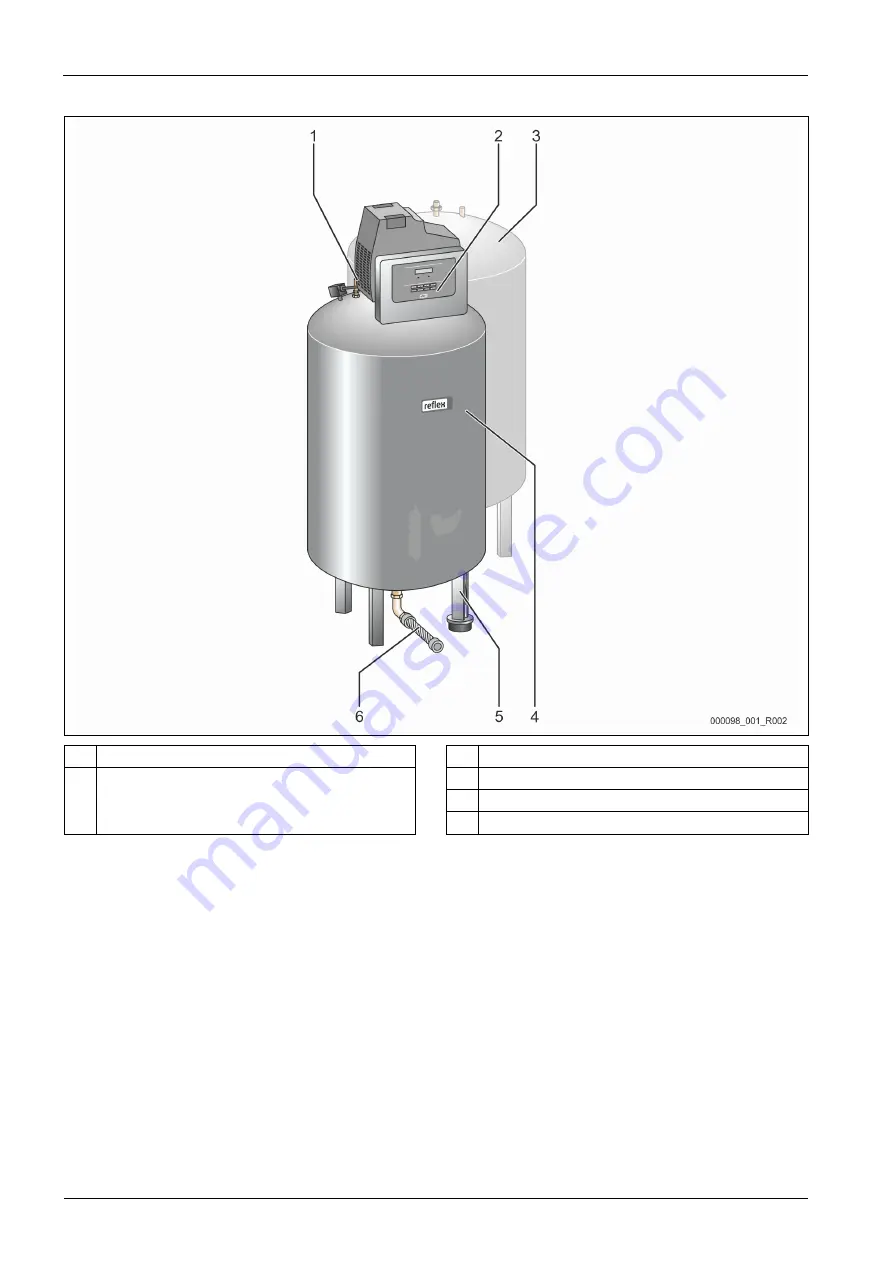
Description of the device
10 — English
Reflexomat with Basic controller — 20.06.2017 - Rev. C
Reflexomat RS 90 / 1 in compact design
1
"SV" safety valve
3
"RF" secondary tank (optional)
2
"RS 90 / 1" control unit
•
Compressor
•
"Reflex Control Basic" controller
4
"RG" primary tank
5
"LIS" level sensor
6
"EC" expansion line
Summary of Contents for Refexomat RSC
Page 5: ...11 ARTIKELIDENTITETER RSK nummer Eget Artikel nr GTIN AT 8300 Sida 5...
Page 11: ......
Page 67: ......
Page 68: ......