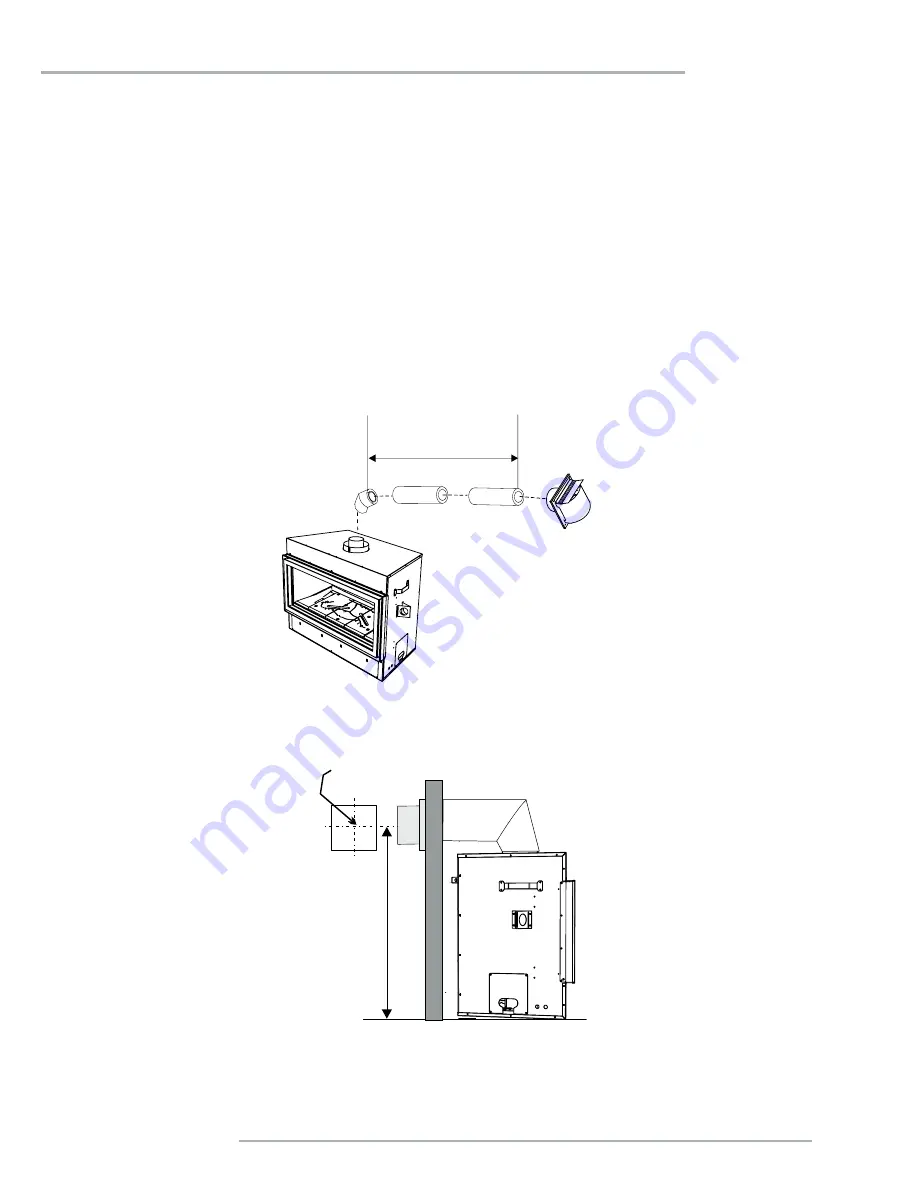
Regency GF900L-1 Gas Fireplace
21
installation
Maximum (0.8m)
Minimum (0.3m)
Straight Out Horizontal Venting
Diagram 1
Please note the minimum centerline for
basic install shown above.
HORIZONTAL TERMINATIONS
RIGID PIPE 4" X 6-5/8
" (
102MM X 175MM)
The diagrams below shows examples of horizontal termination arrangements using one 90
o
elbow.
1) A maximum of one 90
o
elbow is permitted.
2) Minimum distance between elbows is 1 ft. (305mm).
• Maintain clearances to combustibles as listed in the "Clearances" section.
• Horizontal vent must be supported every 3 feet.
• Firestops are required at each floor level and whenever passing through a wall.
• Must use optional rigid pipe adaptor (Part# 510-994) when using rigid pipe vent systems.
• A vent guard should be used whenever the termination is lower than the specified minimum or as per local codes.
• Flex system can only be used up to 3m - otherwise rigid venting must be used.
CL
CL
Min. height
(Rigid)
3
9" (991mm)
center
of hole