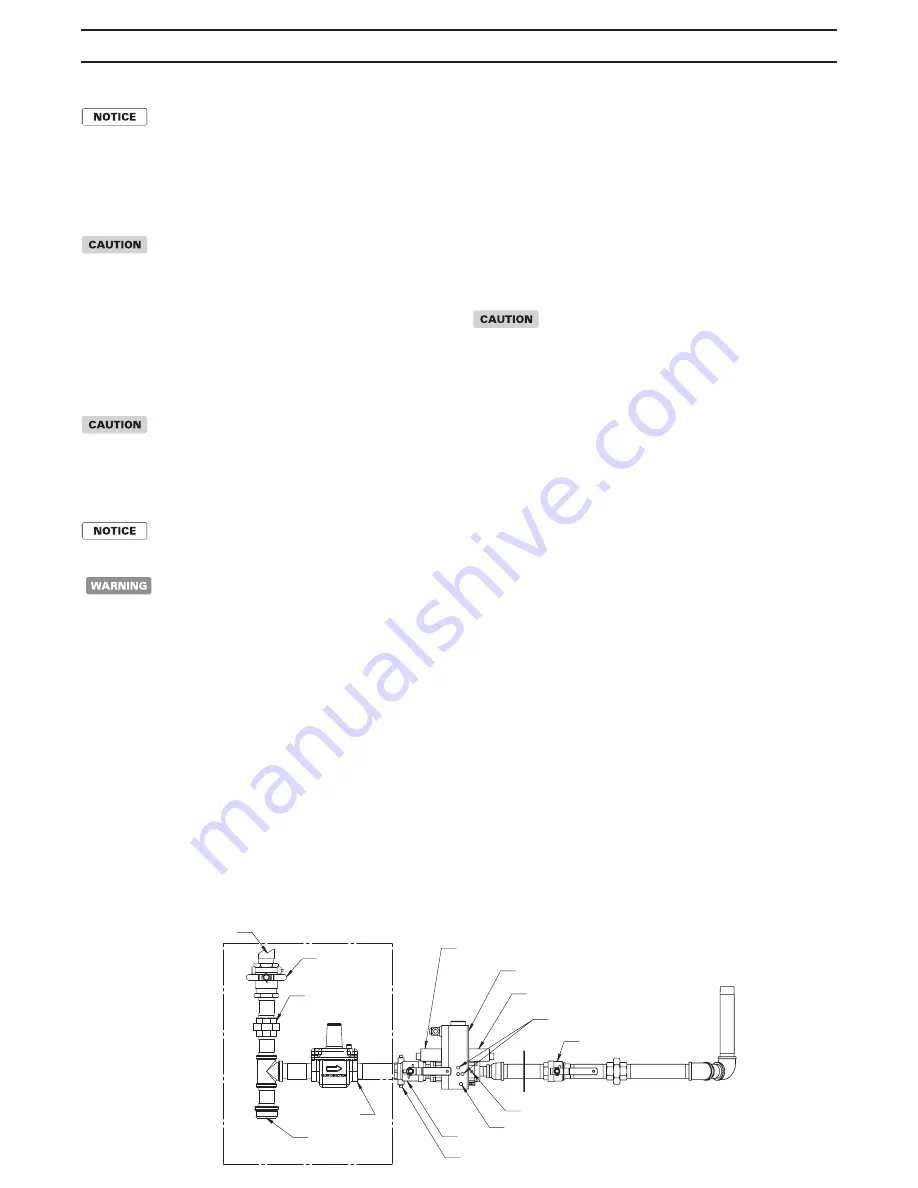
27
Cast Iron Condensing Boilers – Installation Manual
Torus Stainless Steel Condensing Boilers & Water Heaters – Installation Manual
Whenever the gas supply piping is pressure tested the
boiler gas controls must be protected. If the test pressure
is equal to, or less than
1/2 psig, 3.5 kPa isolate the boiler
by closing its' manual shut off valve, see Figure 17. If the
test pressure is greater than, or equal to
1/2 psig, 3.5 kPa,
disconnect the boiler and its individual shut-off valve.
ELECTRICAL WIRING
Electrical Power Connections
Label all wires prior to disconnection when
servicing controls. Wiring errors can cause
improper and dangerous operation! Verify
proper operation after servicing.
ATTENTION. Au moment de l'entretien des
com-mandes, étiquetez tous les fils avant de les
débrancher. Des erreurs de câblage peuvent
entraîner un fonctionnement inadéquat et
dangereux. S'assurer que l'appareil fonctionne
adéquatement une fois l'entretirn terminé.
The electrical connections to this boiler/water heater must
be made in accordance with all applicable local codes and
the latest revision of the National Electrical Code, ANSI /
NFPA-70. Installation should also conform with CSA C22.1
Canadian Electrical Code Part I if installed in Canada. A
separate circuit breaker must be installed per boiler - (if
required, the optional local pump FLA must be
incorporated and sized accordingly). A properly rated shut-
off switch should be located at the boiler. The boiler must
be grounded in accordance with the authority having
jurisdiction, or if none, the latest revision of the National
Electrical Code, ANSI/NFPA-70.
Line voltage field wiring of any controls or other devices must
use copper conductors with a minimum size of #14 awg.
Refer to point of connection diagram in back of this manual
and the wiring diagram supplied with the boiler for proper
wiring connections.
A minimum of (3 in WC) and maximum of
(14 in WC) must be maintained to the inlet of
the boiler/water heater gas train not to exceed
a maximum of (1 in WC) drop when firing from
minimum input to full load of the gas supply
line and all the appliances running.
Always use a wrench on the gas valve body
when making gas connections to it. Never
over-tighten the piping entering the gas
valve body or gas valve failure may result!
Safe lighting and other performance criteria were met
with the gas manifold and control assembly provided
on the boiler/water heater. All gas connections MUST
be leak tested before putting the boiler into operation.
Never use an open flame to test for
gas leaks. Always use an approved leak
detection method. Failure to comply with
this warning can cause extensive property
damage, severe personal injury or death!
Gas train must be isolated when purging the
gas line prior to commissioning the boiler.
Corruption of the gas train components with
debris and cutting oils can reduce reliable
operation which can have a negative effect
on the operation & manufacturers warranty
of the Dungs gas valve. The factory supplied
Dungs MBC modulation gas valve, see Figure
17, incorporates an internal filter that must be
inspected and changed at required intervals.
Reference the Dungs MBC Installation
Instructions - 264541 for detailed instructions.
Combined with clean gas pipes and good
plumbing practices (such as installing a drip
leg), should adequately protect the MBC
valve seat, regulator and internal orifices from
clogging or damage. However, site conditions
might warrant an additional filter. This should
be installed upstream of the appliance gas
regulator to the unit.
Figure 17 - Gas Supply Piping
MAIN GAS
VALVE
PRESSURE
REGULATOR
SUPPLIED BY OTHERS
SEDIMENT TRAP
AND DRIP LEG
FROM GAS SUPPLY
GROUND
UNION
FIRING VALVE
DUNGS
VALVE
MANUAL SHUT-OFF
VALVE
LOW GAS PRESSURE SWITCH
(ON APPLICABLE MODELS)
HIGH GAS PRESSURE SWITCH
(ON APPLICABLE MODELS)
SUPPLY PRESSURE TEST PORT
RIOM-0312_A
LOW FIRE GAS PRESSURE ADJUSTMENT
CSD-1 TEST PORTS
HIGH FIRE GAS PRESSURE ADJUSTMENT