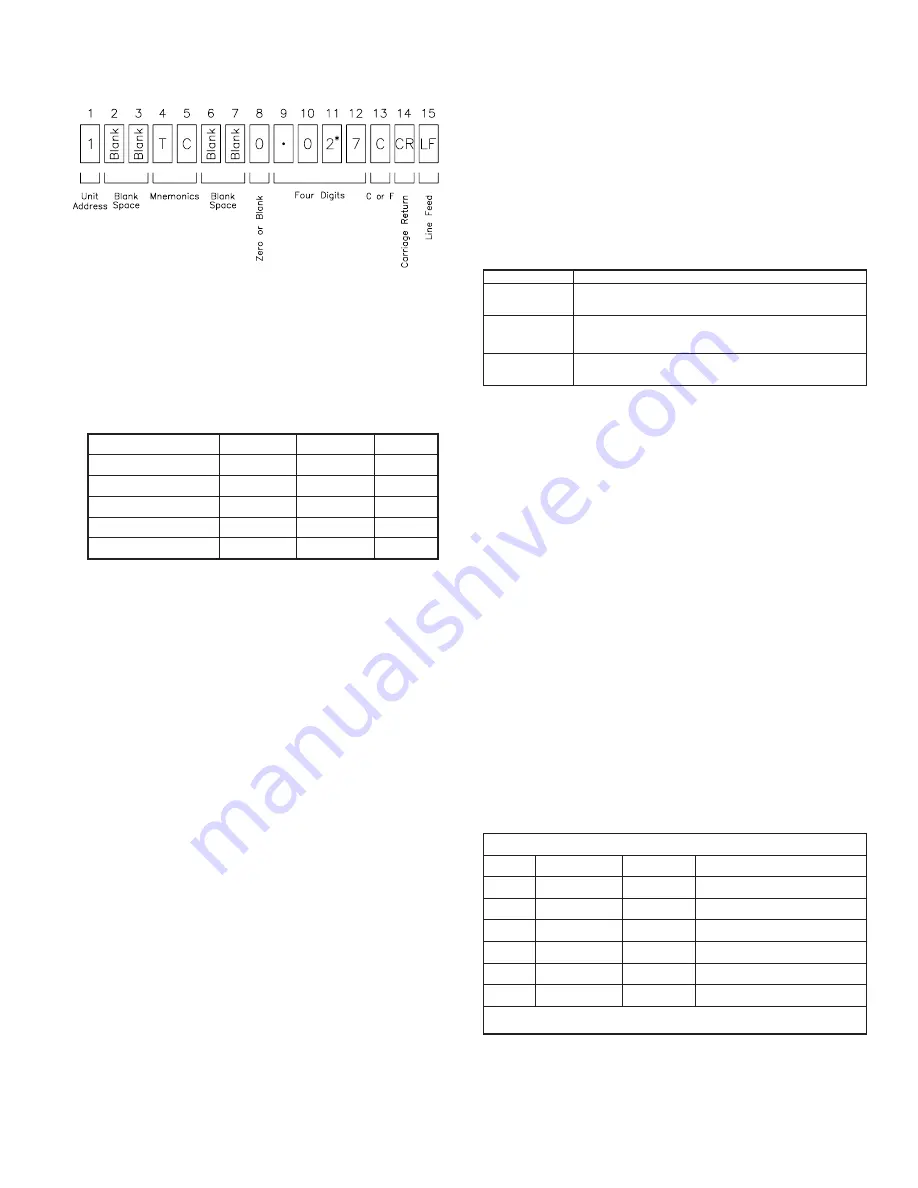
For Sales and Support, Contact Walker EMD • Toll-free: (800) 876-4444 • Tel: (203) 426-7700 • Fax: (203) 426-7800 • www.walkeremd.com
5
RECEIVING DATA FROM THE APLTC
Data is transmitted from the Apollo whenever a T
(transmit command)
is
received or the hardware print request terminal is activated. The five possible
responses and a typical transmission is shown below.
The first character transmitted is the unit address number; unless it is zero, in
which case it will be left blank. Then two blank spaces. The next two characters
are the abbreviation for the values, followed by three blanks
(two for cold
junction).
The actual data values are transmitted next. The field is right justified
with leading zeros
(not blanks)
and negative values have a minus sign in
position 9. A plus sign for positive values is not used and note that the field for
cold junction has a decimal point. The message
“OPEN”
will appear in the data
field of the thermocouple temperature transmission whenever the indicator
senses a thermocouple break. After the data field, an F or C character is
transmitted depending on the indicator’s current units, followed by carriage
return and line feed.
SERIAL TERMINAL DESCRIPTION
Note: The numbers in parentheses refer to the position numbers labeled on the
terminal block.
SI+
(1) - Serial In (+):
Current flows into the Apollo’s receive channel.
SI-
(2) - Serial In (-):
Current flows out of the Apollo’s receive channel.
SO+
(3) - Serial Out (+):
Current flows into the Apollo’s transmit channel.
SO-
(4) - Serial Out (-):
Current flows out of the Apollo’s transmit channel.
