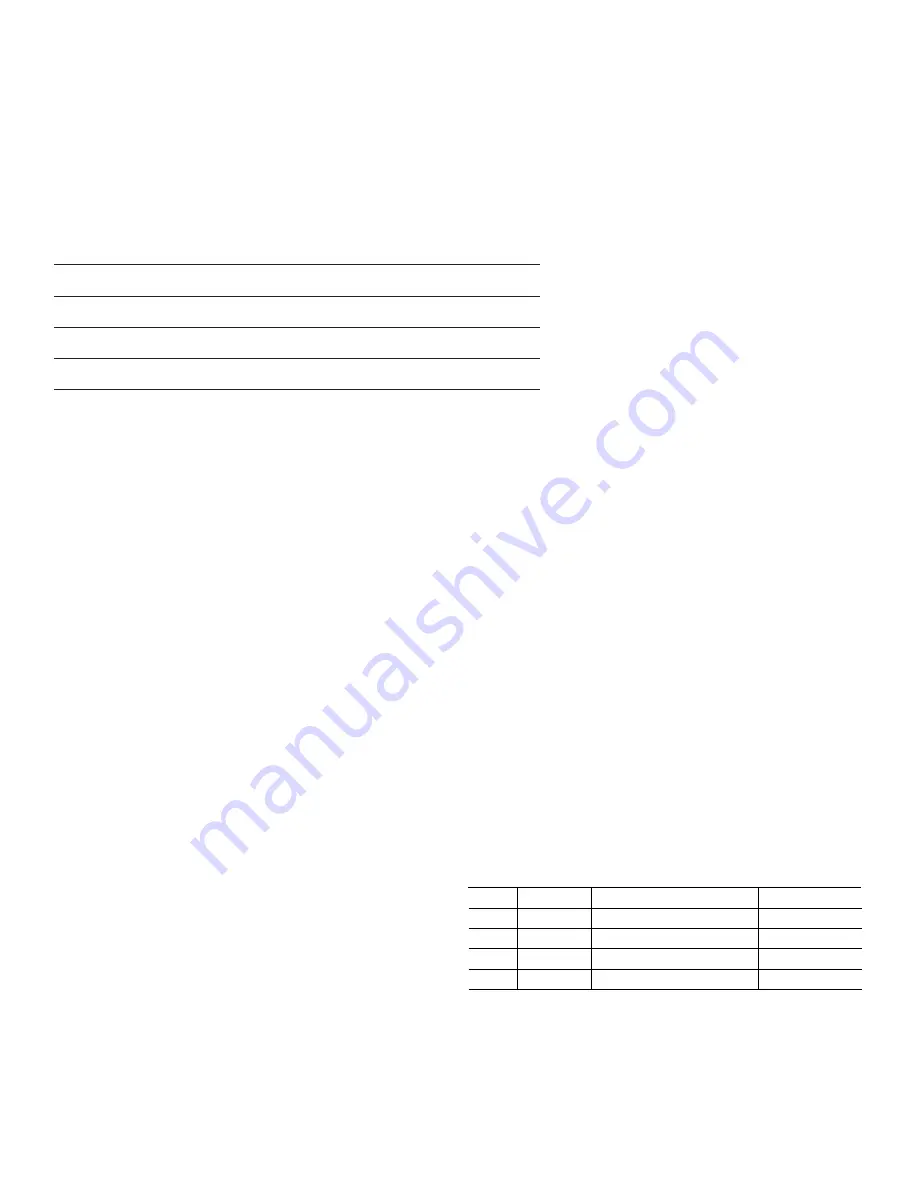
2
The Reed Rotary™ Cutter is a very efficient tool for cutting many
different sizes of cast iron, ductile iron, and steel pipe, from 20" to
36". In most cases, the Rotary™ Cutter is a one person tool.
Fig. 1
Cutter Wheel Reference Chart for Rotary™ Cutters
For best results and efficient operation, these instruc-
tions should be followed carefully:
1.
Determine the best type of cutter wheel to use for the pipe to be
cut by referencing Fig. 1.
2.
To change the cutter wheels, lay the Rotary™ Cutter on its side,
with the head of the wheel pin head pointing down. Next, lightly
tap the end of all wheel pins facing up, allowing them to drop out
far enough to enable the removal of the wheel pin. Prior to re-
moving the wheel pin completely, flip the Rotary™ Cutter over
and then remove each wheel pin. Line up the cutter wheels and
outboard roller and push the wheel pins back into the hole. Next,
seat the wheel pin into place with a light tap and repeat this
proceedure for all of the wheel pins.
3.
