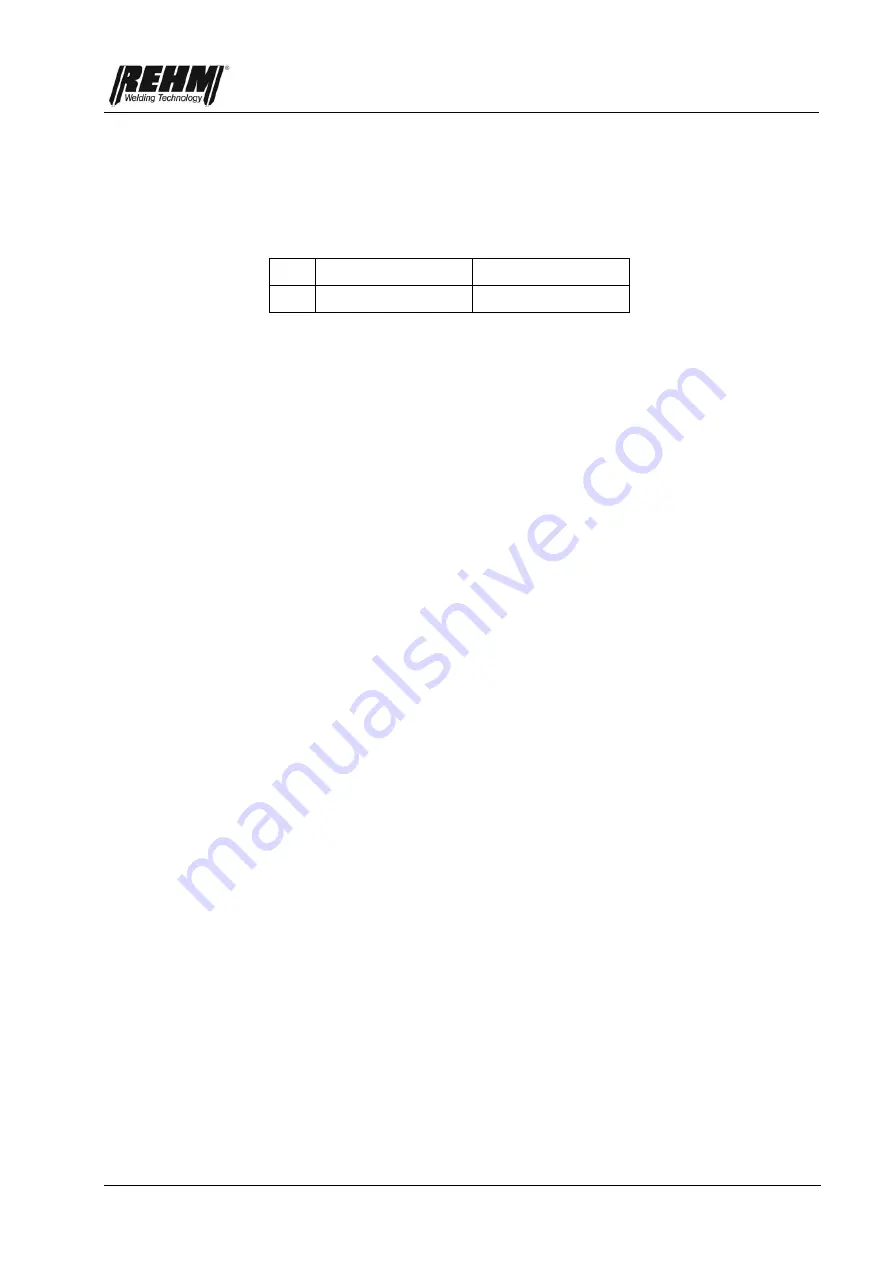
Functional description
18
3.7.1
Welding current with WIG welding
The machine model determines what welding current range can be adjusted.
Use the rotating button [5] to select the following values:
BOOSTER.PRO 250 BOOSTER.PRO 320
WIG
5 A … 250 A
5 A … 320 A
To start the welding process, a contact ignition (lift arc) is required. To ignite the
arc, put the electrode in place, and press the torch button. When the electrode is
lifted up, the arc is ignited as programmed and does not eat away the pointed
electrode.
With WIG welding, the arc burns freely between a tungsten electrode and the
work piece. The shielding gas used is an inert gas like Argon, Helium or a mix of
these. and is provided by a gas valve incorporated in the torch.
The WIG welding process is controlled with the 4-step function. This means no
permanent push button operation is necessary and the torch may be used for a
longer time without fatigue.
How the 4-step function works:
Open the main valve at the gas cylinder. Use the flow regulator and the pressure
reducer to adjust the gas flow. Open the gas valve at the torch and adjust the
flow desired. Place the WIG electrode onto the work piece. The contact is without
current, since there is no output voltage yet. This is in favour of the electrode and
the work piece.
1st Step: Press the torch button
The welding current has the value preselected for the starting current (starting
current = 50% of preselected welding current).
2nd Step: Release torch button.
The welding current adjusts automatically to the preselected value.
3rd Step: Press the torch button
The current drops to the end crater current value (end crater current =20% of the
adjusted welding current).
The welding current flows with the value selected for the end crater current.
4th Step: Release torch button.
The arc ceases. Close the gas valve at the torch when the desired gas post-
purge time is over.
Close the main valve of the gas cylinder again.
3.7.2
Option Gas management (#1480170)
The BOOSTER.PRO with gas management has a shielding gas shut-off valve
integrated in the welding unit. The REHM WIG torch controls the shielding gas
flow and the output voltage with the torch push button and the 4-step function.
This allows for an optimum gas shielding of the welding seam and efficient gas
consumption. This avoids rework and extra cost..
Summary of Contents for BOOSTER.PRO 250
Page 1: ...D BETRIEBSANLEITUNG OPERATING INSTRUCTION BOOSTER PRO 250 320 GB...
Page 6: ...Einleitung 6 1 2 Allgemeine Beschreibung Abb 1 BOOSTER PRO 320...
Page 31: ...Stromlaufplan 31 D 9 Stromlaufplan...
Page 34: ...Bauteile 34 Abb 3 Explosionszeichnung BOOSTER PRO 250 320 rechts...
Page 35: ...Bauteile 35 D Abb 4 Explosionszeichnung BOOSTER PRO 250 320 links...
Page 44: ...Introduction 6 1 2 General description Fig 1 BOOSTER PRO 320...
Page 69: ...Circuit diagram 31 GB 10 Circuit diagram...
Page 72: ...Components 34 Fig 3 Exploded view BOOSTER PRO 250 320 right hand side...
Page 73: ...Components 35 GB Fig 4 Exploded view BOOSTER PRO 250 320 left hand side...