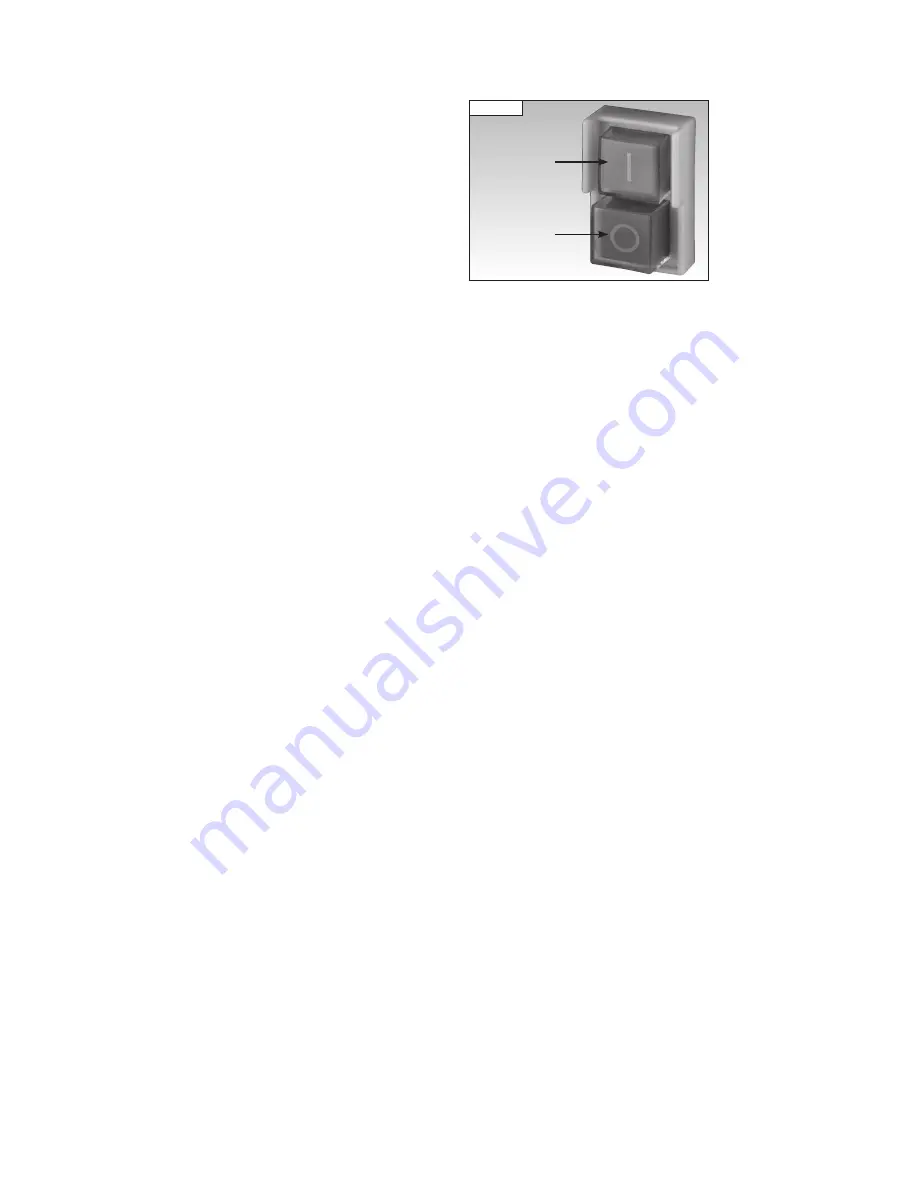
20
11. Operation
Off
Fig 11.20
On
Operating the Lathe
To turn the lathe on, press the green switch marked ‘I’ on the switch situated
on the lathe bed at the opposite end to the headstock, as shown in
Fig
11.20
.
To stop the machine, press the red button marked ‘O’ on the control panel as
shown in
Fig 11.20
.
In the Event of a Blockage or if the Machine Stalls
If the lathe stalls due to a dig in, simply removing the turning tool from the
work piece will normally allow the work piece to start turning again.
In the event of a blockage (for example, if the work piece becomes trapped
against a fixed part of the machine) switch off the machine immediately, by
pressing the red button marked ‘O’ on the switch.
Locate and rectify the source of the blockage and ensure that the work piece
can be rotated freely by hand before attempting to re-start the machine.
To re-start the machine, press the green button marked ‘I’ on the switch.
In the Event of a Power Failure
The lathe is fitted with a no volt release (NVR) switch to protect the user
against automatic starting of the machine when power is restored after a
power failure.
In the event of a power failure, first locate and rectify the source of the
failure. If the fault is within the power circuit of the workshop, there may be
an underlying cause (circuit overload etc.) that should be investigated by a
qualified electrician, before attempting to restore the power source.
Once the power is restored, the machine can be re-started by pressing the
green button marked ‘I’ on the switch.
Summary of Contents for DML250
Page 35: ...35 ...