To set up for making a cut, loosen the nuts on the main screws
just enough to permit the cutter frame to slide over the end of
the pipe. (The main screws can also be slipped out of the frame
slot to permit the cutter to open and be placed around the pipe.
Re-engage the main screw with the frame slot to close the
cutter frame.)
4.
Position the cutter so the cutter wheels are in line with the cutoff
mark. Rotate the cutter until the weight of it is resting on the
spring-loaded guide fingers in the top half of the cutter frame. All
cutter wheels should at this time be away from the pipe, and the
arrow on the frame point in the direction of desired rotation.
5.
Slightly rock and wiggle the cutter until all four of the guide
fingers touch the pipe. This rocking motion makes the cutter sit
square on the pipe.
6.
Next, without disturbing the cutter position, tighten up the main
screw nuts EQUALLY by hand. Usually the two bottom wheels
will contact the pipe first. Continue tightening as the spring-loaded
guide fingers retract and permit the top wheels to contact the
pipe. Using the lug wrench on the operating handle, tighten the
one accessible nut as tight as possible while still being able to
rotate the cutter.
7.
Slipping the lug wrench over the most conveniently accessible
lug, rotate the cutter, one lug at a time in the direction of the
arrow, until the other nut is in position to be tightened. Recheck
the location of the cut and that the cutter is tracking properly.
Item
Reed
Std.
Blade Exposure
Code
Cat. No. Pkg.
Reed Cutter
Inches MM
Application
03530
RCS8-36
4
LCRC8; LCRC12; LCRC16; RC20;
0.635
16.1
Steel; Stainless Steel
RC24; RC30; RC36
03535
RCI8-30
4
LCRC8; LCRC12; LCRC16; RC20;
0.500
12.7
Cast Iron; Ductile Iron (manual)
RC24; RC30; RC36
03545
RCDX
4
LCRC8; LCRC12; LCRC16; RC20;
0.531
13.5
Heavy Cast Iron; Ductile Iron (PRC)
RC24; RC30; RC36
03550
RCX
4
LCRC8; LCRC12; LCRC16; RC20;
0.800
20.3
Heavy Wall Steel; Stainless Steel
RC24; RC30; RC36
Operating Instructions
8.
To complete the cut from this point, keep rotating the cutter and
at every half revolution, tighten each main screw nut one
quarter to one half turn. (For the RC30 or RC36, it may be
advisable to have two workers: one person to tighten the nuts
and one to rotate the cutter.) It is important to complete the
cut without pausing and to maintain consistent pressure.
9.
Steel pipe must be cut all the way through the wall. Cast iron
pipe, depending on age and hardness, will snap off clean and
true after about one-fourth of the wall has been penetrated.
Ductile iron, being very tough, usually snaps off after one-third
to one-half the wall has been penetrated.
10. When cutting cast iron pipe, after hearing the first
snap or crack in the pipe, continue tightening the
nuts to maintain maximum pressure on the pipe
until complete cutoff occurs. If a support can be
maintained on the pipe while cutting, such as with
a crane, hydraulic jack, etc., it will often cut the
operation time in half by inducing the fracture to
occur sooner and to run clear around the pipe
instead of part way.
11. When cutting into a section of cast iron pipe, that has been
buried in the ground for a long time, the line may be under com-
pression from various causes and the slightly jagged fracture of
the cuts may resist lifting the cut piece out. One way around this
difficulty is to make three cuts instead of two. Make a third cut
about 2
1
/
2
” inside one of the end cuts. A sledge hammer will
break out the two and a half inch section and then the bigger
piece will lift out easily. When cutting cast pipe under compres-
sion, the cutter must be fed and rotated until all outboard rollers
are in contact with the pipe, to be sure of complete fracture.
12. The cutter is designed not to break under cutting loads. The
handle will bend first.
13. Certain brands of ductile iron pipe are softer than others and
lend themselves to faster and easier cutting with RCS8-30
cutter wheels for steel pipe. If cutter wheel breakage is not
excessive, the substantial time and labor savings may very well
justify this.
BADLY CRUSTED AND RUST SCALED PIPE: Remove the rust
and scale from the area to be cut with a Reed Descaler (Fig. 2). A
hammer and chisel or coarse file may also be used. This will help
save cutter wheels and cutting time; and helps to square the cutter
on the pipe to ensure tracking.
Fig. 2
PIPE DESCALERS
Cat. No.
Item Code Pipe Capacity
Length
DS12
08000
3 - 12 in
70 - 300 mm
32 in
810 mm
DS36
08006
3 - 36 in
70 - 910 mm
44 in
1110 mm
DS12B
08008
3 - 12 in
70 - 300 mm
45 in
1143 mm
DS36B
08010
12 - 36 in
300 - 910 mm
72 in
1829 mm