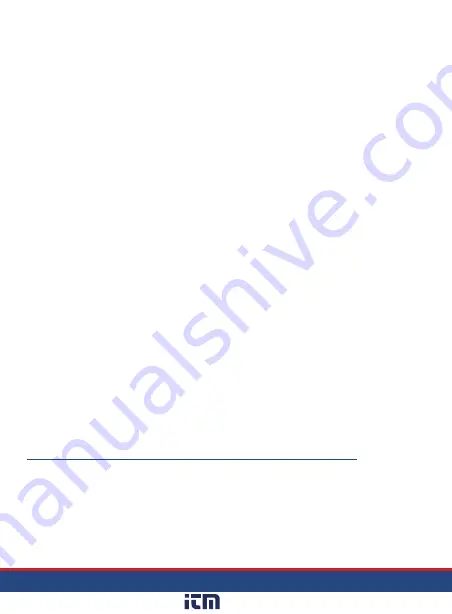
19
Influence of Material's Temperature
Both the thickness and transmitting speed of ultrasonic waves are
influenced by temperature. If there is a high requirement of measuring
accuracy, please use one of the comparison methods listed below:
1. Use a test piece of the same material being measured, under the
same temperature.
2. Obtain the temperature compensation coefficient.
3. Use this coefficient to correct the actual measurement of the material
being tested.
Material with Large Attenuation
Material with porous and coarse particles (such as fibre) will cause a large
scatter and energy attenuation in the ultrasonic wave. This will cause
abnormal readings or provide no readings on the display (generally, the
abnormal readings are less than the actual thickness). These type of
materials cannot be measured by our ultrasonic thickness gauges.
Measuring Castings
Castings will cause large attenuations in sound energy due to coarse
crystal particles and a not-so-dense structure. The attenuation is due to
the material's scatter and absorption of sound energy. Coarse out-phase
structures and coarse crystal particles will cause abnormal reflection (i.e.
a grass-shaped or tree-shaped echo) resulting in errors in the readings.
When the crystal particle is coarse, the anisotropy in flexibility in metal's
crystallizing direction will be obvious. This results in difference in sound
velocities in different directions, with the maximum difference being up to
5.5%. The compactness in different positions of the workpiece is different,
which will also cause difference in sound velocity. All of these will produce
inaccuracies in the measurements.
While measuring castings pay attention to the following:
1. When measuring casting with an un-machined surface use engine
oil, consistent grease, or water glass as a coupling gel.
2. Calibrate the sound velocity for the material under test with a
standard test piece having the same material and measuring
direction as that of the material being measured.
3. If necessary, take a 2-point calibration.
continued...
www.
.com
1.800.561.8187