SHOULDER WING SCREW
4
32 FA1281.02
¼-20 BLIND NUT
4
33 30891050
RADIATOR ENCLOSURE BRACKET
1
34 30894040
RADIATOR ENCLOSURE MOUNT
2
35 30891060
INSTRUMENT PANEL BRACKET
1
OPT 31701000
ELECTRIC SHUTDOWN KIT
MANUAL 33000900
© REINCO INC. 1998
REVISED 3/98