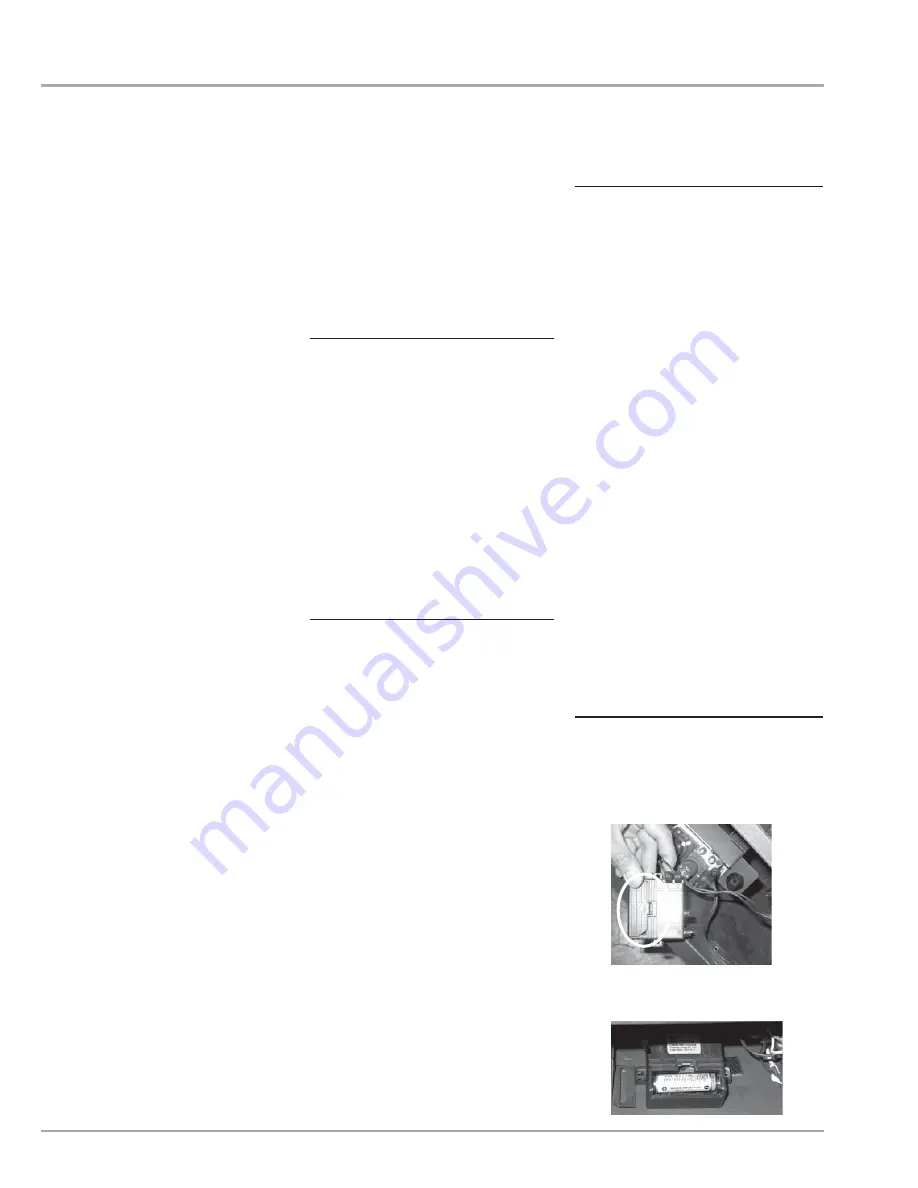
57
Regency Bellavista™ B41XT Gas Fireplace
MAINTENANCE
3)
Check for evidences of excessive
condensation, such as water droplets forming
in the inner liner, and subsequently dripping
out the joints, Continuous condensation can
cause corrosion of caps, pipe, and fi ttings.
It may be caused by having excessive
lateral runs, too many elbows, and exterior
portions of the system being exposed to
cold weather.
4)
Inspect joints, to verify that no pipe
sections or fi ttings have been disturbed,
and consequently loosened. Also check
mechanical supports such as Wall Straps,
or plumbers' tape for rigidity.
LOG REPLACEMENT
The unit should never be used with broken logs.