20 mA- (5) - 20 mA current source for either receive or transmit loop current.
Current flows into this pin.
20 mA+(6) - 20 mA current source for either receive or transmit loop current.
Current flows out of this pin.
When wiring the 20 mA Serial Loop, remove the 6-position terminal block
on the right side of the bottom board. Strip 1/4" off each wire and connect each
wire into the proper location of the terminal block. Re-install the connector and
be sure that the wires are strain-relieved.
ANALOG OUTPUT OPTION
The Apollo Thermocouple Indicator Analog Output Option provides an
isolated 1mV/degree output to drive chart recorders, controllers, data loggers
and slave displays. The output corresponds to the displayed temperature and
increments in discrete steps. Although the option is calibrated at the factory,
user accessible zero and span adjustments are provided for minor adjustments.
These are located adjacent to the output connections. Recalibration is
recommended after 1 year of use.
The analog output option terminal block is located at the rear of the unit in
the upper right-hand corner. Terminal 4 is the VOLT+, and terminal 5 is the
VOLT-
(COMM.) (Note:The alarm COMM. terminal and the analog output
VOLT- terminal are internally connected.)
To check for accuracy, connect a voltmeter to the output and the reading should
be +1mV per degree of displayed reading
(+/- 6 degrees)
. If calibration should be
necessary, connect the indicator as shown in the set-up and calibration section.
1. Apply an arbitrary voltage so that the indicator displays a negative
temperature
(-100,-200, etc.)
. Adjust the zero potentiometer
(right side)
so
that the readings from the voltmeter and the indicator correspond.
2. Apply an arbitrary voltage so that the indicator displays a large positive
temperature
(+1500, +2000, etc.)
. Adjust the span potentiometer
(left side)
so that the reading from the voltmeter and the indicator correspond.
3. Repeat steps 1 and 2 until both points are correct. Calibration is complete.
TROUBLE SHOOTING
A functional test can be performed by connecting a wire jumper between the
thermocouple inputs. When power is applied, the display will briefly show
“888.8
8
” to test the LEDs and then indicate the cold junction temperature at the
rear of the unit. Verify that all display segments illuminate and the temperature
indicated is near ambient temperature. The indicator has several special display
modes which indicate faults within the meter or external connections. The table
illustrates these and the most common causes.
CALIBRATION
The Apollo thermocouple indicator has been calibrated at the factory using
precision instruments and was designed not to require frequent recalibration.
However, as part of a regular maintenance program or after 1 year of use,
recalibration by authorized personnel is recommended.
Recalibration consists of applying accurate voltages to the indicator and
setting the cold junction temperature with an accurate thermometer. A precision
thermometer (RTD, thermistor or similar type) (accuracy of ±0.3°C) and an
accurate voltage source (0.01%) are required.
Do not use thermocouple wire
when making connections.
Allow 30 minutes warm-up time before calibration is attempted.
If long thermocouple runs are present in the application
(>300 ft.),
significant
offset errors may exist due to the input bias current of the indicator. To correct
for this effect, insert a fixed resistance in series with the positive leg of the
millivolt source which is equal to the thermocouple wire resistance and proceed
with calibration as normal. In most thermocouple applications this error is
insignificant and may be ignored.
Following the procedure outlined in SET-UP and CALIBRATION, press the
buttons indicated in the following charts and observe the indicated display.
In steps D and E of CAL
4
, a voltage applied that is not within the calibration
range of the instrument will cause the calibration process to be aborted after 20
seconds and return the display to CAL
0
. Check the calibration set-up before
attempting to recalibrate.
In step C, of CAL
5
, the display will first indicate what the display is and after
2 seconds indicate the current value.
In step D, of CAL
5
, when the Select button is pressed, the display will
increment first slowly and then more rapidly. The button can be released and
pressed again to increment slowly when the desired value is approached.
NOTE:
*
A decimal point will be
placed in this position
for cold junction.
1
TC
0075F
1
CJ
023.9F
Alarm high value
1
SH
0800F
Alarm low value
1
SL
-045F
Hysteresis
1
Hy
0005F
PARAMETER
MNEMONICS
DATA
Thermocouple temperature
UNIT ADDRESS
Reference junction temp.
DISPLAY
“OPEN”
“EEEE”
PROBABLE CAUSES
- incorrect power up/down due to voltage spike
- broken or burned-out thermocouple
- excessive thermocouple voltage
- excessive negative thermocouple voltage (usually due to
reversed T/C connections) defect in analog circuit
“888.88”
Or
“- - - -”
STEP
CAL. BUTTON
SEL. BUTTON
DISPLAY
A
X 10 secs.
CAL
0
B
X
CAL
4
C
X
In-0 Apply 0 mill/-3 µV
D
X
X
In-5 Apply 50 mill/-5 µV
E
X
X
CAL
0
*
It is not necessary to exit to the thermocouple display if further set-up or calibration are
required, just press the “SEL” button. While in CAL
0
, select the desired CAL #.
F
X
888.8
8
Then TC Disp.
*
CAL 4 ZERO AND SPAN CALIBRATION