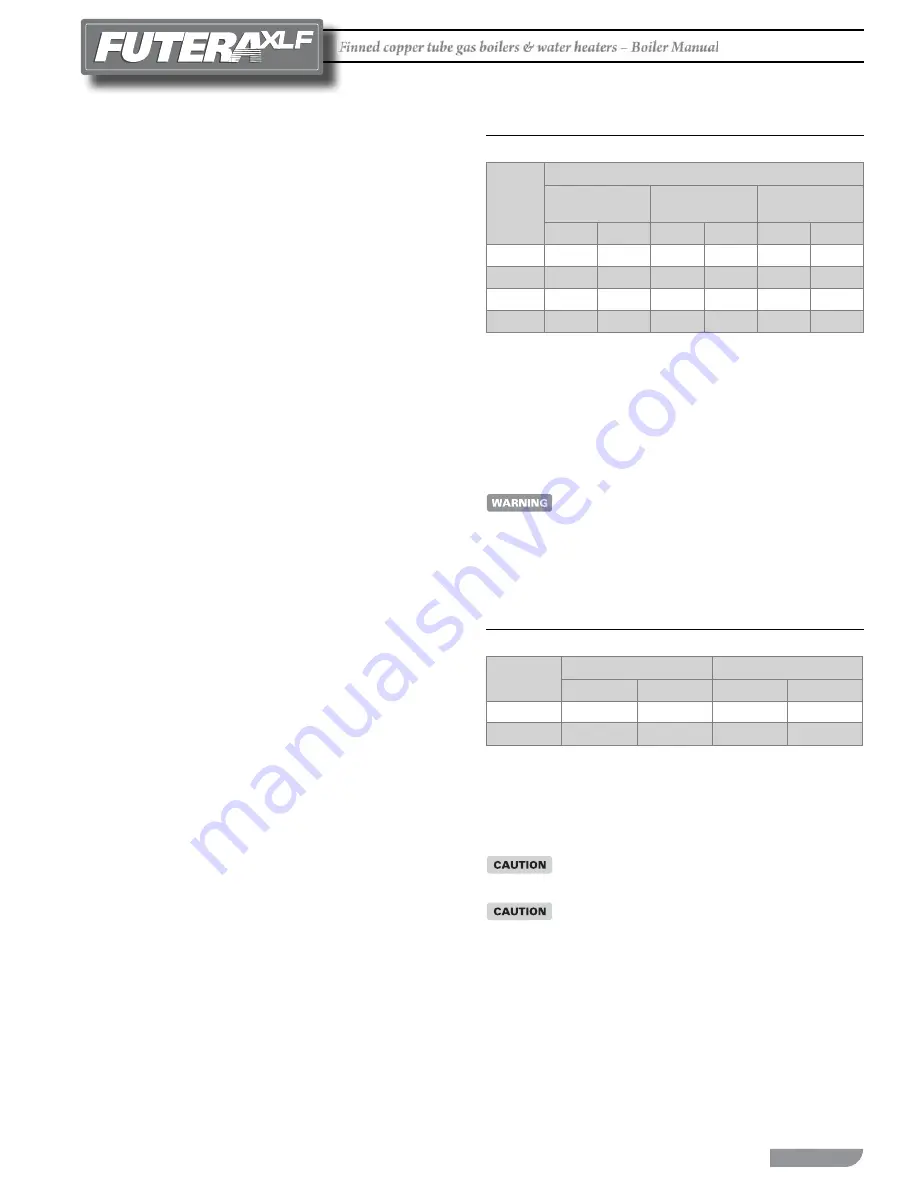
F
d
b
b l
&
h
B l M
l
Finned copper tube gas boilers & water heaters – Boiler Manual
5
F
F
All air from inside the building
If the Futera XLF is to be located in a confi ned space, the minimum
clearances listed in Table 1, page 4 must be maintained between it
and any combustible construction. When installed in a confi ned
space without the intake air option (as in Figure 5, page 10 through
Figure 8, page 13) two permanent openings communicating with
an additional room(s) are required. The combined volume of
these spaces must have suffi cient volume to meet the criteria for an
unconfi ned space. Th e total air requirements of all gas utilization
equipment, fireplaces, wood stoves or any type of exhaust fan
must be considered when making this determination. Each
opening must have a minimum free area of 1 in
2
/1000 Btu/hr,
2200 mm
2
/kW based on the total input rating of ALL gas utilization
equipment in the confi ned area. Each opening must be no less than
100 in
2
, 64,516 mm
2
in size. The upper opening must be within
12 inches, 305 mm of, but not less than 3 inches, 76 mm from, the
top of the enclosure. Th e bott om opening must be within 12 inches,
305 mm of, but not less than 3 inches, 76 mm from, the bott om of
the enclosure.