Turn off the gas valve and allow the unit to cool
before opening door and carefully remove the
logs. (The pilot light generates enough heat to
burn someone.) If for any reason a log should
need replacement, you must use the proper
replacement log. The position of these logs
must be as shown in the diagrams under Log
Installation.
Note: Improper positioning of logs may
create carbon build-up and will
severely alter the unit's performance
which is not covered under
warranty.
THERMOPILE /
THERMOCOUPLE
1) Open the Bottom Louvers or Grills. Remove
the Top Louver or Grill.
2) Remove the Trim Kit, Glass Door, Log
Set, Grate and Burner Assembly (see the
"Log Installation" & "Glass Door Removal"
sections).
3) Disconnect thermocouple by loosening
nut from the valve with a 9mm wrench.
Disconnect thermopile by loosening 2
screws marked TP on the valve.
4) Remove 2 screws from the pilot assembly
and pull up far enough to be able to loosen
the thermocouple or thermopile with a 7/16"
wrench. NOTE: the pilot line is very fragile,
use caution when pulling it up.
5) Drop the thermocouple or thermopile down
through the extrusion and pull it out of the
unit.
6) Reinstall the new ones in reverse order.
GLASS GASKET
If the glass gasket requires replacement use a
tadpole glass gasket (Part # 936-155).
DOOR GLASS
Your Regency
®
fi replace is supplied with high
temperature 5mm-Ceramic glass. If your glass
requires cleaning, we recommend using an
approved glass cleaner available at all authorized
dealers. Do not use abrasive materials.
CAUTION & WARNINGS:
* Do not clean when the glass is hot.
* The use of substitute glass will void all
product warranties.
* Care must be taken to avoid breakage of
the glass.
* Do not strike or abuse the glass.
* Do not operate this fi replace without the
glass front or with a cracked or broken
glass front.
* Wear gloves when removing damaged or
broken glass.
* Replacement of the glass panels should be
done by a licensed or qualifi ed service per
son.
GLASS REPLACEMENT
In the event that you break your glass by impact,
purchase your replacement from an authorized
Regency dealer only. Replacement glass (Part
#940-362/P) is shipped already installed into
the door frame. Reinstall as per Glass Door
Installation in the "Glass Door Removal" section.
MAINTENANCE
INSTRUCTIONS
1)
Always turn off the gas valve before cleaning.
For relighting, refer to lighting instructions.
Keep the burner and control compartment
clean by brushing and vacuuming at least
once a year. When cleaning the logs, use a
soft clean paint brush as the logs are fragile
and easily damaged.
2)
Clean appliance and door with a damp
cloth (never when unit is hot). Never use
an abrasive cleaner. The glass should be
cleaned with a gas fi replace glass cleaner.
The glass should be cleaned when it starts
looking cloudy.
3)
The heater is fi nished in a heat resistant
paint and should only be refi nished with heat
resistant paint. Regency
®
uses StoveBright
Paint - Metallic Black #6309.
4)
Make a periodic check of burner for proper
position and condition. Visually check the
fl ame of the burner periodically, making sure
the fl ames are steady; not lifting or fl oating.
If there is a problem, call a qualifi ed service
person.
5)
The appliance and venting system must be
inspected before use, and at least annually,
by a qualifi ed fi eld service person, to ensure
that the fl ow of combustion and ventilation
air is not obstructed.
Note: Never operate the appliance without
the glass properly secured in place.
6)
Do not use this appliance if any part has been
under water. Immediately call a qualifi ed
service technician to inspect the appliance
and to replace any part of the control system
and any gas control which has been under
water.
7)
In the event this appliance has been serviced
check that the vent-air system has been
properly resealed & reinstalled in accordance
with the manufacturer's instructions.
8)
Verify operation after servicing.
General Vent Maintenance
Conduct an inspection of the venting system
semi-annually. Recommended areas to inspect
as follows:
1)
Check the Venting System for corrosion in
areas that are exposed to the elements. These
will appear as rust spots or streaks, and in
extreme cases, holes. These components
should be replaced immediately.
2)
Remove the Cap, and shine a fl ashlight down
the Vent. Remove any bird nests, or other
foreign material.
DC SPARKER BATTERY
REPLACEMENT
1)
Remove the battery cover from the DC
Sparker - remove the AA battery.
2)
Replace with a new 'AA' battery and reinstall
battery cover.