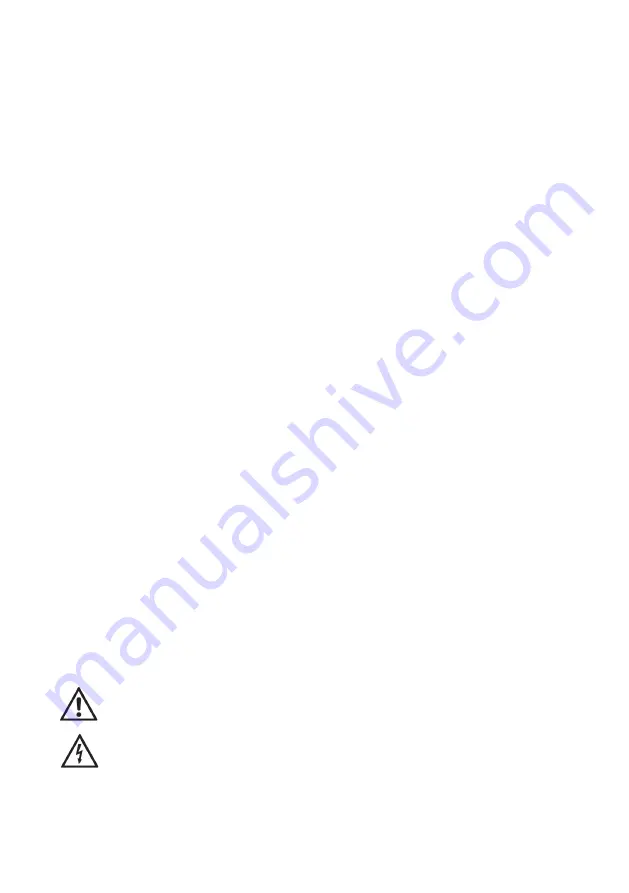
Symbols and sign at the welding machine or system
Attention - danger or damage
Attention - high voltage
Disregarding might cause injure or dead.
Personal protective equipment (PPE)
Personal protective equipment (PPE) is mandatory when working with a welding
system:
• Welding protection filter, protection level 10-15
• Protective shield, screen or hood
• Welding gloves
• Leather apron
The company is obliged to provide the operator with the necessary PPE.
Intended Use
The MIG / MAG welding systems are only to be used
• for MIG / MAG or manual electrode welding for hand-guided and machine-guided
operation (see original operating instructions)
• for welding metallic materials (such as steels, copper, titanium and aluminum)
• in a perfectly safe condition
Environmental conditions
• Temperature range of the ambient air:
- In operation: -10 ° C to + 40 ° C (14 ° F to 104 ° F)
- During transport and storage: -20 ° C to + 55 ° C (-4 ° F to 131 ° F)
• Relative humidity
- up to 50% at 40 ° C (104 ° F)
- up to 90% at 20 ° C (68 ° F)
• Ambient air:
Summary of Contents for 1307045
Page 27: ......