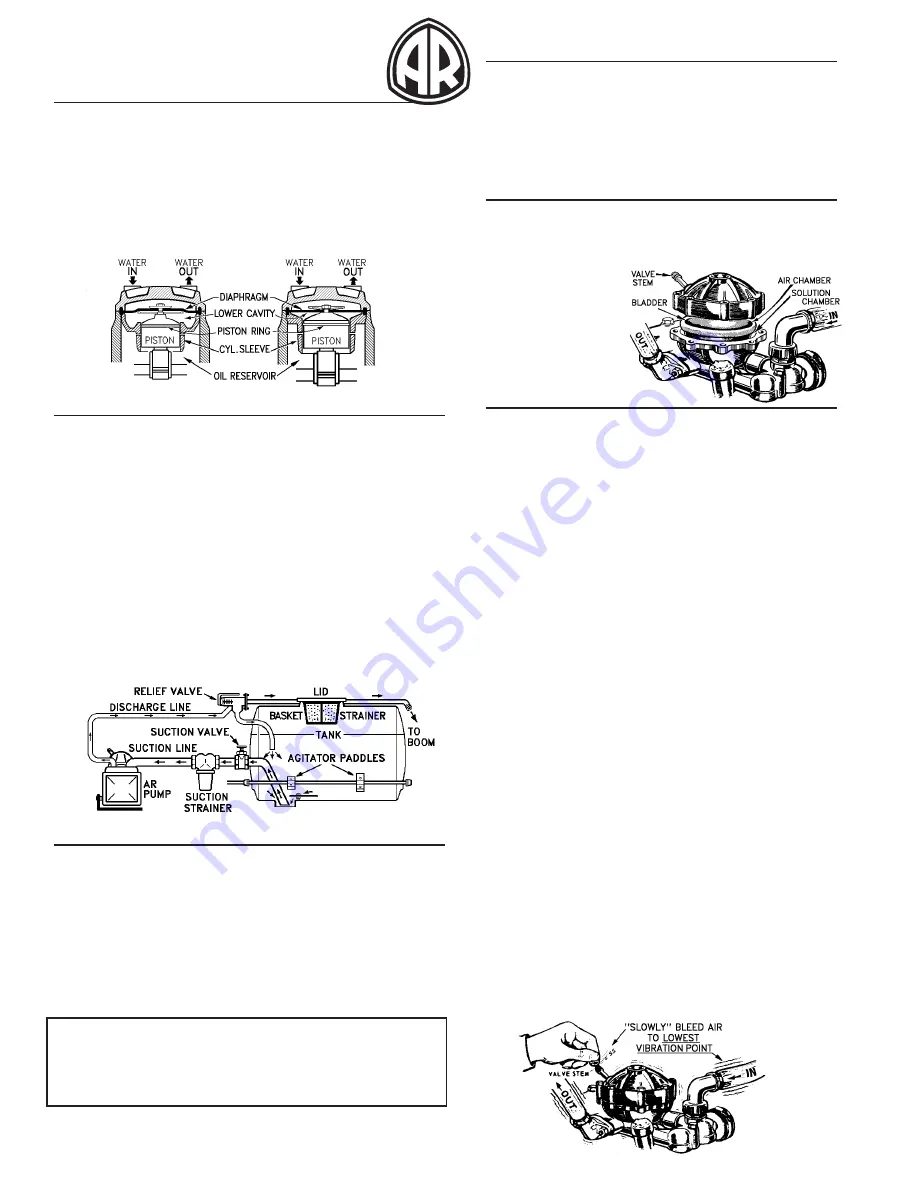
Maintain proper oil level
The crankcase oil serves two important functions. The oil lu-
bricates all moving parts in the pump
and
affects the hydraulic
action for optimal pump capacity. The pump diaphragms are
supported by the crankcase oil during each pressure upstroke of
the piston: to assure maximum performance of your pump and
protect your pump diaphragms
maintain the oil level
marked on
the transparent filler spout.
