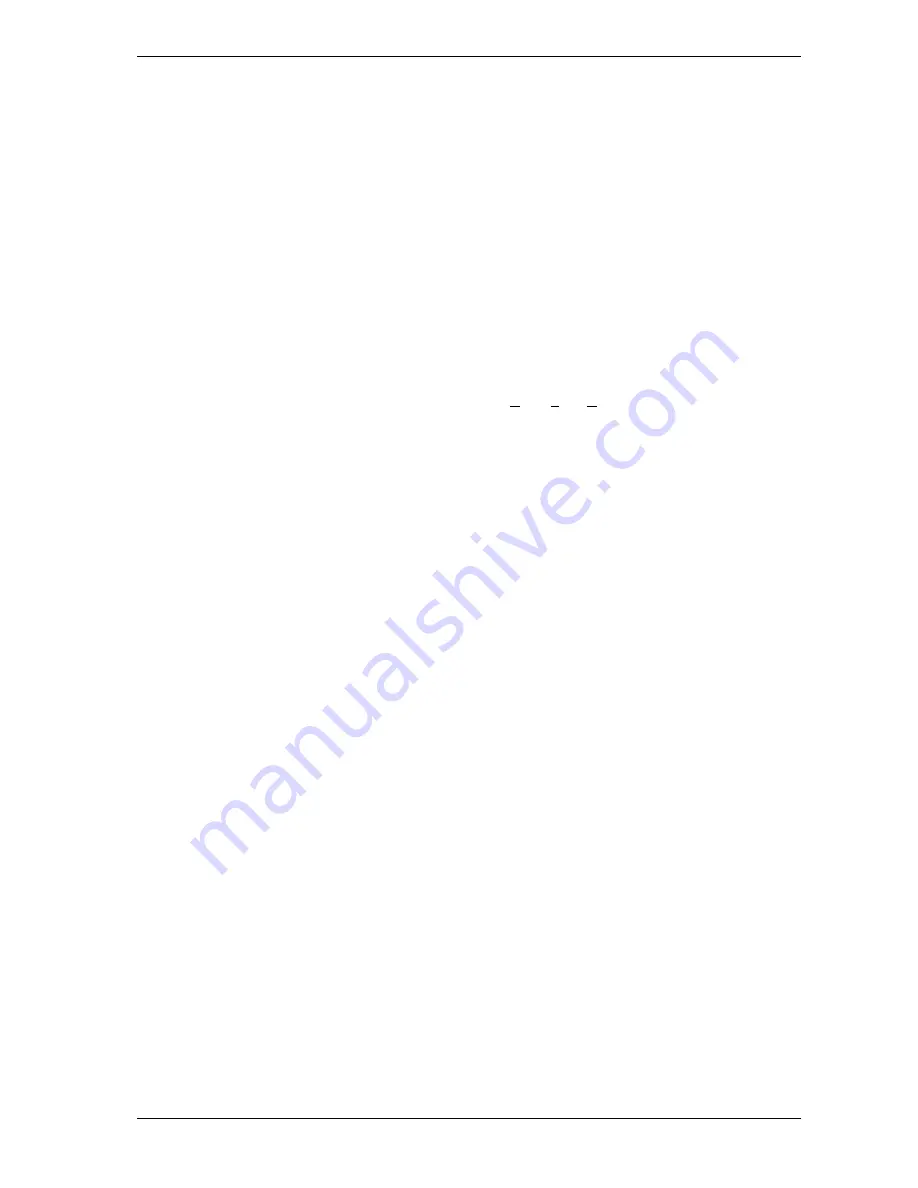
RM-216 C.10 Easy Line Documentation
RDN 10000029
15
13.05.2014
9 Details on the equipment function
Differential pressure controlled cleaning
The cleaning is controlled by means of two
∆
p switch points which can be set independently of one
another. It starts when the value
∆
p-MAX is reached. All connected solenoid valves are controlled using
the preset values for the pulse time and the interval time, starting with the interval time. If the differential
pressure reaches the value
∆
p-MIN, cleaning stops. To monitor the filter, a
∆
p alarm switch point (
∆
p
alarm) can be set.
Cleaning starts at the first valve. If cleaning is interrupted using the
∆
p controller or the start/stop input
D1, D2, the controller sequence is continued with the next cleaning process. The cleaning then starts at
the valve following the last valve activated.
If the control is reactivated following a mains voltage failure, a restart is carried out.
Input E1, E2 “Down time cleaning”
(terminals 10, 11)
If the control is working in DTC mode 1 or DTC mode 2 (Down-Time-Cleaning mode. See also section
6.3), the control must be switched on and off via input E1, E2. The input should be operated in isolation.
Ideally, the auxiliary contact of the fan contactor should be connected here.
Closing the contact on input E1, E2 switches on the control unit.
In DTC mode 1, opening the contact on input E1, E2 executes the down time cleaning cycles and then
switches the device off. In DTC mode 2, the same function is only carried out if differential pressure
exceeded the value
∆
p DTC max during the last operating period.
In DTC mode 3, the down-time cleaning cycles are activated if differential pressure exceeded the value
∆
p DTC max during the last operating period and then fell below the value
∆
p DTC min.
Relay output S1, S2 to control extractor elements
(terminals 8, 9)
If automatic components for dust removal (extractor elements) are fitted, these need to be in operation
during cleaning and during down time cleaning. Connect the cut-out for controlling these drive units to the
isolated output S1, S2.
“Alarm” relay output A1, A2, A3
(terminals 5, 6, 7)
As soon as the supply voltage is present on the RM-216 C, relay contact A1, A2 closes (terminals 5, 6)
and contact A2, A3 opens (terminals 6, 7). In the following situations, relay contact A1, A2 opens and
contact A2, A3 closes:
Supply voltage failure
Failure of a voltage internal to the equipment
Fault in a connected I/O module
Total number of valves is set incorrectly (parameter P06)
The
∆
p alarm switching point has been exceeded.