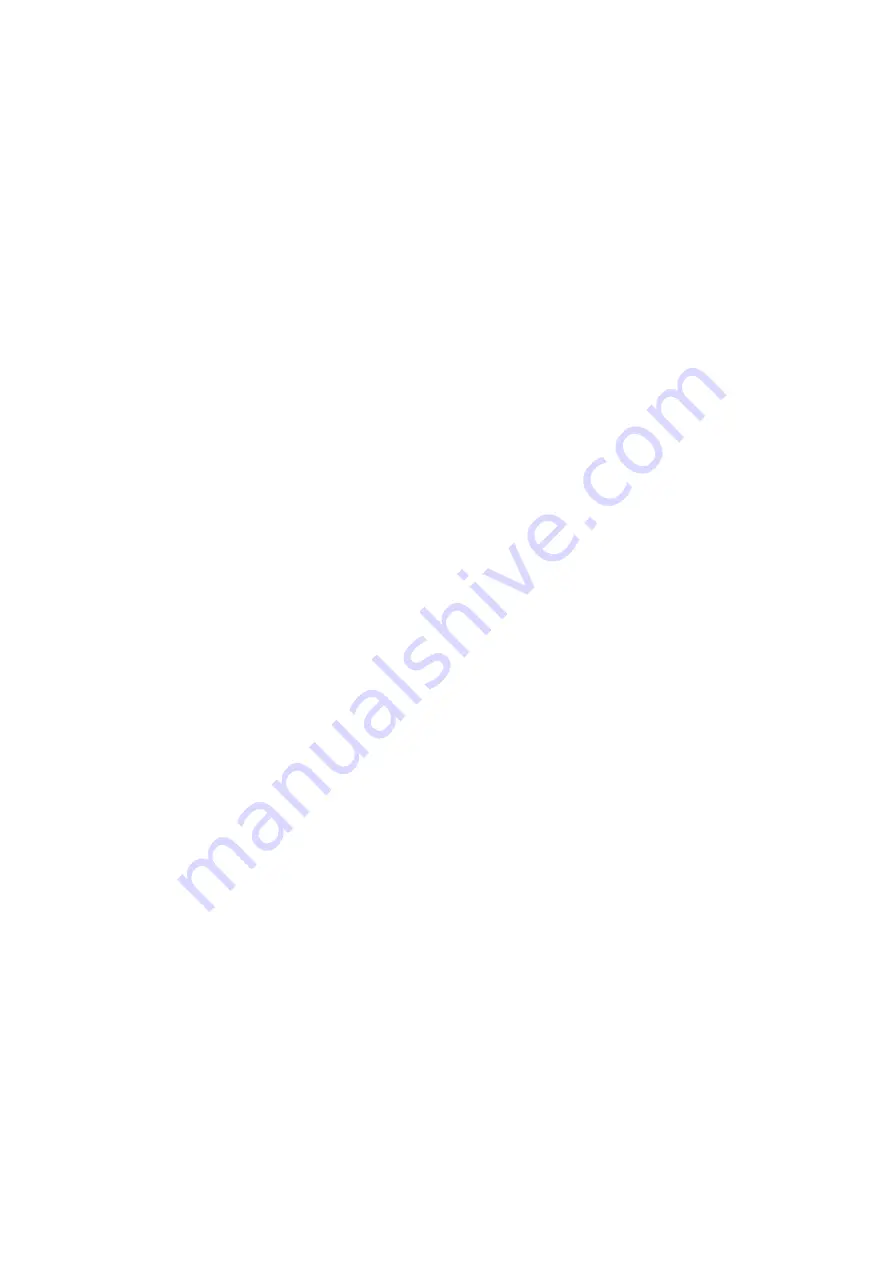
Max distance between centres
24” (610mm)
Max bowl Dia. over bed
9” (229mm)
Max spindle Dia.
6” (152mm)
Motor
230 V 50Hz 2.5A
Capacitor start & run drip proof type
Motor Power
430w (p1) 250w (p2)
Motor Speed
1425 min-1
Noise emission
< 85dB(A)
Spindle Speeds
450, 950, 1500, 2000
Drive
Poly V belt
Main Bearing
Deep groove ball
Spindle Nose
3/4”ø whit. x 16tpi
Overall Dimensions
Length
51” (1295mm)
Depth
12” (305mm)
Height
11
3
/
4
” (298mm)
Weight
40kg
3.
Specification
4.
Assembly Instructions
HEADSTOCK SPINDLE AND TAILSTOCK BARREL BORED TO SUIT NO.1 MORSE TAPER SHANK.
SPINDLE FLATTED TO SUIT 9/16" WHITWORTH. WRENCH TO FACILITATE FITTING AND RELEASE OF
SPINDLE NOSE ATTACHMENTS SUPPLIED.
Unpacking
NOTE:
Make sure that all items are included by checking against
Parts Diagram / Parts List. Do not discard any packaging
material before carrying out this check.
WARNING:
To avoid injury, do not attempt to run or use this
machine until all parts are fitted and working satisfactorily.
Installation
Before assembling and using your lathe, you must have a sturdy
bench or stand for it. Alternatively the Record Power® DML24S
Leg Set. If you wish to build your own bench, remember that the
lathe is heavy (see Specifications for correct weight). The bench
must not move during use.
WARNING
Inadequate strength of the bench could result in failure of the
bench and falling of the lathe. Serious injury could occur.
WARNING
The lathe must not shift or move. If there is movement when not
running, the movement will be exaggerated when turned on.
Serious injury could occur. To prevent movement, bolt the bench
to the floor and the lathe to the bench.
CAUTION
To avoid back injury, get help lifting the lathe. Bend your knees
lift with your legs not your back.
Wiring Instructions
The lathe supplied is fitted with a plug. The wires in the mains
lead are coloured in accordance with the following codes.
Green & Yellow:
Earth
Blue:
Neutral
Brown:
Live
If a new plug is fitted
The green and yellow wire must be connected to the terminal
that is marked with the letter ‘E’ or by the earth symbol.
The blue wire must be connected to the terminal which is
marked with the letter ‘N’.
The brown wire must be connected the terminal which is marked
with the letter ‘L’
Machines for use in the UK are fitted with a BS1363 amp. 3 pin
plug. Replacement of the power cable should only be carried out
by a qualified electrician.
R.C.D (Residual Current Device)
For your additional safety, we always recommend the use of a
residual current breaker, or Earth leakage circuit breaker.
Summary of Contents for DML24X-MK2
Page 10: ...8 Spare Part Identification ...