All air from outside the building
When installed in a confi ned space without utilizing the intake air
option two permanent openings communicating directly with, or
by ducts to, the outdoors or spaces that freely communicate with
the outdoors must be present. Th e upper opening must be within
12 inches, 305 mm of, but not less than 3 inches, 76 mm from, the
top of the enclosure. Th e bott om opening must be within 12 inches,
305 mm of, but not less than 3 inches, 76 mm from, the bott om of
the enclosure.
Where directly communicating with the outdoors or communicating
with the outdoors through vertical ducts, each opening shall have a
minimum free area of 1 in
2
/4000 Btu/hr, 550 mm
2
/kW of the total
input rating of all of the equipment in the enclosure.
Where communicating with the outdoors through horizontal ducts,
each opening shall have a minimum free area of 1 in
2
/2000 Btu/hr,
1100 mm
2
/kW of the total input rating of all of the equipment in
the enclosure.
When ducts are used, they must have the same cross-sectional area
as the free area of the opening to which they connect.
When calculating the free area necessary to meet the make-up air
requirements of the enclosure, consideration must be given to the
blockage eff ects of louvers, grills and screens. Screens must have a
minimum mesh size of 1/4 inch, 6.4 mm. If the free area through a
louver or grill is not known, ducts should be sized per Table 2.
Canadian installations must comply with CSA B149.1 when air
supply is provided by natural air fl ow from the outdoors for natural
draft , partial fan-assisted, fan-assisted, or power draft -assisted burners,
there shall be a permanent air supply opening(s) having a cross-
sectional area of not less than 1 in
2
per 7,000 Btuh (310 mm
2
per
kW) up to and including 1 million Btuh, plus 1 in
2
per 14,000 Btuh
(155 mm
2
per kW) in excess of 1 million Btuh.
Table 2
Make-up Air Louver Sizing
Input
MBH
Required cross-sectional area
Wire screen
¼ inch (6.4 mm)
Metal louvers
75% free area
Wooden louvers
25% free area
in
2
cm
2
in
2
cm
2
in
2
cm
2
2500
625
4031
833
5382
2500
16127
3000
750
4838
1000
6452
3000
19354
3500
875
5645
1167
7522
3500
22581
4000
1000
6452
1334
8592
4000
25808
Intake air option — General guidelines
Th is confi guration provides combustion air directly to the boiler/
water heater’s air intake adapter using a dedicated pipe when using
the direct vent option. Combustion air can be drawn in horizontally
through the same outside wall which terminates the exhaust gases
or vertically through the roof, see Figure 1, page 8 through Figure 4,
page 9.
Common intake air systems may be used provided the
common duct is sized properly. An intake combustion
air damper should be installed if the common vent
option is used in the intake air pipe of each heater.
Improper installation can result in excessive levels of
carbon monoxide which can cause severe personal
injury or death!
Table 3
Intake air pipe sizing
Input
MBH
Vertical
Horizontal
in
mm
in
mm
2500/3000
10
254
8
203
3500/4000
12
305
10
254
All joints in metal intake air systems must be secured using
corrosion resistant fasteners and sealed using a suitable Silicone
caulk . If PVC or CPVC is used, the joints must be
cleaned with a suitable solvent and connected using a solvent based
PVC cement.
Th e combustion air system MUST be supported by the
building structure not the boiler/water heater.
A combustion air damper interlocked with the unit
should be installed in the intake air pipe when the
infi ltration of subfreezing air could occur, otherwise
the unit could freeze up voiding the warranty!
Intake air option – Vertical guidelines
Th e maximum equivalent length for the vertical intake air pipe is
100 ft , 30.5 m. Each 90
o
elbow and the intake air terminal are equal
to 10 linear ft , 3.0 m of pipe, see Table 3.
An approved, nonrestrictive intake air terminal must be used. Th e
intake air terminal must terminate as shown in Figure 3, page 9. Th e
penetration point in the roof must be properly fl ashed and sealed.