How the AR diaphragm pump works
Each
downstroke
of the piston/diaphragm assembly draws spray
material into the upper head cavity. Simultaneously, crankcase
oil from the lower head cavity is expelled as the cycling piston
ring passes a vent in the cylinder sleeve,
see above illustration
.
Each upstroke of the piston injects a measured amount of oil
back into the lower head cavity, expanding the diaphragm as
the piston cycle tops-out and expelling the spray material from
the upper chamber.
Low oil level lowers performance.
For optimal hydraulic diaphragm actuation, piston assembly
lubrication, diaphragm membrane support: check the oil level
frequently- the transparent oil-fill makes level checks easy.
Maintain the indicated level.
Don’t starve the suction
The pump will not suffer if run dry when the tank is empty.
A
clogged suction strainer
or
closed suction valve
, however,
will
starve the pump
and cause premature diaphragm failure.
When mixing powders
, avoid clogging the suction strainer by
sluicing
heavy concentrations of wettable powders through the
lid basket into an already half-filled tank. Agitator paddles will
mix the powder into solution, preventing material deposits at
the bottom of the tank which plug the suction strainer.
The suction valve
is provided to shut off flow from the tank:
for emergency plumbing repair or for strainer cleaning.
To
prevent possible pump damage, SHUTDOWN SYSTEM before
closing the suction valve.
How clean is your water source? You may need to clean your
suction strainer before each tank refill.
Do not over-speed your pump
Refer to the performance chart for your specific pump to
find the
maximum operating speed
. Your pump is de-
signed to operate at or below this speed. Over-speeding
will cause valves to prematurely fail and could cause
other internal damage.
Before pump operation
Check tightness of suction line fittings and strainer cap.
Follow airdome pressurizing instructions, below.
Pressurizing the air dome
Piston and piston-like pumps (diaphragm pumps) will
have pulsation vibration,
water hammer
, because of the
rapid change in piston direction. The
air dome
pulsation
dampener reduces vibration by providing a cushion of air
to bump against:
inflate or deflate this cushion to reduce
vibration.
The AR airdome uses a rubber bladder to sepa-
rate the air cushion from the spray material. The bladder
eliminates water-logging problems common in static-air
type dampeners.
If you have a pressure gauge
the basic rule is to charge
the air dome to 10% of the system working pressure:
for a handgun pressure of 100psi, we recommend an air
dome pressure of 10psi. Always shut down pump before
adding air to the airdome with either a compressor or
manual pump. The air cushion is small, making pres-
sure checks challenging. Take care applying the pressure
gauge evenly on the air valve to prevent air from leaking
out of the air dome. It is not uncommon to lose 5-10 psi
checking the pressure.
If you do not have a pressure gauge
charge the air
dome
with the pump shut down
to 70-80 psi: sufficient
for 700 psi working pressure. Start up the pump (expect
pump vibration) and adjust the relief valve to your de-
sired working pressure. Slowly bleed off air dome pressure
while watching the vibration of the pump discharge hose.
Continue bleeding until vibration is eliminated or mini-
mized. Replace stem cap tightly.
It may take a couple
attempts to get the feel for
minimum vibration.
Too much air in the air dome is as bad as too little.
PUMP OPERATION
Floating
Diaphragm
Bolt
Design
Fixed
Diaphragm
Bolt
Design
Summary of Contents for Pakblast 50 Gal
Page 2: ......
Page 19: ...xvii Read this manual completely before operating follow all safety instructions ...
Page 28: ...Pak Blast 50 gallon 10 CHEMICAL CONTAINERS INC 800 346 7867 ...
Page 42: ...10 1 11 12 13 8 12 13 5 4 6 7 14 9 2 3 right left ...
Page 56: ...Pak Blast 50 gallon 38 CHEMICAL CONTAINERS INC 800 346 7867 ...