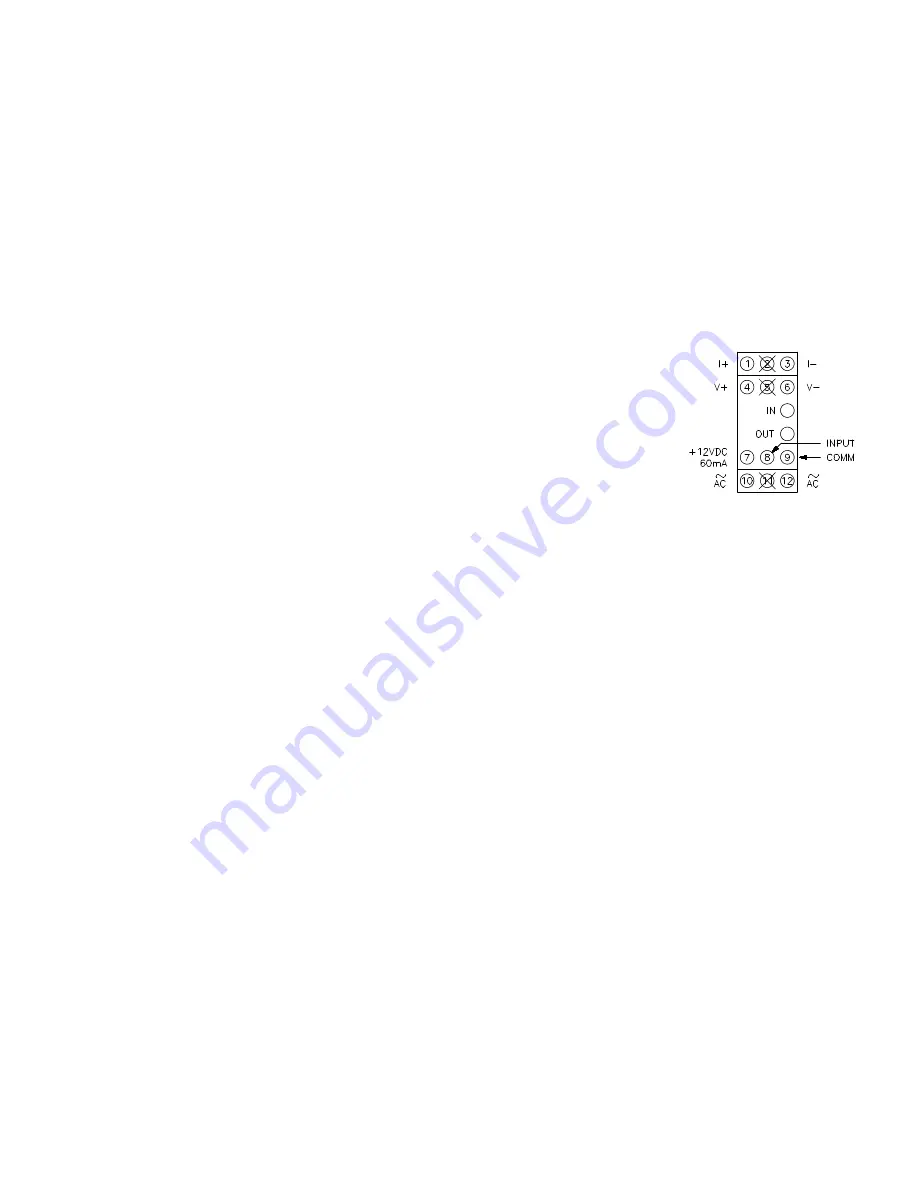
3
EMC INSTALLATION GUIDELINES
Although this unit is designed with a high degree of immunity to
ElectroMagnetic Interference (EMI), proper installation and wiring methods
must be followed to ensure compatibility in each application. The type of the
electrical noise, source or coupling method into the unit may be different for
various installations. The unit becomes more immune to EMI with fewer I/O
connections. Cable length, routing, and shield termination are very important
and can mean the difference between a successful installation or troublesome
installation.
Listed below are some EMC guidelines for successful installation in an
industrial environment.
1. Use shielded (screened) cables for all Signal and Control inputs. The shield
(screen) pigtail connection should be made as short as possible. The
connection point for the shield depends somewhat upon the application.
Listed below are the recommended methods of connecting the shield, in order
of their effectiveness.
a. Connect the shield only at the rail where the unit is mounted to earth
ground (protective earth).
b. Connect the shield to earth ground at both ends of the cable, usually when
the noise source frequency is above 1 MHz.
c. Connect the shield to common of the unit and leave the other end of the
shield unconnected and insulated from earth ground.
2. Never run Signal or Control cables in the same conduit or raceway with AC
power lines, conductors feeding motors, solenoids, SCR controls, and
heaters, etc. The cables should be run in metal conduit that is properly
grounded. This is especially useful in applications where cable runs are long
and portable two-way radios are used in close proximity or if the installation
is near a commercial radio transmitter.
3. Signal or Control cables within an enclosure should be routed as far away as
possible from contactors, control relays, transformers, and other noisy
components.
4. In extremely high EMI environments, the use of external EMI suppression
devices, such as ferrite suppression cores, is effective. Install them on Signal
and Control cables as close to the unit as possible. Loop the cable through the
core several times or use multiple cores on each cable for additional
protection. Install line filters on the power input cable to the unit to suppress
power line interference. Install them near the power entry point of the
enclosure. The following EMI suppression devices (or equivalent) are
recommended:
Ferrite Suppression Cores for signal and control cables:
Fair-Rite # 0443167251 (RLC #FCOR0000)
TDK # ZCAT3035-1330A
Steward #28B2029-0A0
Line Filters for input power cables:
Schaffner # FN610-1/07 (RLC #LFIL0000)
Schaffner # FN670-1.8/07
Corcom #1VR3
Note: Reference manufacturer’s instructions when installing a line filter.
5. Long cable runs are more susceptible to EMI pickup than short cable runs.
Therefore, keep cable runs as short as possible.
WIRING CONNECTIONS
All conductors should meet voltage and current ratings for each terminal.
Also cabling should conform to appropriate standards of good installation, local
codes and regulations. It is recommended that power supplied to the unit (AC
or DC) be protected by a fuse or circuit breaker.
POWER AND OUTPUT CONNECTIONS
AC Power
Primary AC power is connected to terminals 10 and 12 (labeled AC). For best
results, the AC Power should be relatively “clean” and within the specified
variation limits. Drawing power from heavily loaded circuits or from circuits
that also power loads that cycle on and off, should be avoided.
DC Power
The DC power is connected to terminals 10 and 12. The DC plus (+) power
is connected to terminal 10 and the mius (-) is connected to terminal 12.
It is recommended that separate supplies be used for sensor power and unit
power. Using the same supply for both will negate isolation between input and
power.
Current Output
When using Operating Mode 3 or 4, the output device is connected to
terminals 1(I+) and 3 (I-).
Voltage Output
When using Operating Mode 1 or 2, the output device is connected to
terminals 4 (V+) and 6 (V-).
Note: Although signals are present at
voltage and current outputs at the
same time, only the selected mode is
in calibration at any one time.
Example: Operating Mode 2 is
selected. The voltage level present
at the voltage terminals is in
calibration, but the signal
appearing at the current terminals
does not conform to either of the
current output modes.