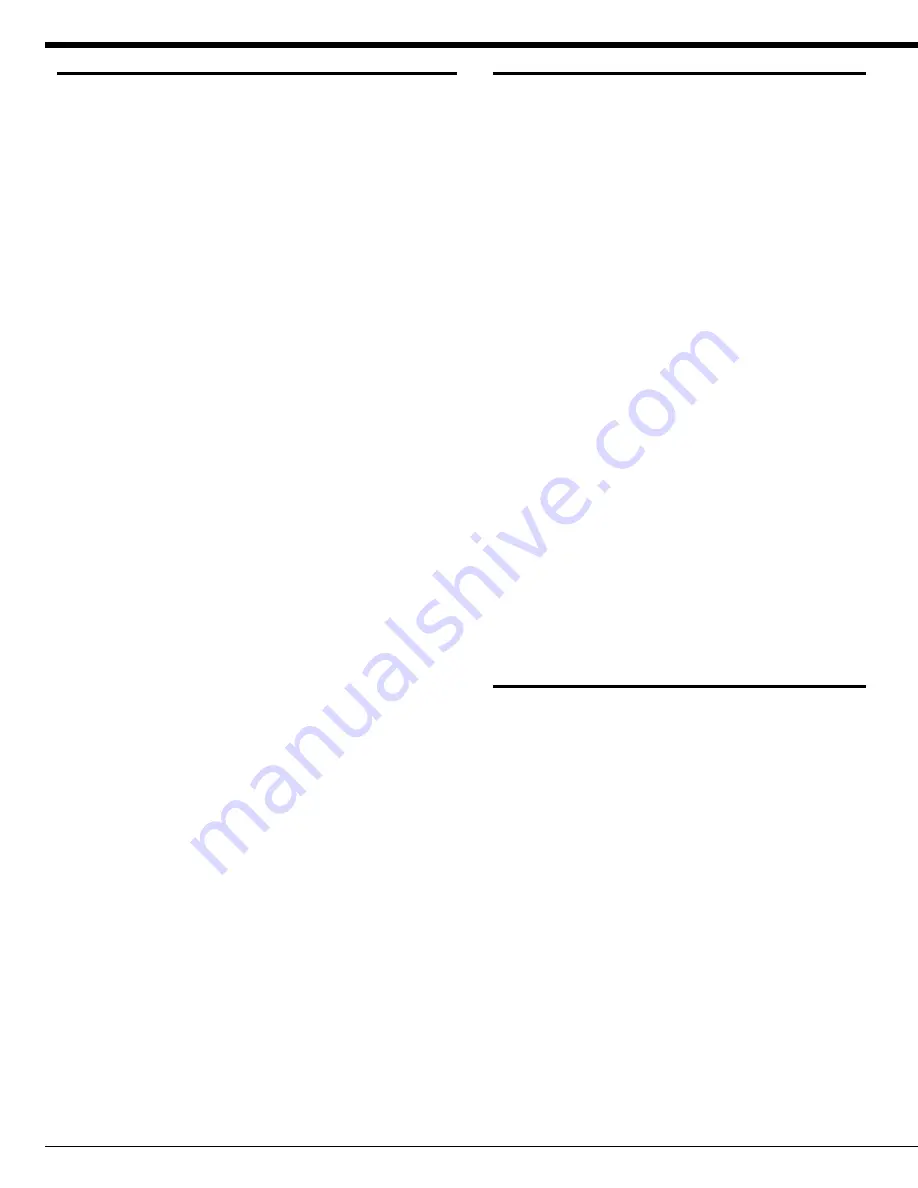
INSTALLATION
1.
Red Valves have flanges that mate with standard 125#
ANSI flanges which are also equivalent to 150# flange
dimensions. Due to clearances, the valves have tapped
holes, not through bolts.
WARNING
: Do not use bolts that
are too long. They will bottom out and may crack the valve
body. Stud bolts are recommended, and be sure to tighten
bolts in a ìstarî pattern, not sequentially around the flange.
2.
The flanges mating to the Series 5400 should be serrated,
approximately 1/16" x 90
°
. Rubber will creep along smooth
glass, PVC, or Teflon flanges, eventually causing a flange leak.
