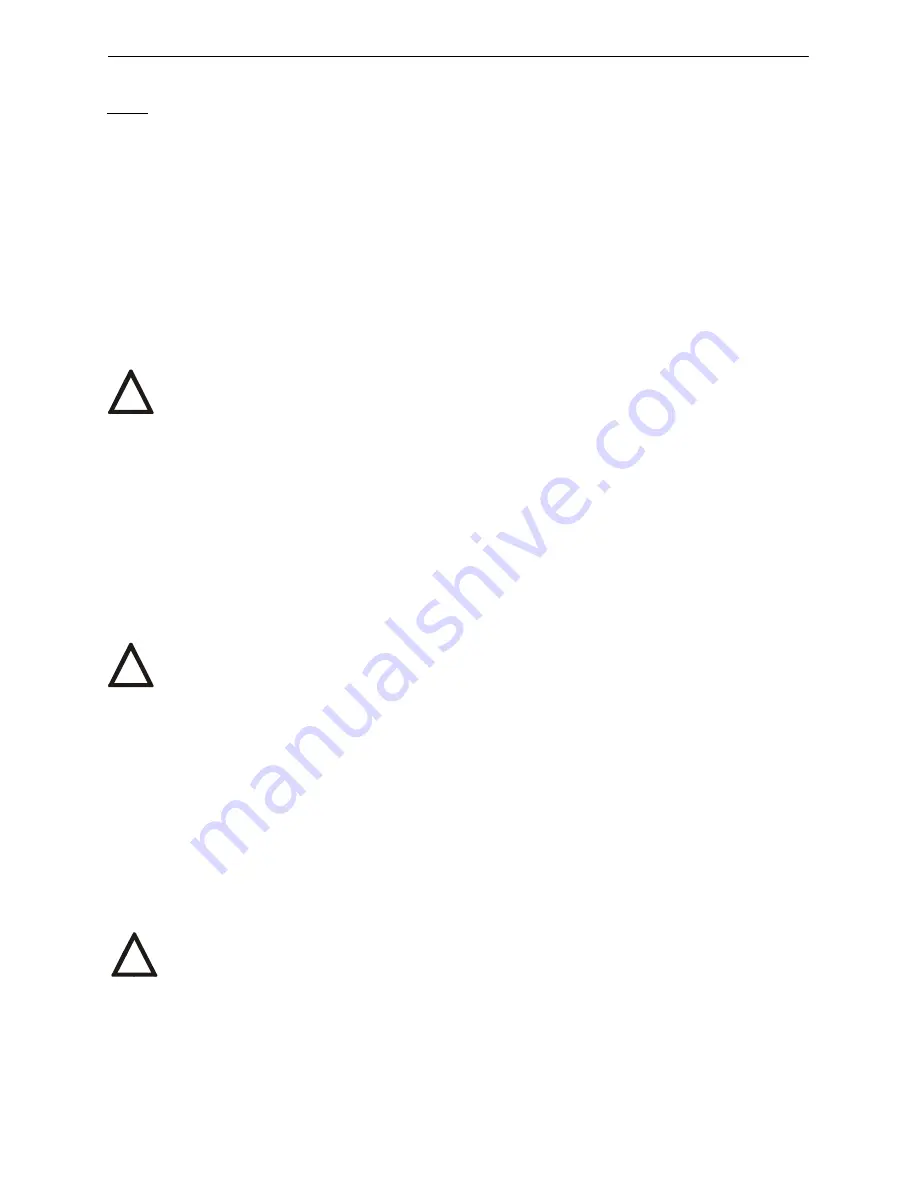
SP 1, SP 2, SP 2.3, SP 2.4
15
SPR1, SPR 2, SPR 2.3, SPR 2.4
Notes:
1. The EA are delivered with cable glands, which in case of tight putting on the leads assure protection
enclosure up to IP 68. For required protection enclosure it is needed to use rings according to the actual
cable diameter.
2. While fixing the cable it is needed to count with allowed bend radius to avoid damaging or deformation of the
sealing element of the bushing. The leads are to be fixed with the solid construction at most 150 mm from
the cable glands.
3. It is recommended to use screened cables to connect remote transmitters.
4. The face areas of the control part cover have to be before re-mounting clean, coated with a grease without
any acid (e.g. vaseline) and sealing not damaged to avoid joint corrosion.
5. Reversation of the EA is sure, if the period between switching-off and switching-on of power supply for the
reversed movement of the output part is minimally 50 ms.
6. Delay after switching-off, i.e. time since a reaction of switches till the motor is dead can be maximally 20 ms.
7. It is recommended to have the corresponding direction protection switched-off directly with the
corresponding position or torque switches.
Abide by instructions of valve producers, whether switching-off in limit positions is to be
realised with position or torque switches.
After electric connection perform checking of function:
•
Put the valve manually to a mid-position.
•
Connect the EA electrically for the chosen direction of movement and watch the output part movement.
•
If it does not correspond change the order of feeding phases (valid for 3x400V version), or change leads of
the feeding phase to the corresponding terminals (valid for 230V version).
•
Check the control unit switches connection with switching consequently the contacts of the corresponding
switches by pressing the control elements during running of the EA (at proper connection) to the chosen
direction. In case of proper connection the EA stops or indicates the adjusted position according to switching
of the chosen switch. If any of the functions is fault check connecting of the switches according to wiring
diagrams.
In the
SPR version
with the built-in electronic controller it is needed to perform
autocalibration
for
assuring optimal functioning.
The procedure is as follows
Press the button
SW1
for about 2 sec (i.e. till the
D3
diode is got on) to set the controller to the
autocalibration
mode. During this process the controller checks the feedback transmitter and the sense of
turning, puts the EA to the positions open and closed, measures inertia mass in the directions "opening" and
"closing", and loads the adjusted parameters into the EEPROM memory. In case that during the initialization
process an error occurs (e.g. in connection or adjustment) the initialization process will be interrupted and the
controller with the
D4
diode reports about the type of the error. Else after finishing the initialization process the
controller is put into the
regulation mode
. If needed to change adjusted parameters of the controller follow
instructions given in the part Adjusting of actuator.
3.2 Dismantling
Before dismantling it is required to disconnect the EA from mains!
Do not connect and disconnect live connectors!
•
Disconnect the EA from mains.
•
Disconnect the leads from the EA terminal boards and loosen the cables from cable glands. Pull out the
connectors in case of the connector version.
•
Loosen the fixing screws of the EA flange and disconnect the EA from the valve/gearing.
•
While sending the EA to be repaired put it into a package solid enough to avoid damages of the EA during
transportation.
!
!
!