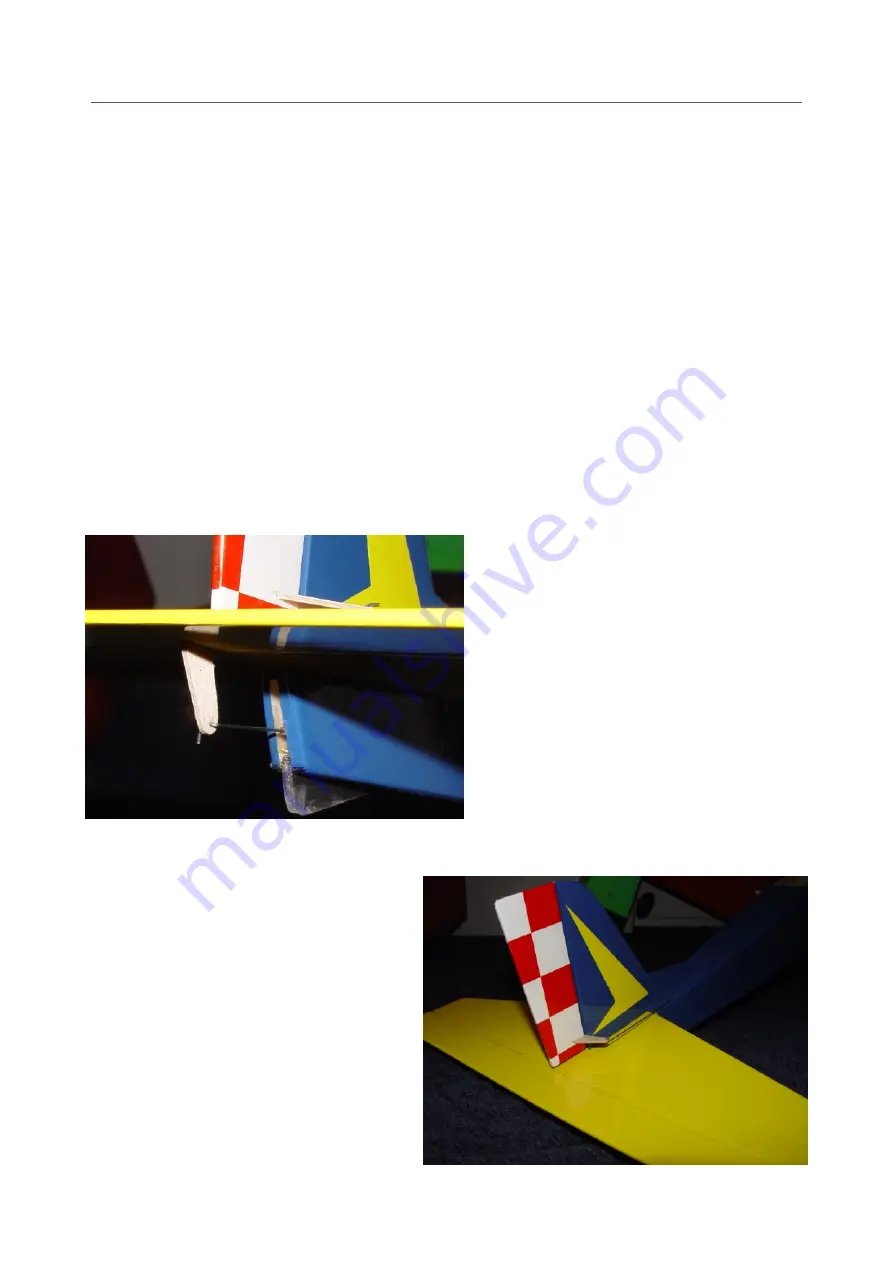
Building Instructions JIMMY
Page
van
15
20
Finishing
Wing and fuselage are now ready to get their final finish. Sand everything smooth, and
round the corners of the fuselage. Do not overdo it, avoid reducing the glue areas too
much. The simplest way to finish all surfaces and open structures is to use iron-on
covering film. It is important to apply the covering at a low temperature setting of your
iron to reduce initial shrinking, and only when everything is attached properly raise the
temperature to tighten the covering and remove any wrinkles. This is especially important
with open structures, i.e. the wing, which should be covered at low setting on top and
bottom first, and only then raise the setting to tighten it evenly. Be careful not to introduce
warping of the wing, but when you do you can iron those out by ”counter-warping” the
wing by weighting one half down on the board and carefully rotate the other tip by hand,
reheat the covering and let it cool before you release it.
It will be difficult to describe the details of iron-on covering in a few words, best is to let
an experienced modeller show you how it’s done, or refer to the instructions of the iron-
on film supplier, e.g. Solarfilm, Oracover and others.
As mentioned before, the tail surfaces
are best covered before final assembly.
Leave the area to be glued to the
fuselage free from covering.
Mark the position of the rudder horns,
cut a slot and glue the horns to the
control surfaces. Check the drawing for
the exact positioning of the horns.
Attach the elevator to the stabiliser with
sticky tape. Stick the tape to the top of
the stabiliser, leaving one half past the
edge to stick to the elevator. To ensure
a minimum hinge gap and a maximum
deflection angle, hold the elevator in a
downward attitude against the rear
edge of the stabiliser and push down
the tape onto the elevator.
Attach the rudder in the same way, pay
attention to the bevel on the front edge
of the rudder.