Flange I.D. should match sleeve I.D. and should be free of
sharp edges which could cut into the sleeve. Weld-neck or
socket flanges are recommended. Slip-on or screw-on
flanges have a larger I.D. and can cut into the rubber. If slip-on
or screw-on must be used, grind off all sharp I.D. edges.
3.
Do no use sharp tools such as screwdrivers or crowbars on
the rubber for installation. This can damage the face flange
and cause possible leakage.
4.
The valve should be completely open before installing the
valve in the pipeline or tightening flange bolts. Valves with
Fail-Closed spring-return cylinders are shipped with the lower
portion pressurized to keep the valve open during shipment,
storage, and installation. See the supplementary sheet on
installing valves with fail-closed cylinders for more information.
For valves with stem seals and body gaskets,
remove the drain plug in the bottom of the casting
before operating valve.
5.
Tighten all flange bolts to values listed in the table on the
back page. You will not overtorque the flange rubber.
6.
Pneumatic and hydraulic actuators are sized based upon
the line pressure and operating pressure at the installation
site. Changing the location of the valve may result in insuffi-
cient pressure to fully close the valve, or if the valve has a
fail close spring, it may not fully open. Be sure to refer to the
positioner manufacturerís IOM for proper air line connec-
tions. Connecting plant air to the instrument air port can
result in severe damage.
7.
For pneumatic valves, a pressure reducing valve and
integral gauge should be placed on the air supply line and
also on the instrument air supply line. This will prevent
accidental damage to the unit from overpressures or surges.
8.
Electrically operated valves are sized based upon the line
pressure and electrical supply available at the installation
site. Only qualified personnel should handle the electrical
connections. Be sure to refer to the actuator manufacturerís
IOM for proper safety precautions. Reversing positive-
negative connections, or connecting the wrong phase power
supply can lead to severe damage.
OPERATION
1.
All units are bench tested before shipping. Calibration
and stroke adjustment may change during shipment. An
operational test is recommended before installing the unit
into the line.
2.
If flanges leak during initial operation, the holes in the
sleeve may be out of line. Open the valve fully, loosen all
flange bolts, stroke the valve half-closed, re-open, and re-
tighten the flange bolts a second time.
3.
For both on-off and modulating valves, be certain that
the sleeve is not slightly cracked open in the fully closed
position. Operating the valve in the cracked position can
shorten sleeve life, since flow velocities are very high
under these conditions. If the valve does not close
completely, it should be adjusted.
For electrically operated valves, the stroke limits and/or
torque limits can be increased to gain additional stroke.
Check the manufacturers operating instructions. For all
valves, the lower pinch bar can be raised slightly to shorten
the stroke.
A.
With the valve open, remove both Side Rod Pins (6).
B.
Close the valve to clear the Scissor Plates (3).
C.
Turn each Side Rod clockwise 1-1/2 revolutions.
D.
Both bars must be turned the same number of times.
E.
Open the valve and reinstall Side Rod Pins (6).
MAINTENANCE
Valves should be inspected, actuated, and lubricated
every 90 days. If the valve is operated under severe
environmental conditions, (eg. high vibration, abrasive
dust, frequent washdown, etc.) the frequency of inspec-
tion, actuation, and lubrication should be increased as
appropriate. Visually examine the operating mechanism
for damage, loose parts or signs of excessive wear.
WARNING: Make sure there is no pressure in
the line before adjusting, tightening, or replac-
ing any parts.
Tighten any close parts. Replace any
parts that are damaged or exhibit excessive wear. Lubri-
cate the operating mechanism, side rods, and stem in
the fully closed position using a high quality Lithium based
grease (Mobil Mobilith AW 1 or equivilent). Lubrication is
required at every pivot point on the operating mechanism,
the side rods, and stem. This includes pins, scissor plates,
and the brass bearing blocks. Open the valve and lubri-
cate the operating mechanism, stem, and side rods in the
fully open position. Cycle the valve to the full closed posi-
tion and back to the full open position to distribute the
grease throughout the mechanism.
Page 4 of 8